What Is HMI and How Does It Work?
What Is HMI and How Does It Work?
The Human Machine Interface (HMI) plays a crucial role in the field of industrial automation. HMI serves as the primary point of interaction between humans and machines, enabling seamless communication and control over complex industrial processes. With its user-friendly design and intuitive interface, HMI empowers operators to monitor real-time data, analyze system performance, and make informed decisions in a fast-paced industrial environment. By providing a bridge between humans and machines, HMI enhances operational efficiency, improves productivity, and ensures safer working conditions in various industries such as manufacturing, oil and gas, automotive, and more. In the context of industrial automation, an interface that serves as a crucial link between humans and machines is known as a Human-Machine Interface (HMI). This powerful tool empowers operators to effectively monitor and control numerous processes within a system. By providing a user-friendly graphical representation, HMIs facilitate seamless interaction between humans and machines, enabling operators to have real-time visibility into the functioning of the system. With its intuitive design and functionality, an HMI enhances operational efficiency by presenting vital information in a clear and organized manner. Operators can easily access critical data, such as process parameters, alarms, and status indicators, allowing them to make informed decisions swiftly. Moreover, HMIs often offer advanced features like touch-screen capabilities or multi-language support to further streamline communication between humans and machines. Overall, HMIs play a pivotal role in optimizing productivity by bridging the gap between operators and automated systems while ensuring reliable monitoring and control of various processes.
SCADA System
In the realm of SCADA (Supervisory Control and Data Acquisition) systems, the Human-Machine Interface (HMI) plays an essential and indispensable role. The HMI acts as a crucial component in enabling real-time data visualization, process monitoring, and control capabilities. Through its user-friendly interface, operators can effortlessly access critical information about the system's performance and status, facilitating effective decision-making. Moreover, the HMI empowers users to interact with the SCADA system by providing intuitive controls for executing commands or adjustments in real-time. This interactive aspect enhances operational efficiency while ensuring a swift response to any anomalies or contingencies that may arise within the system. Supervisory Control and Data Acquisition (SCADA) systems play a crucial role in various industries including manufacturing, energy, water treatment, and transportation. These systems are specifically designed to efficiently monitor and control complex processes within these sectors. By utilizing advanced sensors and communication networks, SCADA systems enable real-time data collection, analysis, and visualization. This enables operators to effectively monitor the operations of industrial machinery, detect abnormalities or faults in the process, and make informed decisions for optimal performance. Moreover, SCADA systems provide an integrated platform for supervisory control, allowing operators to remotely manage multiple processes from a central location. The implementation of SCADA technology has revolutionized these industries by enhancing efficiency, reducing operational costs, improving safety protocols, and ensuring regulatory compliance
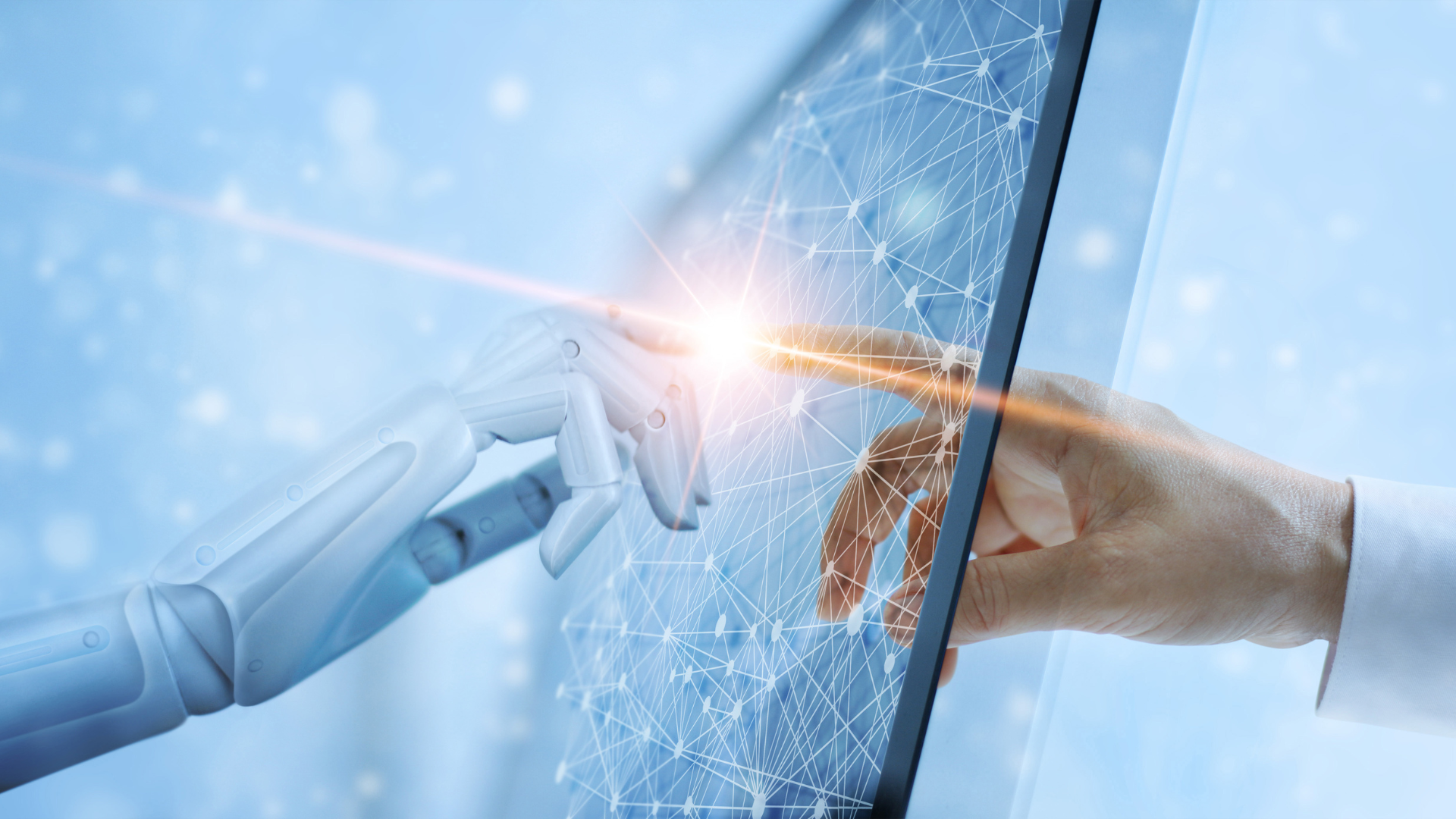
What are the three 3 main types of SCADA?
When it comes to SCADA systems, there are three main types that are commonly used in various industries. These types include supervisory-only systems, distributed systems, and integrated systems. Let's take a closer look at each one. Supervisory-only systems are designed to provide a high-level overview and control of industrial processes. They allow operators to monitor and manage multiple remote terminal units (RTUs) or programmable logic controllers (PLCs) from a central location. This type of system is ideal for applications where real-time monitoring and basic control functions are sufficient. Distributed systems, on the other hand, involve multiple SCADA servers that work together to oversee various aspects of the industrial process. This allows for greater scalability and redundancy, as well as improved performance. Distributed SCADA systems are often used in large-scale operations where there is a need for continuous monitoring and control across multiple sites or areas. Lastly, integrated systems combine the functionalities of both supervisory-only and distributed systems. They offer comprehensive monitoring, control, and data acquisition capabilities while also providing the flexibility to scale up or down based on specific requirements. Integrated SCADA systems are widely used in industries such as oil and gas, power generation, water treatment plants, and manufacturing facilities. In summary, understanding the different types of SCADA systems can help industries make informed decisions when implementing these technologies into their operations. Whether it's supervisory-only systems for basic control needs or integrated solutions for complex processes, choosing the right SCADA system can greatly enhance efficiency and productivity in the workplace.
Supervisory-only systems, as their name suggests, primarily focus on the acquisition and monitoring of data rather than having direct control capabilities. These systems are designed to gather and analyze data from various sources, such as sensors or other connected devices, in order to provide valuable insights and information. While they do not possess the ability to directly control or manipulate the processes being monitored, they play a crucial role in providing real-time updates and alerts that enable human operators to make informed decisions and take appropriate actions based on the acquired data. By leveraging advanced technologies like machine learning and analytics, supervisory-only systems contribute significantly to enhancing operational efficiency, optimizing resource allocation, and improving overall productivity within various industries. Distributed systems, in the context of computer science and networking, are complex networks that consist of multiple remote terminal units (RTUs) that communicate with a central supervisory unit. These systems are designed to handle large-scale data processing and enable efficient communication between different components across geographically dispersed locations. The RTUs, which serve as autonomous nodes within the network, collect and transmit data to the central supervisory unit. This allows for real-time monitoring, control, and coordination of various operations within the system. The distributed nature of these systems ensures enhanced reliability, scalability, and fault tolerance by distributing the workload across multiple nodes and enabling seamless communication between them. Additionally, this architecture enables better resource utilization and facilitates easy integration with other systems or devices. Overall, distributed systems play a crucial role in numerous industries such as telecommunications, power distribution, transportation management, industrial automation, and more by providing efficient and robust communication infrastructure. Integrated systems are highly sophisticated and innovative solutions that bring together the best of both worlds: supervisory functions and direct control capabilities. These systems seamlessly merge various components, allowing for efficient coordination and automation across different processes. By integrating supervisory functions, such as monitoring, analyzing, and decision-making, with direct control capabilities, businesses can achieve a higher level of efficiency, accuracy, and responsiveness in their operations. This integration empowers organizations to streamline their workflows and optimize resource allocation while minimizing human error. The result is a more effective and reliable system that enhances productivity, reduces costs, and ultimately improves overall performance.
Difference between HMI and PLC
It is crucial to understand and highlight that Human-Machine Interface (HMI) and Programmable Logic Controller (PLC) are distinct entities in the field of automation and control systems. While they both play vital roles in industrial settings, they serve different functions and have separate functionalities.HMI refers to the user interface or graphical display through which operators can interact with machines or systems. It enables users to monitor, control, and manage various aspects of the machinery or processes. HMI interfaces usually consist of touchscreens, buttons, indicators, and other visual elements that provide real-time data visualization and facilitate user input. On the other hand, PLCs are specialized computers designed for automating industrial processes. They are responsible for executing control algorithms based on input signals from sensors or other devices. PLCs are typically programmed using ladder logic or other programming languages specifically tailored for automation purposes. While HMI serves as the interface between humans and machines, allowing operators to visualize data and make adjustments as needed, PLCs act as the brains behind the automation process by controlling machinery operations based on predefined logic. Understanding this distinction is important to ensure efficient utilization of both HMI and PLC technologies in industrial applications while avoiding confusion between their respective functionalities. Programmable Logic Controllers (PLCs) play a crucial role in industrial systems as they are responsible for the control and automation of various physical processes. They act as the brains of the operation, ensuring that everything runs smoothly and efficiently. On the other hand, Human-Machine Interfaces (HMIs) serve as the bridge between operators and the system itself by providing a visually intuitive Graphical User Interface (GUI). This allows operators to interact with the system, monitor its performance, make necessary adjustments, and receive real-time feedback. By combining PLCs and HMIs in an industrial setup, businesses can achieve seamless control, enhanced productivity, and improved overall system performance.
There are various types of HMIs available in the market today. These include touchscreens, keypads, graphical displays, and even mobile applications that allow remote monitoring and control. Each type offers different features and functionalities to suit specific industry requirements.
The three main components of a typical SCADA system are:
1. Supervisory Unit: This is the central unit responsible for collecting data from remote devices or sensors connected to the system.
2. Remote Terminal Units (RTUs): These units gather data from field devices such as sensors or actuators and send it back to the supervisory unit.
3. Communication Infrastructure: This includes networks or protocols that facilitate communication between the supervisory unit and RTUs. PLC HMI programming involves creating logic programs within PLCs that interact with HMIs. This programming enables the HMI to display real-time data, control processes, and provide operators with a user-friendly interface for system management.
In conclusion, HMI is an essential component of SCADA systems, providing operators with a visual interface to monitor and control industrial processes. Understanding the differences between HMI and PLC, as well as the various types of HMIs available, is crucial for those working in automation and control industries.