What Is Fixed Automation?
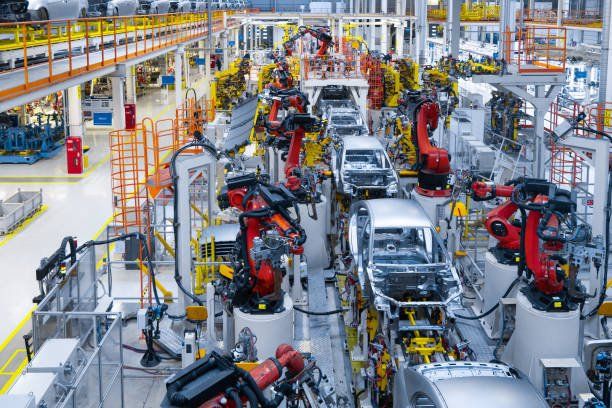
Stationary automation is a modern and efficient type of production process in which the sequence of technological operations is determined by the equipment settings. Stationary automation systems, or "hard automation", are typically used for production systems with exclusively dedicated equipment and large volume high production requirements. Fixed automated manufacturing, also called rigid automation, is a system in which automated manufacturing processes and assembly are set up to produce a single product.
Fixed automation, also known as hard automation, refers to systems designed to produce a single type of product. Fixed (complex) automation typically involves a set of repetitive or fixed sequences (hence the name), such as the assembly or processing of a product. This type of manufacturing automation uses specialized or specialized hardware to automate assembly or fixed sequential processing operations.
In this automation system, it is possible to modify a certain class of product modifications, as well as assembly or machining operations with a change in the control program in automated equipment. This automation system provides automatic control equipment for greater flexibility in making product design changes. Programmable automation is the best solution for companies that are constantly changing the products they make or the activities they carry out, whether it's business or customer contact.
Unlike fixed automation, programmable automation describes the process of mass production of a product in which production equipment needs to be reprogrammed to accommodate production environments and the new style of the next batch of products. In the case of fixed automation, the machining or assembly operations in the system are fixed by the equipment configuration, while in the case of programmable automation, the production equipment can change the sequence of operations to be able to handle different product configurations. An important feature of stationary automation is that the sequence of production operations is fixed by the design of the production equipment, so the sequence cannot be easily changed later in the product life cycle.
Despite the high initial investment costs, a stationary automation system is suitable for high-volume production processes where products do not change much over time. The initial installation of stationary automation can be costly due to the equipment required, but in turn, stationary automation provides high productivity.
Examples of stationary automation systems include automated assembly machines, chemical manufacturing processes, material handling conveyor systems, paint and coating automation processes, and process lines. Stationary automation systems are mainly used in discrete mass production and continuous flow systems such as paint shops, distillation processes, transfer lines and conveyors. Flexible automation systems link multiple machines together through a material handling system, and human operators enter commands using computer code or a human-machine interface (HMI), allowing them to centrally control production and operations from a control desk.
Flexible automation uses a human-controlled centralized computer that controls and updates the production process, as well as a material handling system that groups its machines. This type of automation, called "soft automation", is used in computer-controlled flexible manufacturing systems and enables more flexible production. This type of automation can include technologies such as flexible handling systems, automated material handling, and automated manufacturing.