Data Historian vs Database: Which One is More Suitable for Your Business?
What are Data Historians and Databases and How Do They Differ?
Sensors are now ubiquitous and play a key role in factory settings. They monitor the number of parts used, as well as assess the quality of products. Even so, once measurements have been taken, more challenges may arise. Utilizing data for improvement requires strategically considering where to gather it and how to use it to reduce variability and maximize quality.
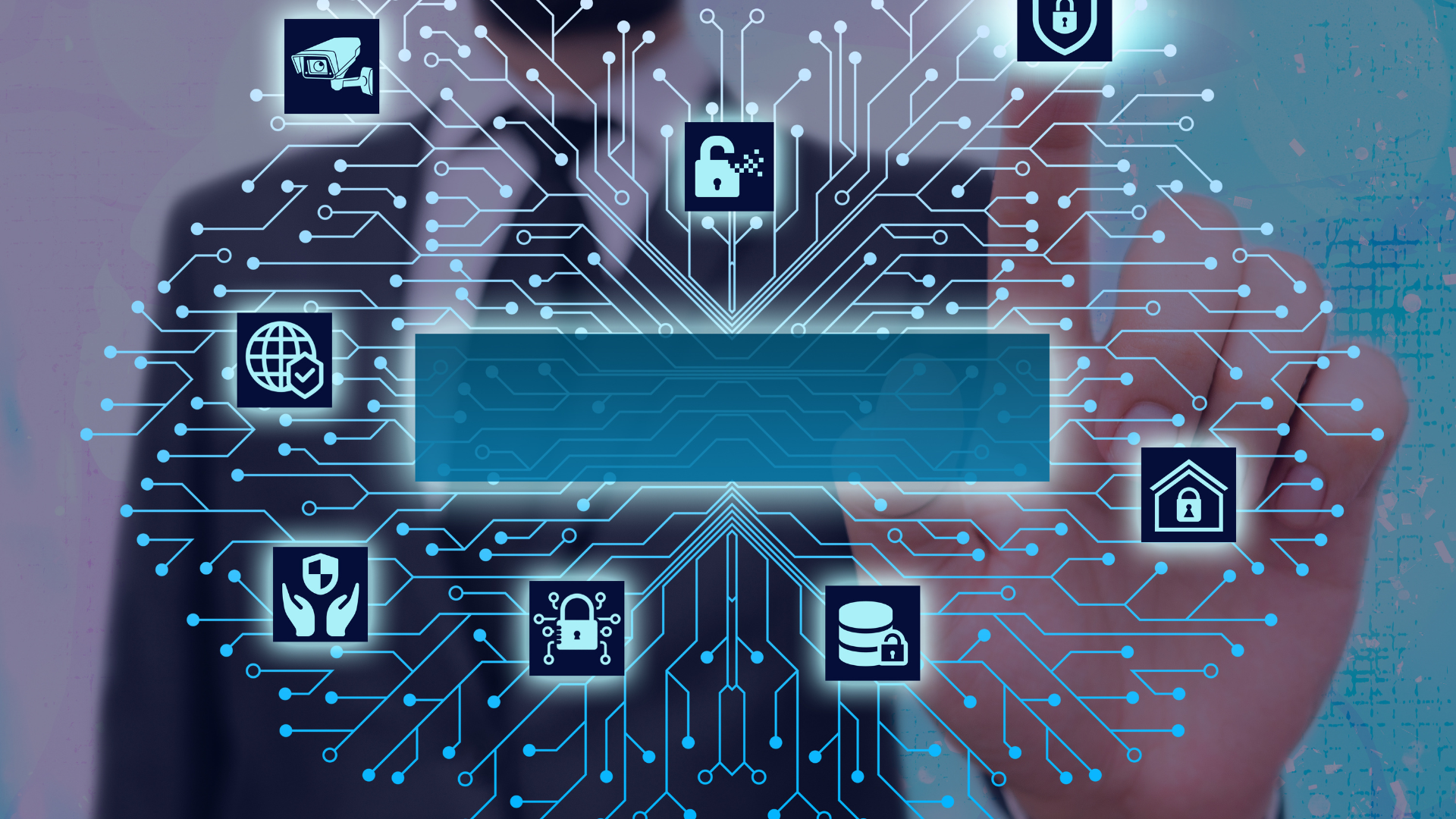
Possibilities: Manufacturing firms need to collect data in real-time for optimal analysis. There are two primary methods to do this: via a traditional relational Historian SQL database or via a dedicated plant Manufacturing Data Historian.
When it comes to data storage and management, businesses have to choose between a data historian in industrial automation and a database. Data historian systems are designed to store large amounts of time-series data, while databases are used for storing structured data. Each has its own advantages and disadvantages, so it is important to determine which one is more suitable for your business.
In this article, we will discuss the differences between a data historian and a database system. We will also look at the features of popular data historian vendors, their architecture and what they can do for businesses. By the end of this article, you should be able to decide which system is best suited for your needs.
Each offers distinct advantages. A relational database is built to manage relationships, but a plant data historian software is optimized for time-series data. For example, relational databases are great at answering a question such as: "Which customer ordered the largest shipment?" A Data Historian SCADA, however, excels at answering questions such as: "What was today's hourly unit production standard deviation?"
Relational Databases: Relational databases are the perfect choice for storing in-depth manufacturing info or historical data. Their flexible architecture facilitates integration with other business systems and makes them a great option. Companies are making use of the open-source data historian nature of relational databases for manufacturing applications by creating and managing custom tables that store data from different sources such as other databases, manual inputs on forms, and XML files. This helps to extend existing functionality.
Relational databases have been growing in popularity, especially when it comes to handling transactional and manufacturing applications. This includes capturing data from RFID readers or contextual information/time-series data from a few sensors. In these scenarios, a relational database typically offers the best performance.
Plant Data Historians: Plant data historians are an ideal option when collecting data from sensors and other real-time systems. It uses manufacturing standards like OPC which encourages seamless communication across various platforms. Plant data historians provide the convenience of using standard interfaces, making their implementation easier and more efficient.
Plant data historians can be installed and configured quickly with no need for custom coding or scripting, eliminating the need for manual management or creation of data schema, triggers, stored procedures, or views.
Plant data historians are specifically designed to endure the difficult environment of manufacturing floors and can still log & store data even when the main database is inaccessible. Plant data historians typically come with a feature that enables you to compress the stored data, helping reduce the required disk space. If you have a large number of sensors (more than 1000) that are generating time-series data quickly (at less than 5s refresh rate), using a plant data historian can be beneficial.
The Best of Both Worlds: Relational databases and plant data historians are powerful tools that enable companies to dig deeper into their data from their plants, maximize performance, bridge the gap between plant floor & business systems, and reduce costs incurred due to regulations. Quality experts widely agree that "measurement is essential to improvement" - as such, plantwide data collection is a critical part of this process.
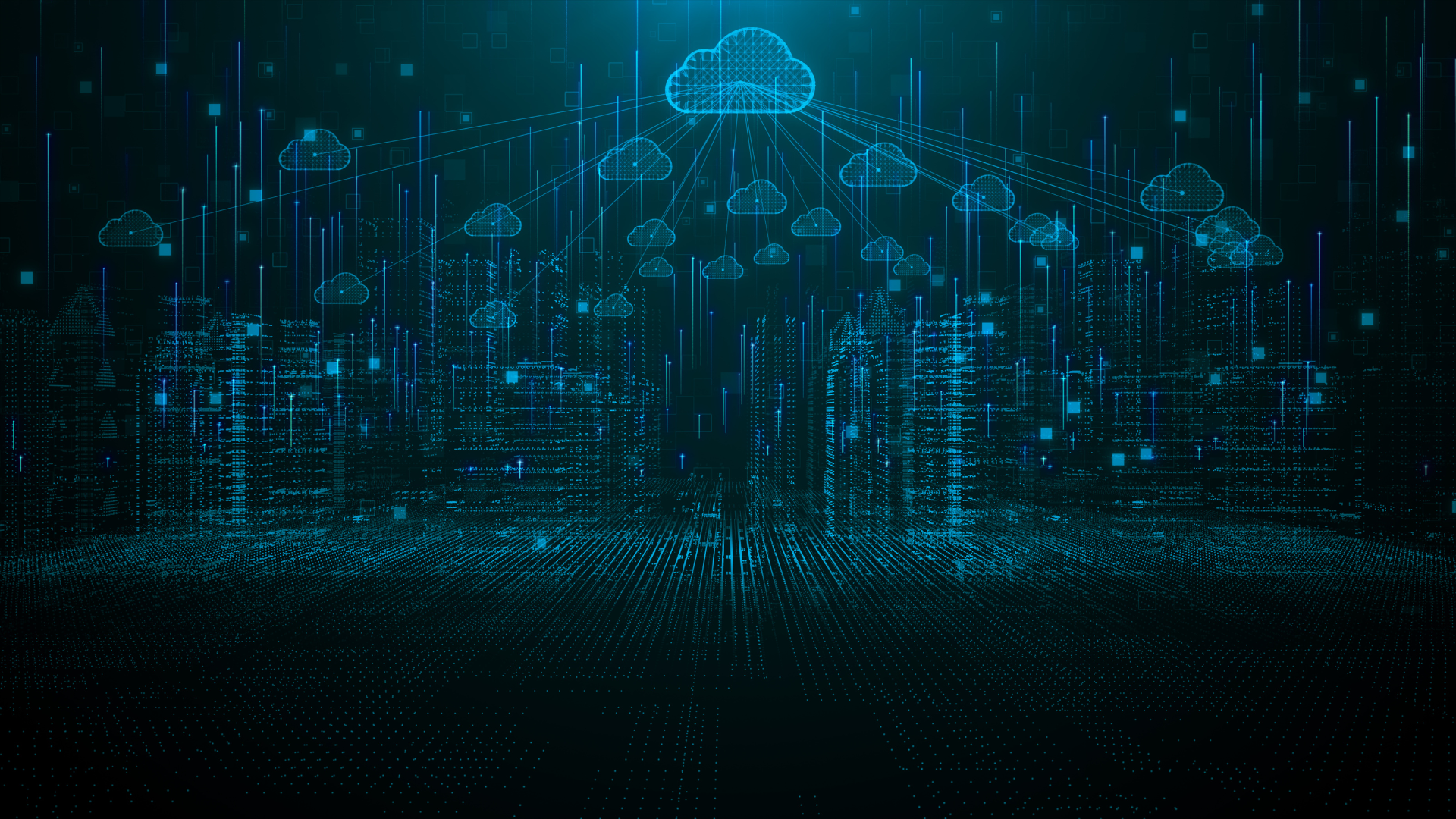
Utilizing analysis tools like Microsoft Excel or other available reporting solutions can improve the quality & consistency of your products. It also enables you to compare past production runs, review data prior to a downtime episode and compare ideal production runs with current ones. It's now simple to collect data, compile reports and share insights with today's advanced analysis tools; all accessible through your web browser.
In-process data collection is an essential link between plant operations & business activities, furnishing the business systems with the required data to get a clear & precise understanding of current production levels or past trends.
Using a relational database and a plant data historian is the best course of action, as it can yield numerous benefits for both the internal and external stakeholders. It provides comprehensive information that makes this decision a no-brainer.