What are MES Interfaces?
What are MES Interfaces?
MES interfaces, integral to MES integration, are points of connection enabling data exchange between Manufacturing Execution Systems and other systems like ERP, SCADA, and MOM, as well as shop floor equipment. They facilitate real-time data collection from production machinery and sensors, transmitting it for analysis, and enable the transmission of instructions from higher-level systems to the shop floor. These interfaces come in various forms such as APIs, message queues, and standardized protocols like OPC and MQTT, selected based on system requirements and interoperability needs. In essence, MES interfaces ensure seamless communication, optimizing manufacturing operations efficiently.
Here are some notable MES (Manufacturing Execution System) software solutions:
- Siemens Opcenter (formerly known as SIMATIC IT and Camstar)
- Apriso FlexNet
- Aegis FactoryLogix
- SAP Manufacturing Execution (SAP ME)
- Wonderware MES (formerly known as Wonderware Operations Management)
- Rockwell Software MES
- Plex Manufacturing Cloud
- IQMS MES
- Lighthouse MES
- DELMIA Apriso MES
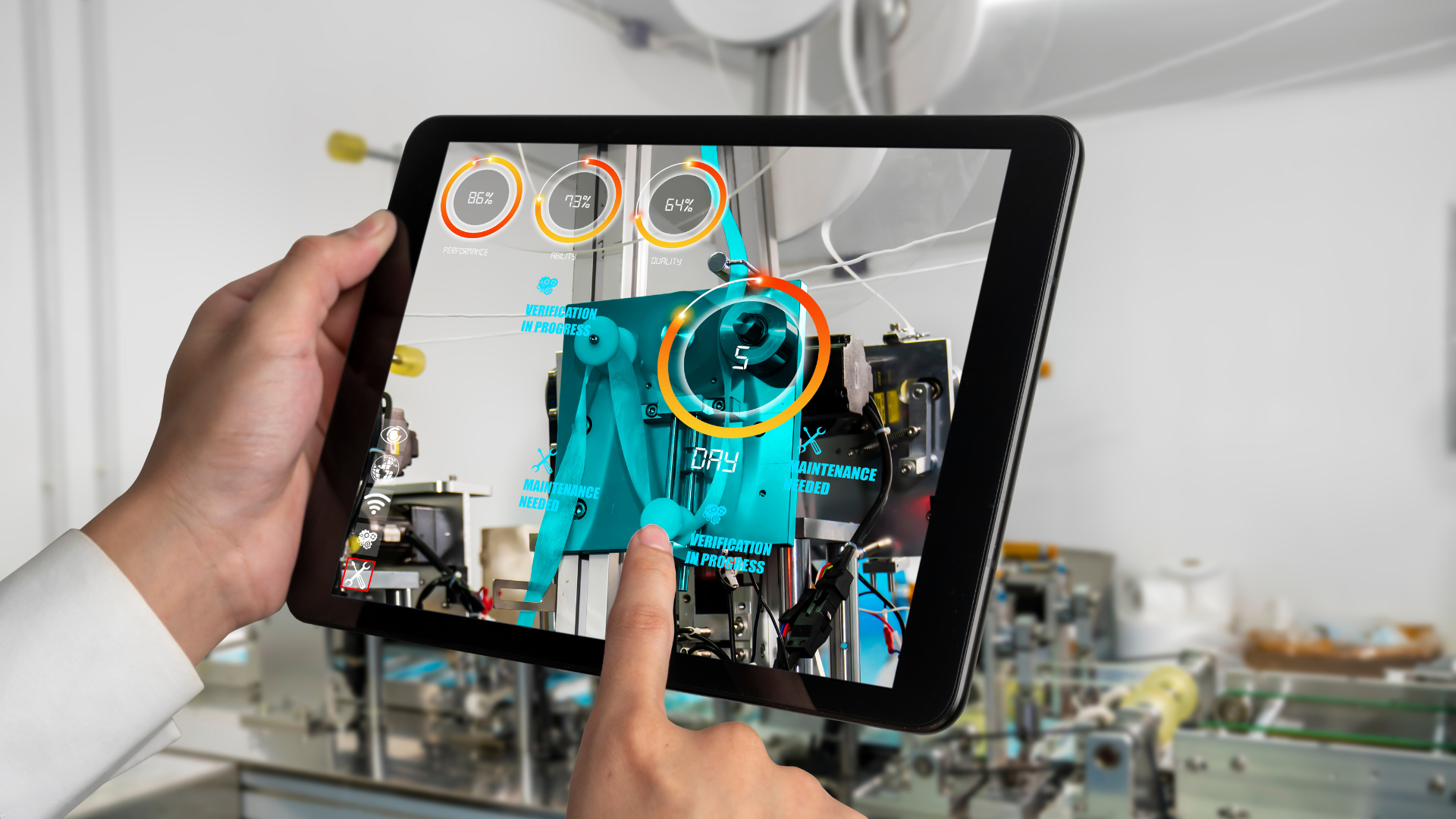
What Does MES Stand for?
MES stands for Manufacturing Execution System. A Manufacturing Execution System is a crucial component in the manufacturing industry, as it monitors, tracks, and documents the transformation of raw materials into finished goods. By providing real-time data on production processes, MES helps optimize operations, improve product quality, and ensure regulatory compliance. This system bridges the gap between enterprise resource planning (ERP) systems and the factory floor, offering valuable insights that drive efficiency and productivity in manufacturing environments.
What is the Role of MES?
The role of a Manufacturing Execution System (MES) is to manage and control production operations on the factory floor. MES software vendors provide tools that enable manufacturers to monitor real-time data, track product lifecycles, and ensure quality control. By integrating with enterprise systems and providing detailed insights into manufacturing processes, MES helps optimize production efficiency, reduce waste, and improve overall product quality. This system is essential for maintaining smooth operations and achieving operational excellence in today's competitive manufacturing landscape.
What is MES Integration?
MES integration involves connecting a Manufacturing Execution System (MES) with other enterprise systems, such as Enterprise Resource Planning (ERP) and supply chain management systems. This integration allows seamless data flow and real-time communication across various platforms, enhancing operational visibility and efficiency. By integrating MES, manufacturers can ensure that production processes are aligned with business objectives, improve decision-making based on accurate data, and streamline operations from the factory floor to the executive level. This holistic approach enables better resource management, reduces downtime, and boosts overall productivity.
What is the Difference Between MES and SAP?
The difference between MES (Manufacturing Execution System) and SAP lies in their primary functions and areas of focus within a manufacturing enterprise. MES is designed to manage and control production processes on the factory floor, providing real-time data and monitoring to optimize manufacturing operations, track product lifecycles, and ensure quality control. On the other hand, SAP (Systems, Applications, and Products) is a comprehensive enterprise resource planning (ERP) software that integrates various business processes, including finance, human resources, supply chain management, and more. While MES focuses specifically on manufacturing operations, SAP provides a broader scope of business management solutions, making it essential for overall enterprise planning and resource management. Together, they can work in tandem to provide a seamless and efficient workflow from production to business operations.
What is the Difference Between MES and ERP?
The difference between MES (Manufacturing Execution System) and ERP (Enterprise Resource Planning) lies in their scope and functions within a manufacturing organization. MES focuses specifically on the shop floor, managing and controlling production processes, tracking real-time data, and ensuring product quality. It provides detailed insights into manufacturing operations to optimize efficiency and productivity. In contrast, ERP encompasses a broader range of business functions, integrating various departments such as finance, human resources, supply chain, and customer relationship management. ERP provides a unified view of the entire enterprise, facilitating strategic planning and resource allocation. While MES enhances operational performance at the production level, ERP supports overall business management and coordination across the organization. Together, they create a comprehensive system for managing both manufacturing processes and business operations.
MES vs. ERP
MES (Manufacturing Execution System) focuses on managing and optimizing production processes on the factory floor with real-time data and monitoring. In contrast, ERP (Enterprise Resource Planning) integrates and oversees broader business functions such as finance, HR, and supply chain across the entire organization. Together, MES enhances operational efficiency while ERP ensures overall business coordination and strategic planning.
Is SAP and MES System?
SAP is not an MES (Manufacturing Execution System) but an ERP (Enterprise Resource Planning) system. While SAP provides comprehensive solutions for various business functions such as finance, human resources, and supply chain management, it does offer MES capabilities through its SAP Manufacturing Execution module. This module integrates with SAP's ERP system to provide real-time monitoring, control, and optimization of manufacturing processes. However, the core SAP system itself is primarily focused on broader enterprise management rather than the specific, detailed execution of manufacturing operations that a dedicated MES system handles.
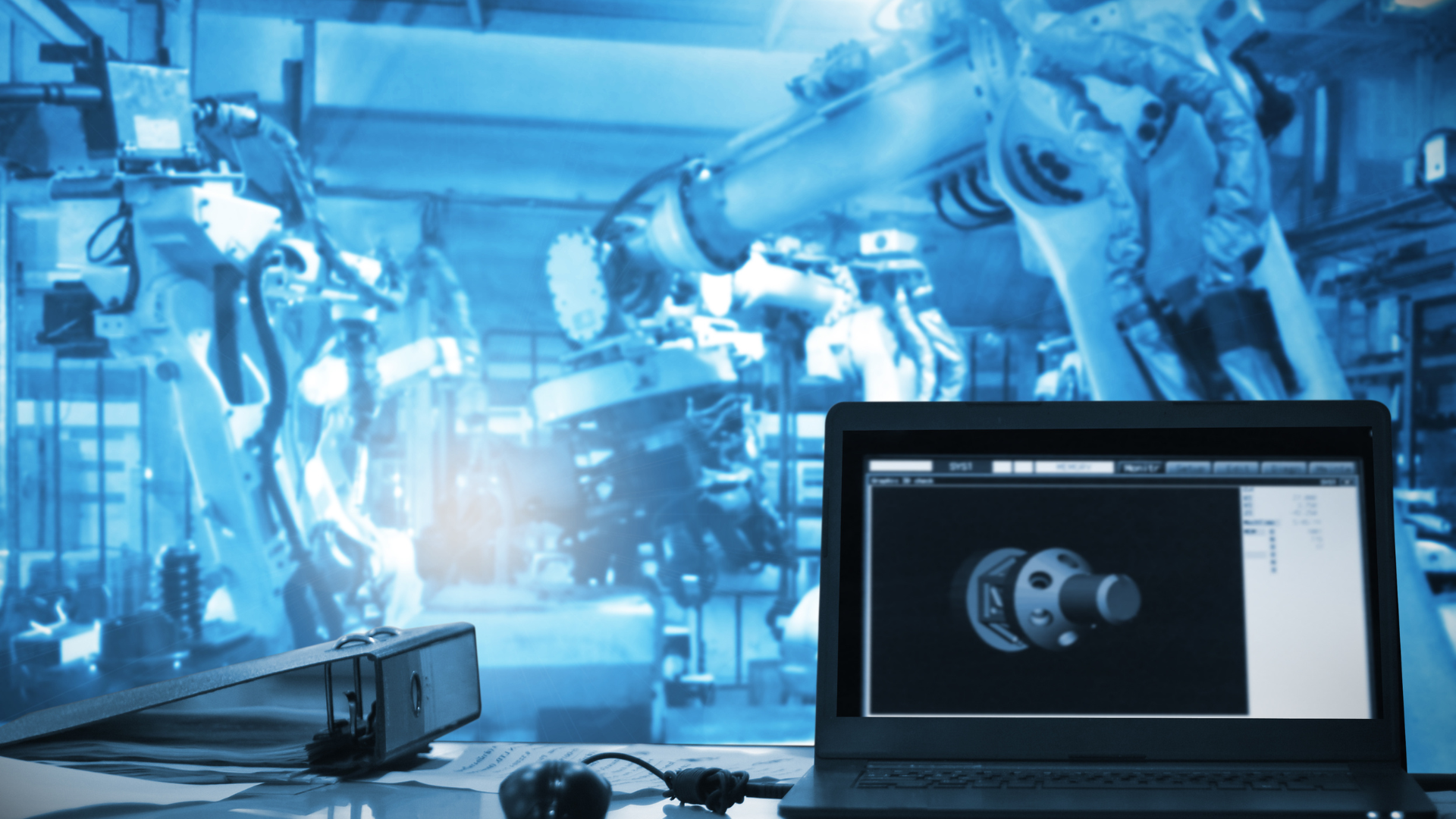