What Does OPC Stand For in Business?
What Does OPC Stand For in Business?
OPC, which stands for OLE for Process Control, is a widely used acronym in the business world. OLE, or Object Linking and Embedding, is a technology developed by Microsoft that allows different software applications to share and exchange data. In the context of business, OPC specifically refers to the implementation of OLE technology in process control systems.OPC has revolutionized the way businesses monitor and control their industrial processes. It enables seamless communication between various devices, sensors, and software applications involved in process control. This interoperability ensures that data can be easily exchanged and accessed by different components of a system, regardless of their manufacturer or platform. By adopting OPC standards, businesses can achieve improved efficiency in their operations. The real-time data exchange facilitated by OPC enhances decision-making processes by providing up-to-date information on process variables such as temperature, pressure, flow rate, and more. This valuable data can be used to optimize production processes, minimize downtime due to equipment failure or maintenance issues, and enhance overall productivity. Moreover, OPC offers a flexible solution that can be utilized across different industries including manufacturing plants, energy production facilities, chemical processing plants, and many others. Its versatility allows businesses to integrate diverse hardware devices and software applications seamlessly. In summary, OPC (OLE for Process Control) is an essential technology in today's business landscape as it empowers organizations with efficient communication capabilities within their process control systems. By leveraging OPC standards effectively, businesses can streamline operations, improve decision-making processes, and ultimately achieve higher levels of productivity across various industries. It is a set of standards and protocols that enable communication between various industrial automation devices and software applications.
OPC SCADA
OPC, which stands for OLE for Process Control, is a widely adopted technology in the field of SCADA (Supervisory Control and Data Acquisition) systems. These systems play a crucial role in industrial processes by providing real-time monitoring and control capabilities. OPC acts as a communication protocol that enables seamless data exchange between various devices and software applications within a SCADA system. By employing OPC, organizations can effectively collect and analyze data from diverse sources such as sensors, machines, and databases. This empowers operators to make informed decisions, optimize processes, improve efficiency, and ensure the smooth functioning of industrial operations. OPC provides a standardized way for different devices, such as sensors, controllers, and software applications, to exchange data in real-time.
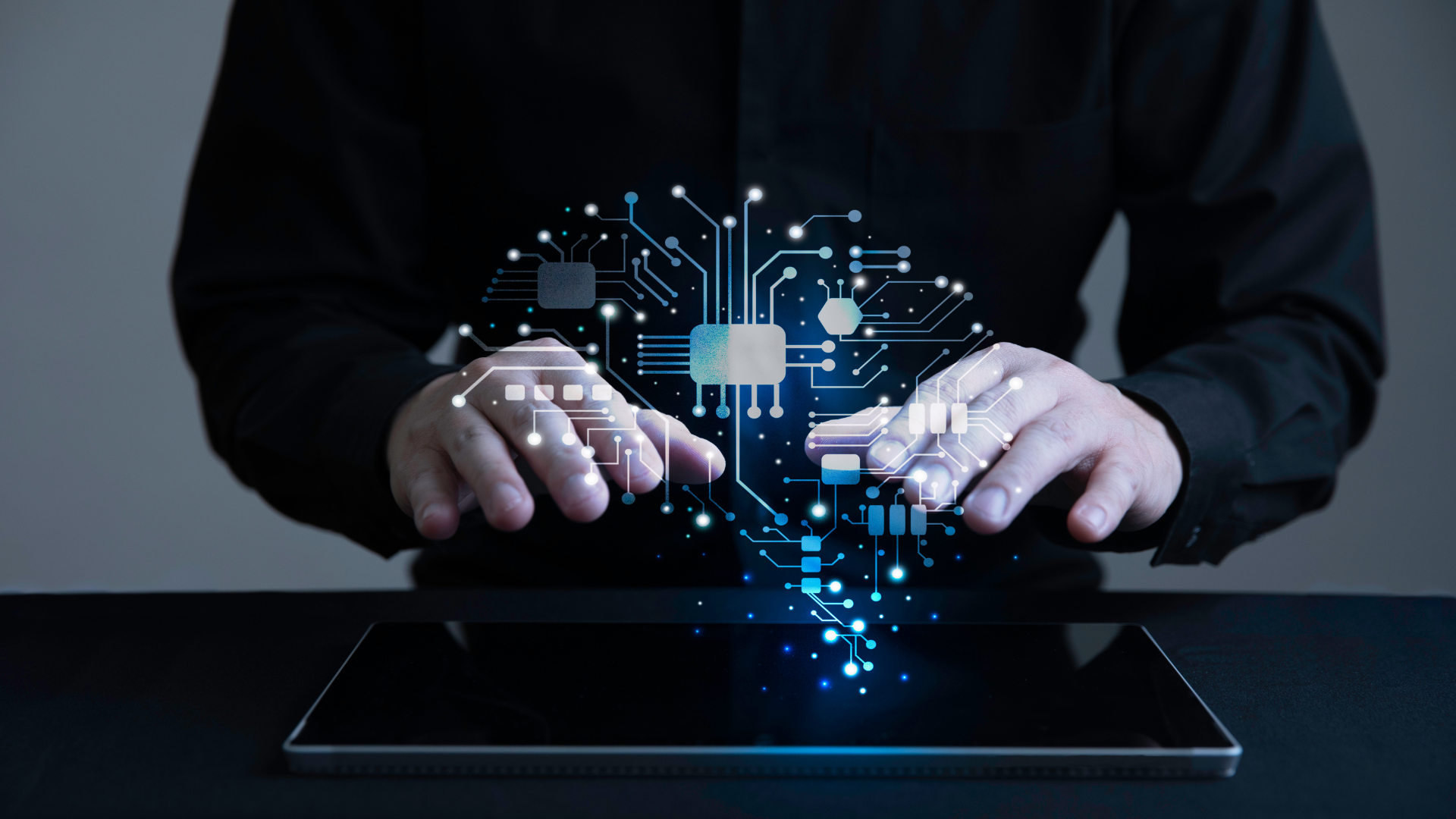
OPC Protocol Example
When it comes to OPC (OLE for Process Control) protocols, it's important to note that there are several versions available, each serving specific purposes. Two of the most commonly used versions are OPC DA (Data Access) and OPC UA (Unified Architecture). OPC DA primarily focuses on real-time data exchange between devices and applications. This version enables seamless communication and synchronization of data, allowing for efficient monitoring and control in industrial systems. It ensures that real-time data is accessible to applications in a reliable manner, facilitating rapid decision-making processes. On the other hand, OPC UA takes the concept of OPC protocols to a higher level by offering a unified architecture. This means that it provides not only real-time data access but also comprehensive support for information modeling, security mechanisms, and platform independence. OPC UA offers enhanced scalability and interoperability between different systems and devices within an industrial environment. Both versions have their own strengths and are widely adopted in various industries based on specific application requirements. It's important for businesses to evaluate their needs carefully before choosing between OPC DA or OPC UA to ensure optimal performance and compatibility with their existing infrastructure. On the other hand, OPC UA is a more advanced version that offers enhanced security features, platform independence, and support for complex data structures.
OPC Communication
To successfully integrate OPC communication into a system, it is essential to have an OPC server software in place. This specialized software plays a crucial role as an intermediary between devices or applications that require data exchange. By acting as a bridge, the OPC server software facilitates seamless and efficient communication between various components within the system. It enables devices and applications to effectively transmit and receive information, ensuring smooth data flow throughout the entire network. There are various vendors offering OPC server software solutions with different features and pricing models.
When it comes to OPC servers, there are numerous options available in the market. Among these options, the Matrikon OPC server stands out as a popular choice. It has gained recognition for its reliable performance and extensive features that cater to the diverse needs of various industries. With its user-friendly interface and robust functionality, the Matrikon OPC server provides seamless communication between different devices and applications within industrial automation systems. Its wide compatibility with different protocols further enhances its appeal, making it a go-to solution for many organizations seeking efficient data exchange in their operations. While there may be free versions or trial periods offered by some vendors for their OPC server software products, it's essential to check with the specific vendor or visit their website to determine if they offer a free version or trial period.
In summary, OPC, which stands for OLE for Process Control, is a widely-used acronym in the field of industrial automation and control systems. It refers to a set of standards and specifications that enable interoperability between various software applications and devices used in process control environments. The OLE (Object Linking and Embedding) technology allows different software applications to communicate and exchange data seamlessly, facilitating efficient process monitoring, data collection, and control. OPC has greatly improved the integration of disparate systems in industrial settings and has become an essential component in ensuring smooth operations and enhanced productivity. It provides a standardized way for industrial automation devices and software applications to communicate with each other. Different versions of the protocol exist like OPC DA and OPC UA. An OPC server software acts as an intermediary for facilitating this communication process. While there may be options for free or trial versions of certain products like Matrikon's OPC server software available in the market, it's important to verify with individual vendors regarding their pricing models.
OLE for Process Control
OLE for Process Control (OPC) is a standard protocol that enables seamless communication between various industrial automation systems. It provides a common interface for real-time data exchange between control devices such as PLCs, DCS, and SCADA systems and software applications. OPC enhances interoperability and data accessibility, allowing for more efficient and flexible process automation. This standard is crucial for optimizing industrial operations, improving system integration, and ensuring reliable data flow across different platforms.
Understanding OLE for Process Control: Basics and Benefits
OLE for Process Control (OPC) is a standard that enables different industrial automation systems to communicate with each other. It provides a common interface for real-time data exchange between control devices and software applications, enhancing interoperability. The main benefits of OPC include improved data accessibility, streamlined integration of diverse systems, and increased flexibility in process automation. Understanding OPC is crucial for optimizing industrial processes and achieving seamless communication between various control systems.
How OLE for Process Control Enhances Industrial Automation
OLE for Process Control (OPC) plays a pivotal role in enhancing industrial automation by facilitating reliable and efficient data exchange. OPC allows for seamless communication between disparate systems such as PLCs, SCADA, and DCS, ensuring that real-time data is accessible across the entire network. This interoperability improves system responsiveness, aids in better decision-making, and boosts overall operational efficiency. By leveraging OPC, industries can achieve greater automation and integration, leading to enhanced productivity and reduced downtime.
Implementing OLE for Process Control: Best Practices and Challenges
Implementing OLE for Process Control (OPC) in industrial environments involves several best practices and challenges. Best practices include thorough planning, ensuring compatibility of OPC servers and clients, and rigorous testing of the data communication interfaces. Common challenges include dealing with legacy systems, ensuring cybersecurity, and maintaining data integrity. Overcoming these challenges requires a strategic approach and a deep understanding of both OPC standards and the existing industrial setup, ensuring a smooth and effective implementation.
Future Trends in OLE for Process Control Technology
The future of OLE for Process Control (OPC) technology is set to be shaped by advancements such as OPC Unified Architecture (UA), which enhances security, scalability, and cross-platform interoperability. Emerging trends include the integration of OPC with IoT and edge computing, enabling more efficient data processing and real-time analytics. These advancements will further enhance the capabilities of OPC, driving smarter and more adaptive industrial automation systems. Staying abreast of these trends is essential for industries looking to leverage the latest in process control technology.