What is the role of MES?
What is the Role of MES?
The role of a Manufacturing Execution System (MES) is to monitor, control, and optimize production processes on the shop floor in real-time. MES helps bridge the gap between enterprise-level systems like ERP and the actual production equipment, ensuring efficient operations, data collection, and quality management. By providing detailed insights into production, MES allows for better decision-making, minimizing downtime and improving overall productivity. Integrating the Best SCADA Software with MES enhances control over both production and process data, creating a more cohesive and efficient manufacturing environment.
List of MES Software
Several companies provide leading MES software solutions to streamline production processes and improve manufacturing efficiency. Popular MES software includes Siemens SIMATIC IT, known for its comprehensive automation and integration features, and Rockwell Automation's FactoryTalk, which offers real-time visibility and control over production. SAP Manufacturing Execution provides robust tools for managing production workflows and ensuring compliance with industry standards. Other notable MES solutions are GE Digital's Proficy MES and Dassault Systèmes' DELMIA, both of which excel in delivering real-time data insights and process optimization.
MES System Examples
Examples of MES systems range from Siemens Opcenter, which specializes in optimizing manufacturing performance, to Honeywell Forge, a cloud-based solution offering enhanced productivity and predictive insights. Rockwell Automation’s FactoryTalk ProductionCentre integrates production and quality control, ensuring smoother operations. GE Digital’s Proficy MES focuses on improving efficiency and product quality, while SAP Manufacturing Execution provides end-to-end visibility across production, from planning to delivery. These systems help manufacturers maintain quality, optimize processes, and reduce downtime.
What is the Main Purpose of MES
The main purpose of a Manufacturing Execution System (MES) is to provide real-time control, monitoring, and optimization of production processes. MES ensures that manufacturing operations are efficient, consistent, and aligned with business goals by tracking production data, managing workflows, and ensuring quality standards are met. It acts as a bridge between the shop floor and enterprise systems like ERP, helping to reduce downtime, minimize waste, and improve overall productivity. By offering detailed insights and control, MES helps manufacturers make informed decisions and respond quickly to changes in demand or production challenges.
Manufacturing Execution System PDF
For a Manufacturing Execution System PDF, businesses often provide downloadable resources detailing the features, benefits, and technical specifications of MES solutions. These PDFs typically cover how MES supports various industries, key functionalities like production tracking, and integration with other systems. They are valuable for understanding the system’s impact on improving manufacturing performance and can serve as reference materials for implementing MES in an organization.
Manufacturing Execution System
A Manufacturing Execution System (MES) is a software solution designed to monitor and control the production process in real-time, from raw material usage to finished goods. MES integrates with other enterprise systems like ERP and SCADA, providing visibility into production data, optimizing processes, and ensuring product quality. It helps manufacturers improve efficiency, reduce downtime, and meet compliance standards by offering real-time data insights and automated workflows. MES is crucial for bridging the gap between business-level planning systems and the factory floor operations.
What Are the Principles of MES
The key principles of a Manufacturing Execution System (MES) focus on optimizing production processes, improving efficiency, and maintaining product quality. One core principle is real-time data management, where MES tracks and collects information from the shop floor to provide actionable insights. Another principle is process control and automation, ensuring that production follows predefined workflows and meets quality standards. MES also promotes integration and communication between different systems, enabling seamless coordination between production, supply chain, and business operations to drive overall manufacturing performance.
MES Manufacturing
MES (Manufacturing Execution System) plays a vital role in optimizing manufacturing processes by providing real-time data and control over production operations. It helps manufacturers track every aspect of the production cycle, from material input to finished products, ensuring that quality and efficiency standards are met. By integrating MES with automation and other enterprise systems, manufacturers can improve productivity, reduce waste, and respond more quickly to market demands. MES systems are essential for achieving seamless communication between the shop floor and higher-level business systems.
What Are the Core Functions of an MES
The core functions of a Manufacturing Execution System (MES) include real-time monitoring of production processes, enabling manufacturers to track performance and ensure efficiency on the shop floor. MES handles production scheduling by coordinating workflows, resources, and materials to optimize output. It also provides quality management, ensuring that products meet predefined standards by monitoring production conditions and performing quality checks. Additionally, MES integrates with other systems like ERP and SCADA to manage data flow across the entire production lifecycle, helping manufacturers improve decision-making and productivity.
MES Software Examples
Popular MES software examples include Siemens Opcenter, which focuses on enhancing manufacturing efficiency through advanced production planning and scheduling tools. Rockwell Automation's FactoryTalk ProductionCentre is another example, offering real-time visibility and control over production processes, ensuring quality and compliance. SAP Manufacturing Execution integrates seamlessly with ERP systems, providing end-to-end control over manufacturing operations. Additionally, GE Digital's Proficy MES helps optimize production by offering detailed insights into equipment performance, quality control, and resource management. These solutions are widely used to streamline and improve manufacturing workflows.
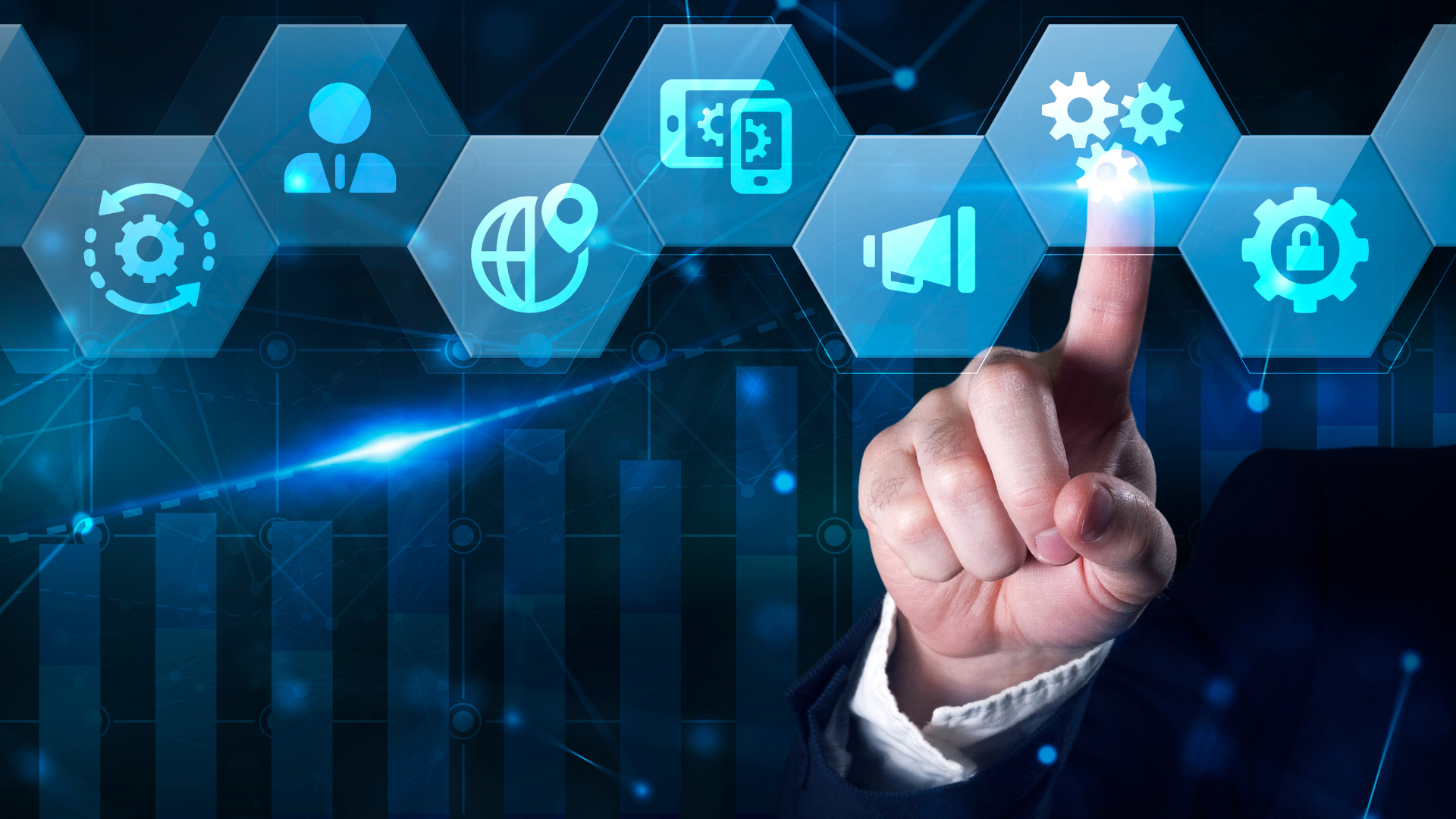
What is the Difference Between MES and SAP
The difference between MES and SAP lies in their focus and functionality. An MES (Manufacturing Execution System) primarily manages and monitors production processes in real-time on the shop floor, controlling everything from material usage to product quality. SAP, on the other hand, is an enterprise resource planning (ERP) system that covers broader business processes like finance, supply chain, and human resources. While MES focuses on optimizing manufacturing, SAP provides a holistic view of the entire organization, including manufacturing as one of many modules.
SAP MES
SAP MES refers to SAP’s solution for managing manufacturing operations within its ERP system. It integrates the production process with other business functions, offering tools for real-time production monitoring, resource management, and quality control. SAP MES helps manufacturers optimize their shop floor operations while ensuring seamless data flow between production and other enterprise systems like supply chain and finance. It’s designed to improve efficiency, reduce downtime, and maintain product quality through advanced automation and integration.
MES vs ERP
When comparing MES vs. ERP, MES focuses specifically on real-time control and optimization of the manufacturing process, while ERP (Enterprise Resource Planning) covers a broader scope of business operations, including finance, procurement, and human resources. MES ensures that production is efficient and meets quality standards on the shop floor, while ERP manages overall business strategy and resource allocation. Many companies use both systems in tandem, with MES managing production data and ERP handling high-level business functions.
What Does an MES Engineer Do
An MES Engineer is responsible for designing, implementing, and maintaining Manufacturing Execution Systems (MES) that monitor and control production processes on the shop floor. They ensure that the MES integrates seamlessly with other enterprise systems like ERP and SCADA to optimize production, manage data, and maintain product quality. MES Engineers troubleshoot issues, customize software solutions, and train staff to use the system effectively, playing a crucial role in improving manufacturing efficiency and reducing downtime.
What is a MES Engineer
An MES Engineer is a specialized professional who works on configuring and supporting MES software solutions for manufacturing environments. They focus on integrating the system with machines, equipment, and other software, ensuring smooth operations on the production floor. Their role involves developing automation scripts, analyzing production data, and collaborating with various departments to enhance production workflows. MES Engineers help manufacturers increase efficiency, track production, and maintain high-quality standards.
MES Software
MES Software is designed to manage and control production processes in real-time within manufacturing environments. It helps manufacturers track raw materials, monitor machine performance, and ensure product quality throughout the production lifecycle. Key features of MES software include production scheduling, quality management, and data collection, all of which help optimize manufacturing workflows. Popular MES solutions include Siemens Opcenter, Rockwell Automation's FactoryTalk, and SAP Manufacturing Execution, which provide comprehensive tools to enhance production efficiency and performance.
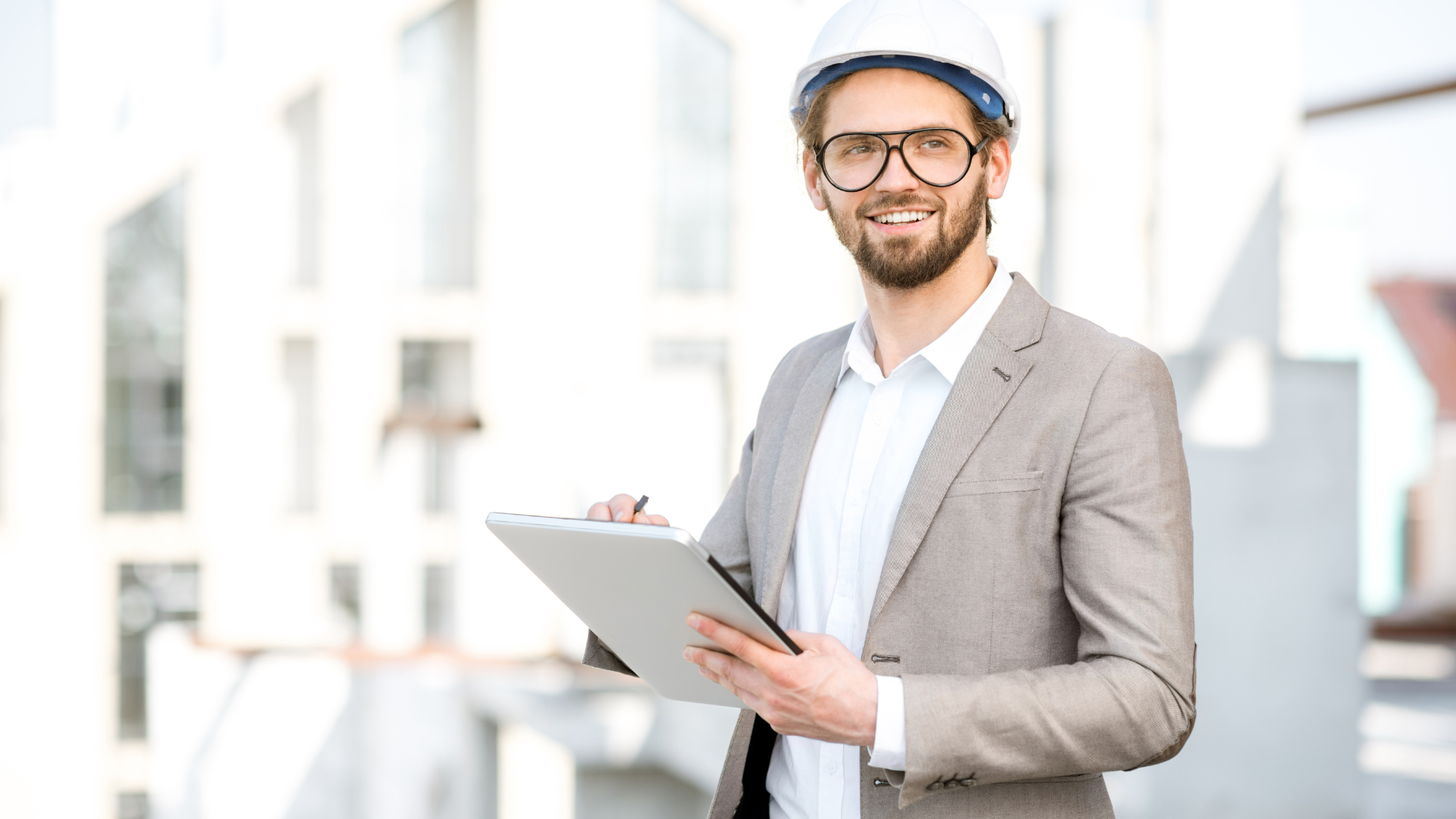