A Comprehensive Guide to Data Historians and How They are Revolutionizing Data Analysis
What is a Data Historian and How Does it Work?
A data historian in Industrial Automation is a specialized type of software system designed for the purpose of storing and organizing vast volumes of historical data. It provides an effective way to capture, analyze, and visualize complex datasets over extended periods of time in order to gain valuable insights and knowledge from the collected information. Industrial Data Stores (IDS) are specialized data storage solutions that are used to store and analyze data from industrial systems such as Supervisory Control and Data Acquisition (SCADA), Programmable Logic Controllers (PLCs), and other industrial automation systems. This advanced technology helps organizations to increase production efficiency by providing them with real-time information, allowing them to make better decisions and reduce risks associated with process control. Data historians are invaluable tools used to accurately track and monitor changes in the system in near real-time, enabling more informed decision-making and improved operational efficiency. They provide an extensive audit history of data, making it easier to detect anomalies, identify opportunities for improvement, as well as provide a deeper understanding of how the system behaves over time.
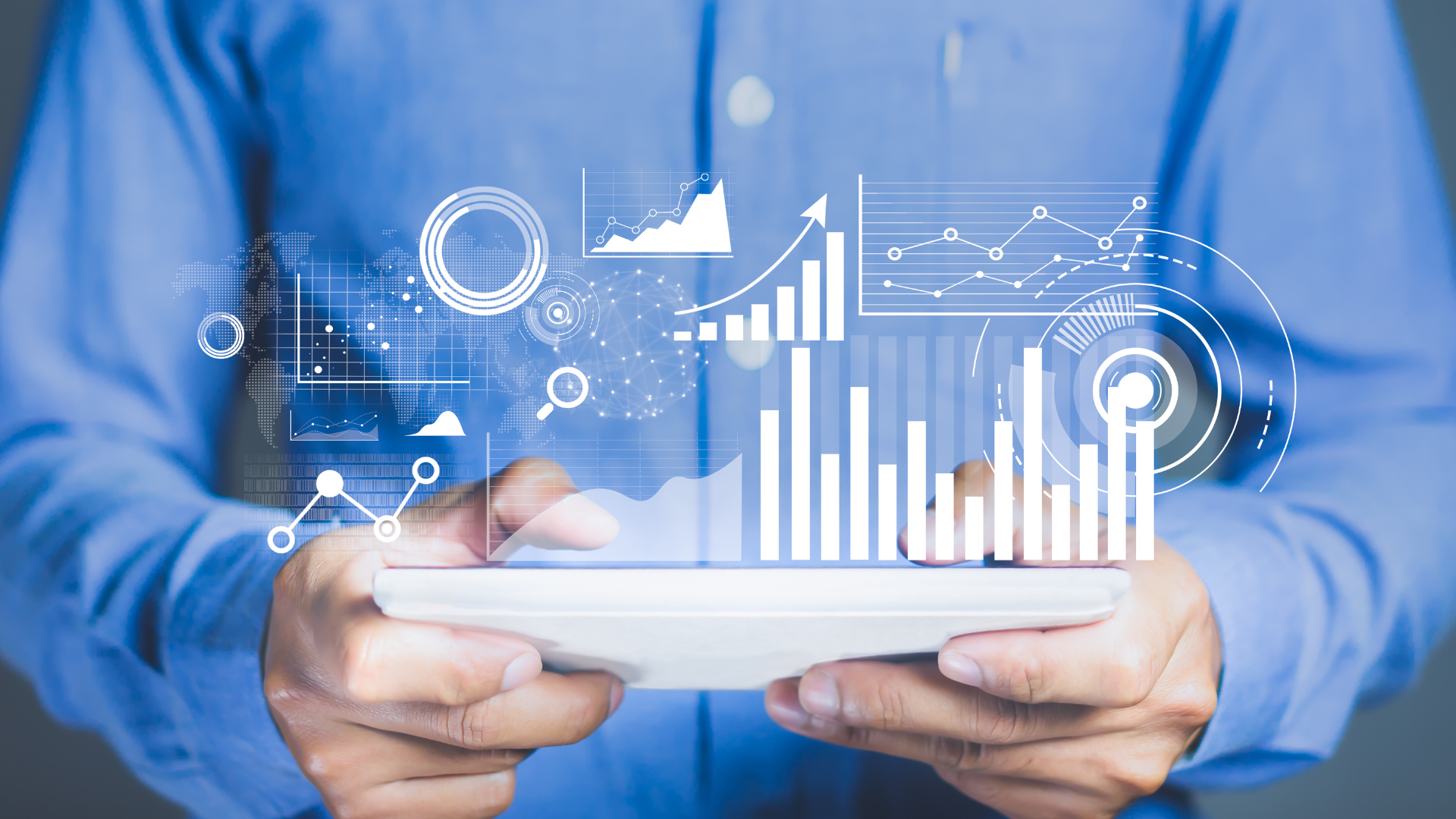
Data historians are software applications that are designed to store and manage historical data and can be divided into two main types: top-level data historians, which are capable of storing large amounts of historical data from multiple sources, and lower-level data historians, which are more specialized in their purpose and can store smaller amounts of historical data from a single source. These applications provide a useful tool for businesses to track the progress of their operations over time. The type of historian that you select to work with should be determined based on your individual project requirements and desired outcomes. Different types of historians specialize in different areas, such as military history, religious history, or even a more general overview of a certain period or region. By carefully assessing your needs and finding the right specialist for the job, you can ensure that you have access to the best possible historical knowledge and information.
In addition to securely storing historical data, some data historians can also provide advanced features such as real-time streaming of data, powerful analytics capabilities for more in-depth analysis, comprehensive reporting tools for better visibility into your data trends, and more. Understanding how these features work and how they can be leveraged can help you make the most out of your historian system and optimize its performance.
The Benefits of Using a Data Historian for Your Business
A data historian is a software tool that helps businesses store, analyze, and visualize their data. It is used to track changes in the data over time and can be used to identify trends or patterns in the data. Data historians are becoming increasingly popular as businesses look for ways to better understand their customers and make more informed decisions.
Data historians come in many different forms, from cloud-based solutions to on-premise solutions. The best data historian software will depend on your business needs and budget. It should be able to store large amounts of data securely, provide easy access to the stored information, and offer powerful analytics capabilities. Additionally, it should be able to integrate with other systems such as ERP or CRM systems for a comprehensive view of your business operations.
How to Choose the Right Data Historian for Your Needs
Choosing the right data historian for your needs is essential for any business. A data historian is a software system that stores and organizes large amounts of data from various sources, such as PLCs, SCADA systems, and other industrial automation systems. It can be used to analyze trends in production processes, identify problems in the system, and provide insights into how to improve efficiency.
When selecting a data historian, it is important to consider factors such as scalability, cost-effectiveness, ease of use, security features, and compatibility with existing systems. Additionally, you should also consider whether the data historian supports real-time analysis or batch processing of historical data. Furthermore, you should also look into the features offered by different vendors to ensure that they meet your specific requirements.
Conclusion: Unlock the Power of Data Historians to Transform Your Business Performance
Data Historians are powerful tools that can help businesses to transform their performance. They are used in manufacturing, control systems, and networks to store and analyze data. By leveraging the power of data historians, businesses can gain insights into their operations and make informed decisions that will improve their performance. Data Historians also enable empowered automation, which allows businesses to automate processes and tasks with greater accuracy and efficiency. With the help of data historians, businesses can unlock the power of data to transform their business performance.
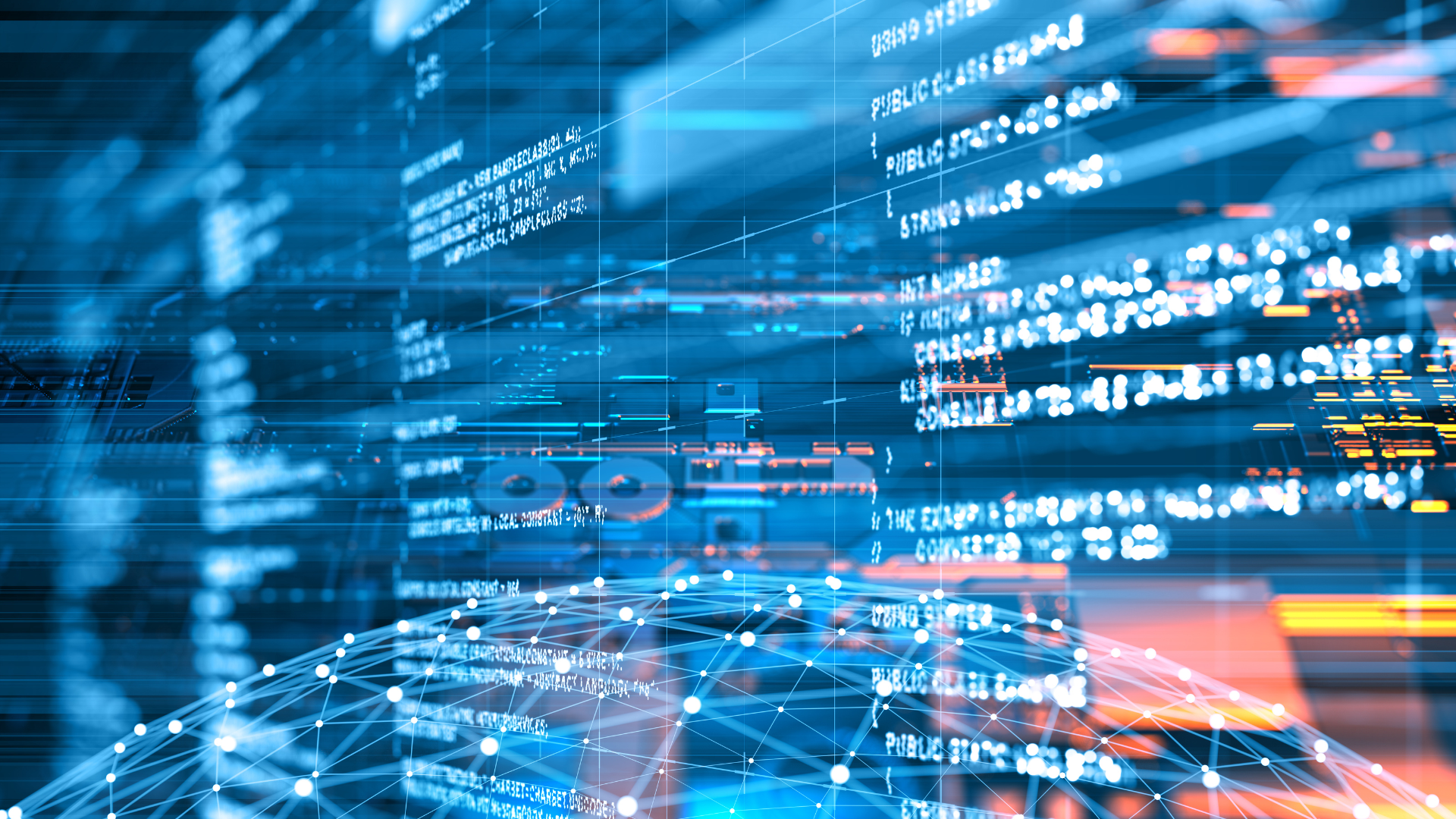