Understanding Automatic Manufacturing: A Comprehensive Guide
Understanding Automatic Manufacturing: A Comprehensive Guide
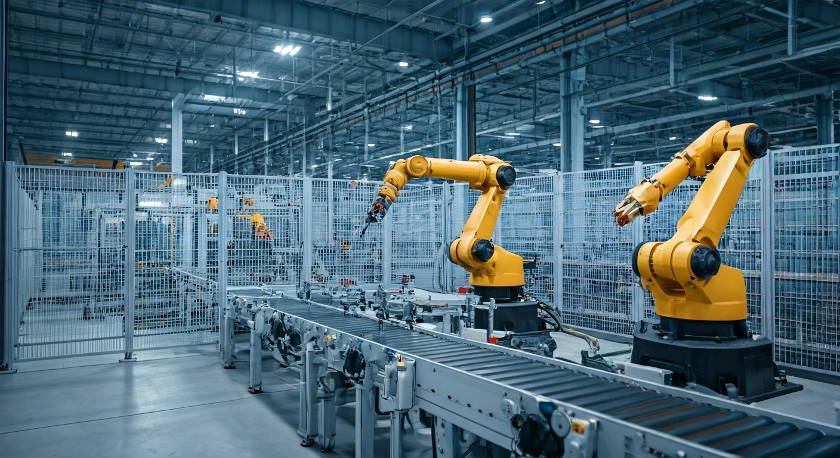
Key Highlights
- Automatic manufacturing leverages control systems, industrial robots, and data analytics to optimise production efficiency and reduce labor costs.
- Key components include various types of automation, such as fixed, programmable, and flexible systems, tailored to meet diverse manufacturing processes.
- Integration of IoT and advanced robotics enhances assembly lines and production goals by ensuring consistent quality and precision.
- Automation minimises human intervention while addressing safety concerns and improving quality control.
- Future trends like
machine learning and
predictive maintenance drive innovation and cater to evolving
market demands.
Introduction
The digital transformation of industries has started a new era in industrial automation. It has changed the way the manufacturing process works in big ways. By using advanced technology like control systems and automated machinery, companies can get more efficiency, better precision, and greater consistency. The change does not just automate work. It also shapes how people and machines work together so they can meet market demands as they grow or shift. As automation keeps moving forward, the link between new ideas and how they are used is what helps create the future of production.
Automatic Manufacturing Limited: Innovations That Matter
Key Components of Automatic Manufacturing
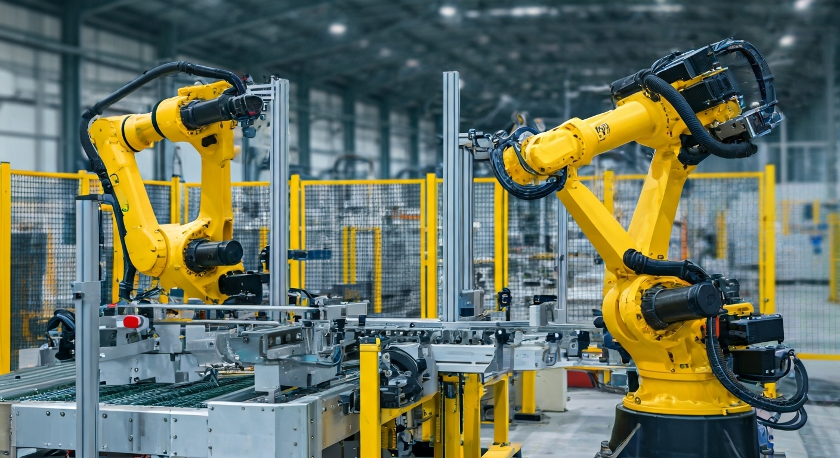
The base of automatic manufacturing is in how it helps make production better. It does this by cutting down on manual work and making tasks the same each time. The main tools are programmable logic controllers, industrial robots, and smart automation solutions. These work as a team to take care of boring tasks and make things run smoother. This helps set new levels for what the industry can do.
There is also the need to adapt. Flexible automation can change fast to handle market changes or new products. On the other hand, fixed automation is good for doing the same job over and over. With both types, manufacturers can keep up with others and stay strong in the global marketplace.
Overview of Automation Equipment
Automation equipment helps make sure things run well in production. Control systems sit at the center and use special plans to watch and change input and output. They help make choices quickly, which cuts down the time things are stopped and helps production be right and on time.
Programmable logic controllers (PLCs) are important in industrial automation. These strong computers help control systems by doing jobs to arrange steps, set timing, and handle logic. PLCs are built to work, even when the factory floor is tough. This makes them something a plant really needs.
Industrial robots show what modern automation looks like. These machines can be robotic arms putting together small parts or handle material handling systems. They are good at many types of jobs. Robots can keep a consistent quality and work without getting tired, which lets them change how we think of what efficiency is in manufacturing plants.
Role of Software in Manufacturing Automation
Software works as the main hub in industrial automation. It helps with things like data handling, running the system, and making things work better. By using data analytics, makers can look at important numbers from the production line. This helps them make smart choices and find places that need fixing to reach their production goals.
Artificial intelligence helps take things even further. It can run hard tasks on its own and guess what might happen next. AI can help spot mistakes before they turn into big problems and keep things running smoothly. This helps the system meet high quality control rules, so the results are always good.
Machine learning is also a big part of automation software today. It looks at how things happen in the factory. Then, it finds ways to make changes that help keep up with market changes. Because of this, work becomes faster, new products and processes meet what people need, and companies are ready for whatever comes next.
Integration of IoT in Production Lines
The internet of things (IoT) has changed production lines by making them work together as one. This lets people get real-time updates on how things are going and helps use resources better. The IoT devices take data from many places in the process, which gives the feedback needed to keep getting better at what they do.
IoT helps a lot with digital transformation. It makes it easier to fix things right away and can be used to spot if something might go wrong before it happens. By finding possible slow spots or problems, IoT helps keep everything safe and running. This means these places do not stop often as they used to. So, it helps keep production facilities running smooth and safe.
Also, IoT lets makers match their systems to fast-changing market demands or shifting production goals. Smart sensors and devices make it possible to change things right away when needed. This gives these places the power to switch to different tasks as needed, and keep up with changes in the industry.
The Impact of Automation on Manufacturing Efficiency
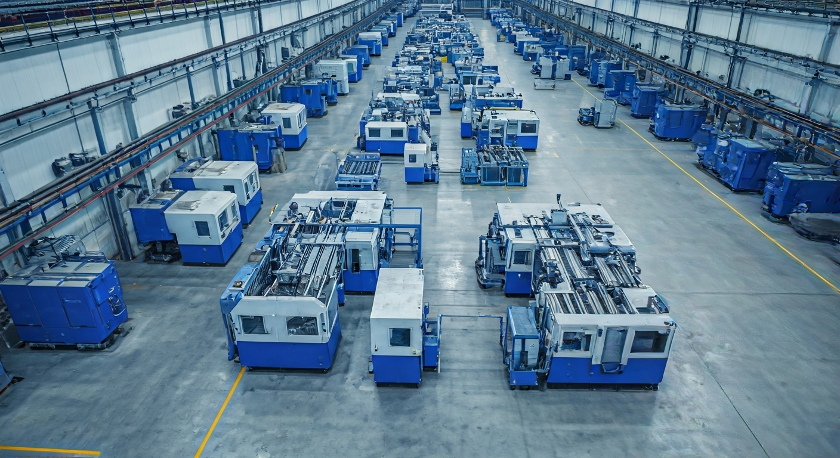
Automation has changed the way people work in modern manufacturing. When you use automated systems, you need less human intervention. These systems help to make workflows simple. They boost how much work you can get done and help to keep consistent quality in every step of the production processes. Because of this, labor costs go down and the work becomes more exact.
Also, automation cuts down mistakes in making products and makes factory floors safer. There is less risk, and things run smoother and are more organised. It helps companies keep their quality control high and reach their production goals again and again. On top of that, it lets these companies work in a way that saves money and can change with the times.
Case Studies: Before and After Automation
Before introducing automation, manufacturing efficiency often lagged due to manual limitations. Factories relied on human workers to perform repetitive tasks, which resulted in higher labor costs and inconsistent output. Challenges such as fatigue and safety risks frequently impeded progress.
With automation, assembly lines transformed into highly efficient systems, increasing production speed dramatically and reducing errors. Automated machines consistently meet production goals, achieving consistent quality and aligning with modern market demands.
Aspect | Before Automation | After Automation |
---|---|---|
Labor Costs | High due to manual labor dependency | Reduced with automated systems |
Production Speed | Slower due to human limitations | Faster with continuous operation |
Manufacturing Efficiency | Inconsistent due to errors | Enhanced with precision technology |
These improvements cement automation’s role in meeting evolving industry needs while tackling operational inefficiencies.
Speed and Precision: Quantifying Improvements
Speed and accuracy get much better with automation in the manufacturing process. Jobs that used to take hours now just take minutes. This is because of new machines and helpful software.
Automated systems are great at quality control. They keep things the same and make sure products come out right. Unlike people, machines give consistent quality and always meet industry standards. This helps people trust the brand and helps companies reach their production goals.
These changes help the company earn more money. Faster production speeds and fewer mistakes give more finished products and lower costs. With this, manufacturers can grow without losing quality.
Reduction in Human Error and Enhanced Safety
Manual manufacturing comes with human error. This can cause less work to get done and can hurt product quality. Automation systems get rid of this problem. They deliver work without errors, helping set better standards for the way quality control is done.
Safety is also a big reason why automation is important. These systems lower the need for human intervention. They take on difficult jobs, keeping human workers out of danger on busy production lines.
This change does more than just make basic safety better. It helps create a detailed, active way of working. By keeping human work to a minimum, companies can keep their teams safe and keep the line moving even when manufacturing processes get complex.
Types of Automation Used in Manufacturing
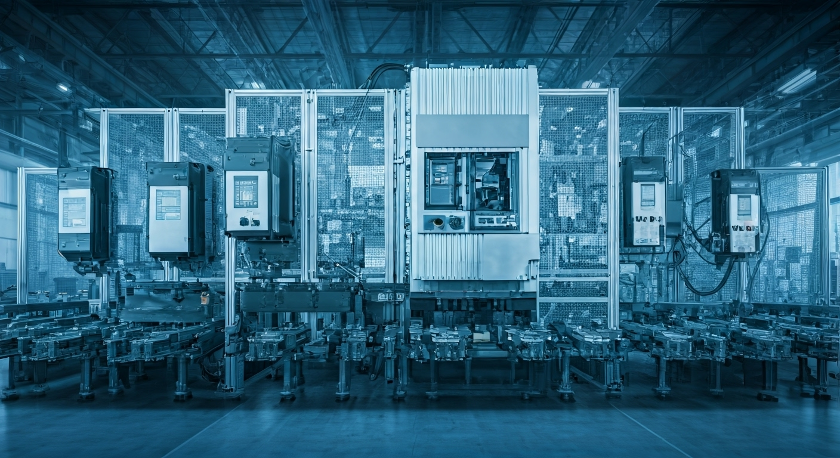
Manufacturing uses different types of automation, each one made for a special job. Fixed automation is used for tasks that have to be done the same way over and over. It works really well for assembly lines where lots of the same thing has to be made.
Programmable automation lets you change things when you need to switch between different products. This is good for batch production, where you often make small groups of a product instead of many at once.
Flexible automation is great for places that need to keep up with market demands as they change. It helps you switch to new tasks fast, with no need to stop work.
Businesses pick from these kinds of automation to help meet their production goals and to make their work smoother. This way, they can keep up with what people want and get the most out of their time and resources.
Fixed Automation Systems
Fixed automation systems are built to do set tasks again and again, very well. For example, in automotive manufacturing, fixed automation helps put together engines. It does this with great speed and a high level of detail.
These systems work best in batch production. When you need the same thing made many times, they keep everything on track. There is no need for many of the step-by-step jobs that people used to do, so mistakes are much less likely. Fixed automation is perfect for jobs that must stay the same every time.
But, it can be hard to make changes with these systems. That is why they work best for places where the way you make things does not change much. With fixed automation, companies can count on getting good results over time. This helps businesses keep up a steady flow and enjoy the same good things year after year.
Programmable Automation
Built for flexibility, programmable automation can adapt fast to market changes and shifts in production goals. With these machines, manufacturers can reprogram things as needed to match new demands or to make different products in batches.
For example, companies that make electronics use programmable automation for many product models, which helps them keep things versatile and reach customer satisfaction. This makes a big difference for industries where the needs change a lot and when there is a medium amount to produce.
Being able to switch up how things are made so easily shows the true power of programmable automation. It keeps making things flexible and helps businesses stay ahead and do well when the market is always changing.
Flexible Automation and Its Adaptability
Flexible automation is great at doing many types of manufacturing processes. It can shift between tasks fast and does not disturb the work routine. This makes it easy to keep up with changes in market demands.
Because of this, flexible automation is very helpful for industries that make custom products or work under tight deadlines. The smart software and advanced robotics used here help keep things moving well, no matter how much things change in production.
If businesses face changing consumer needs or want to make their work smoother, this technology shows how new ideas can work well in real life. Flexible automation helps people meet different challenges every year.
The Role of Robotics in Modern Manufacturing
Modern manufacturing grows with advanced robotics on assembly lines. Robotic arms can complete hard tasks like welding or putting parts together. They do these jobs with high accuracy every time.
These advanced robotics help out far beyond tasks on the production floor. They can find and fix problems while the factory runs. This lets factories keep working at their best.
Robots make tough jobs simple and bring new ways to do things in manufacturing. These advanced machines help the world use less and waste less. They improve how all the manufacturing processes work.
Implementing Automation in Existing Manufacturing Systems
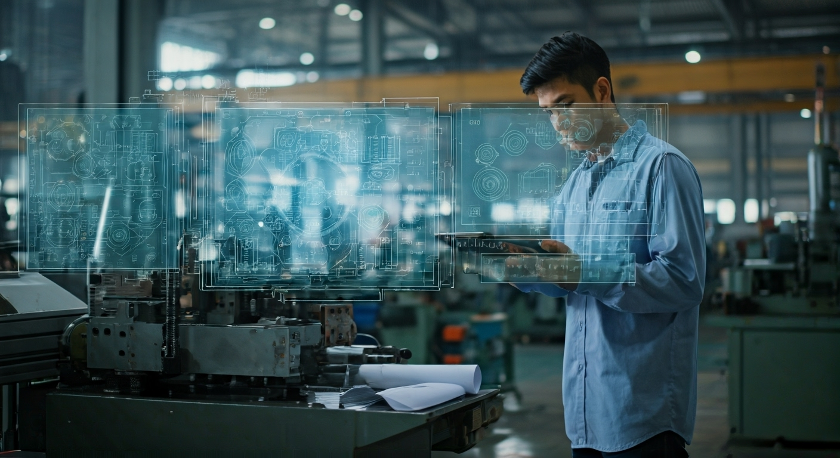
Upgrading to industrial automation needs careful planning and the right action. You have to look at your own production needs. This way, you can pick the best automation solutions for your business. It also helps to make sure all parts of the system work well together.
When you put in automated systems, you need to think about the tech side and the people who work there. You have to train your staff well. It is also good to think ahead about any problems that could come up. Make a plan for a smooth change to new ways of working. Taking these steps helps the business use industrial automation to get more work done and handle changes better.
Assessing the Need for Automation
To know if your business needs automation, you first need to look at your production needs. You also have to find the pain points in what you do now. Break down where things are slow or do not work well. This will help you see the places where automation could make things better.
The economic growth you get from automation is not only about saving money. It can give you new ideas and help your business go further. The business can grow. You can also deal with new problems faster and better. This will help with customer satisfaction, too.
When you start to see the benefit of automation in your business, you start to plan for what is coming next. This will help you put the right technology in place for both your production goals and the needs you have now and later.
Planning and Designing Automated Systems
Designing a good automation system needs a clear plan that fits advanced technology with the facility infrastructure. You have to make sure the system design matches the unique workflows in manufacturing facilities.
When you think about setting up an automation system, you need to look at more than just how it works now. Consider if it can grow with the company’s production goals. If automation solutions are flexible, they help you keep up with new market demands as they come.
Going from the first plans to putting them in place, a smart and clear automation strategy can change how you work. It brings everything up and helps boost productivity for the long run.
Challenges in Retrofitting Older Factories
Retrofitting older factories is not always easy. There are many things that get in the way, like adding new equipment and working with an old layout. The old way of setting things up is hard to change, so you may need to make big changes to how things are built to use automation.
It is very important to update the equipment because the old machines do not work well with new technology. Using modular automation and parts you can add or change out helps solve this problem.
Even though there are many challenges with retrofitting, there can be big gains in productivity and money saved. These benefits show how automation can help make old systems better.
Training Staff to Manage New Technologies
Transitioning to automation means training staff so they can use new technologies. People need to know how to work with automated tools like programmable controllers and data analytics systems. This helps the team keep things running smoothly while things change.
Regular workshops and hands-on classes let teams learn all there is to know about automation. This way, everyone sees how humans and machines can work well together in every part of the job.
Giving workers the power to learn through continuous improvement keeps everyone up to date. It also makes it easier for them to accept and use new ways in how things are made.
Future Trends in Manufacturing Automation
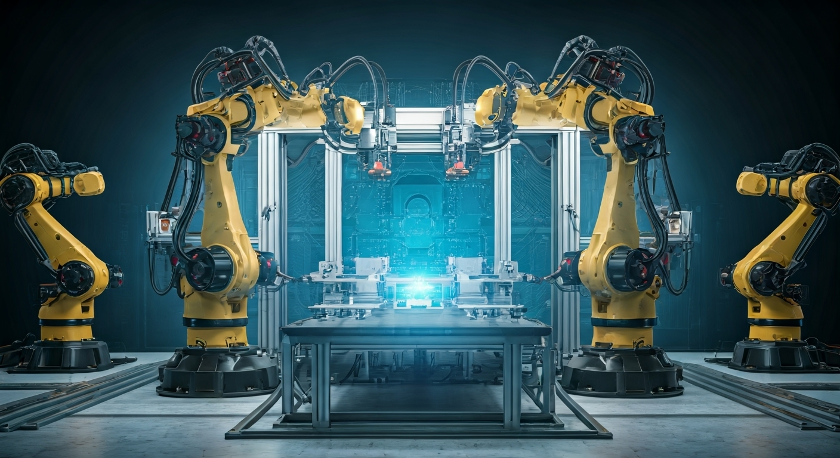
Automation technologies are changing fast these days. Machine learning and predictive maintenance help companies make better choices with data and keep equipment working well. The rise of additive manufacturing, like 3D printing, is also changing the way things are made.
At the same time, cybersecurity and sustainable practices are now at the center. They help build safe and earth-friendly ways to work. All of these changes shape how people think about new ideas, making sure that makers can meet what customers want both now and in the future.
Predictive Maintenance and Machine Learning
Machine learning helps make automated systems better at making predictions. It looks at old data to find patterns. This way, these systems can tell when there may be equipment problems. When you fix things on time, you keep everything running well.
The use of predictive maintenance does more than just stop downtime. It also helps machines last longer and cuts down repair costs. The automation system can change what it does in real time. This keeps everything working at its best.
With automated data collection, manufacturers get useful information. This helps them improve what they do. It also helps their production goals fit well with new changes in the automation system and other technology for the best outcomes.
Advances in 3D Printing and Additive Manufacturing
3D printing and additive manufacturing are changing the way things get made. These new methods help with on-demand prototyping and batch production. They let you turn hard designs into real items and cut out many extra steps.
Additive systems help manufacturers find new ideas without any limits. They help meet customer demands and get the job done with care. Companies can make custom parts and detailed prototypes. With this, people see that the things they can create seem endless.
When companies use these strong tools, they get more agile and use new ideas quicker. This big change helps automation solutions stay ready for whatever comes next.
The Growing Importance of Cybersecurity
Cybersecurity is very important now as factories use more connected systems. Keeping digital safety strong in these networks helps protect important data and makes sure production keeps running with no stops.
Today, most strategies work by stopping cyber threats before they can hurt you. They use many layers of protection with good data protection steps. This careful watch is a must for keeping factory systems safe.
By using strong cybersecurity tools and having regular checks, manufacturers can keep things safe from attacks. This helps everyone feel better about their digital transformation, knowing systems are protected at all times.
Sustainable Practices and Green Automation
The main goal of green automation is to help the industry lower energy consumption and build more eco-friendly ways to make things. When factories use automation solutions for waste and use energy from the sun or wind, they cut down the carbon they put out.
Bringing in sustainable practices does more than just solve today’s problems. It helps companies get ready for what the world expects when it comes to taking care of the environment. These automation solutions let factories make things well, while they also do less harm to the planet.
Energy-efficient automation solutions use tools like smart sensors and IoT devices. This shows that today’s technology can help companies work better and also care for the environment. These ways make businesses strong for the future.
Conclusion
To sum up, knowing about automatic manufacturing is important for any business that wants to keep up in today’s fast-moving world. When companies use new technologies like IoT and robotics, they can make things work better, cut down on mistakes, and make their workplaces safer. We talked about different types of automation, from fixed to flexible systems. Each one gives something different based on what the business needs. Using these new tools not only speeds up how things are made, but also gets a business ready for what’s ahead, like smarter working and eco-friendly ways of doing things. If you want help with automating your business, you can get in touch to talk about the best options for you.
Frequently Asked Questions
Manufacturing automation is when the company uses control systems, robots, and digital tools to help automatic production. This helps the work get done faster because the machines do many things, so there is less need for human intervention. There are different types of automation used, like fixed, programmable, and flexible systems. These ways help in getting better work and more reliable results.
Automation is changing the job market in a big way. It means there is less need for manual labor now. At the same time, it opens up chances for people to build skills in things like robotics and system management. Some jobs might go away, but workforce adaptation and reskilling programs help people learn new skills. This way, the change is balanced for everyone.
Automating a factory needs a big initial investment. You have to spend money on equipment installation and on training people. But if you do a full cost analysis, you will see a good return on investment over time. Better efficiency and higher quality of output help to cover these economic factors as the years go by.
Small-scale industries get a lot from automation benefits. These include better growth and saving costs. When businesses use modern technology, they can stay efficient. It also helps them keep up with bigger companies in the same field.
Common automation systems use industrial robots, programmable logic controllers, and tools that connect to the Internet of Things. These technologies follow industry standards. They help make operations more steady and efficient in many types of manufacturing. With these tools, people see good changes in how work gets done. Many use them to get better results and save time.
Benefits of Automation for Product Quality and Consistency
Automation helps make sure that the product quality stays high and the results are always the same. It meets the tough quality assurance rules every time. The advantages of automation are better accuracy and following manufacturing standards well. This helps with efficiency and makes the process more dependable.
Enhancing Product Quality Through Precise Control
In automated systems, good control plays a key role in keeping product quality high. New tools help make sure automation stays exact. This helps keep quality control strong at every step in the process.
Consistent Output: Meeting Industry Standards Every Time
Automated manufacturing helps to make sure there is always a steady and reliable output. It meets the strong industry rules for both reliability and how steady the process is. This system gets rid of mistakes that people can make, so all production stays right in line with the set standards for good quality every time.