Industrial HMI
What Is an Industrial HMI
An industrial HMI, or Human-Machine Interface, is a technology used in manufacturing to facilitate interaction between humans and machines. It typically consists of a touchscreen display, buttons, and indicators, allowing operators to monitor and control machinery and processes. An industrial HMI provides real-time data visualization, control functionalities, and alerts, enabling operators to make informed decisions and adjustments. With the emergence of Industry 5.0 principles, HMIs are evolving to foster greater collaboration between humans and machines, emphasizing human-centric design and intuitive interfaces. Industry 5.0 PPT highlights how HMIs are adapting to empower workers with enhanced control and decision-making capabilities, fostering a more symbiotic relationship between humans and machines in manufacturing environments.
What Is HMI
Human-Machine Interface (HMI) refers to the dashboard through which a user interacts with a machine, system, or device. This interface can include displays, controls, and software that allow users to input commands and receive real-time feedback from the system. HMIs are used across various fields, including industrial automation, vehicles, consumer electronics, and medical equipment, to facilitate intuitive and efficient interaction between humans and technology. They play a critical role in enhancing user experience, improving operational efficiency, and ensuring safety in technological interactions.
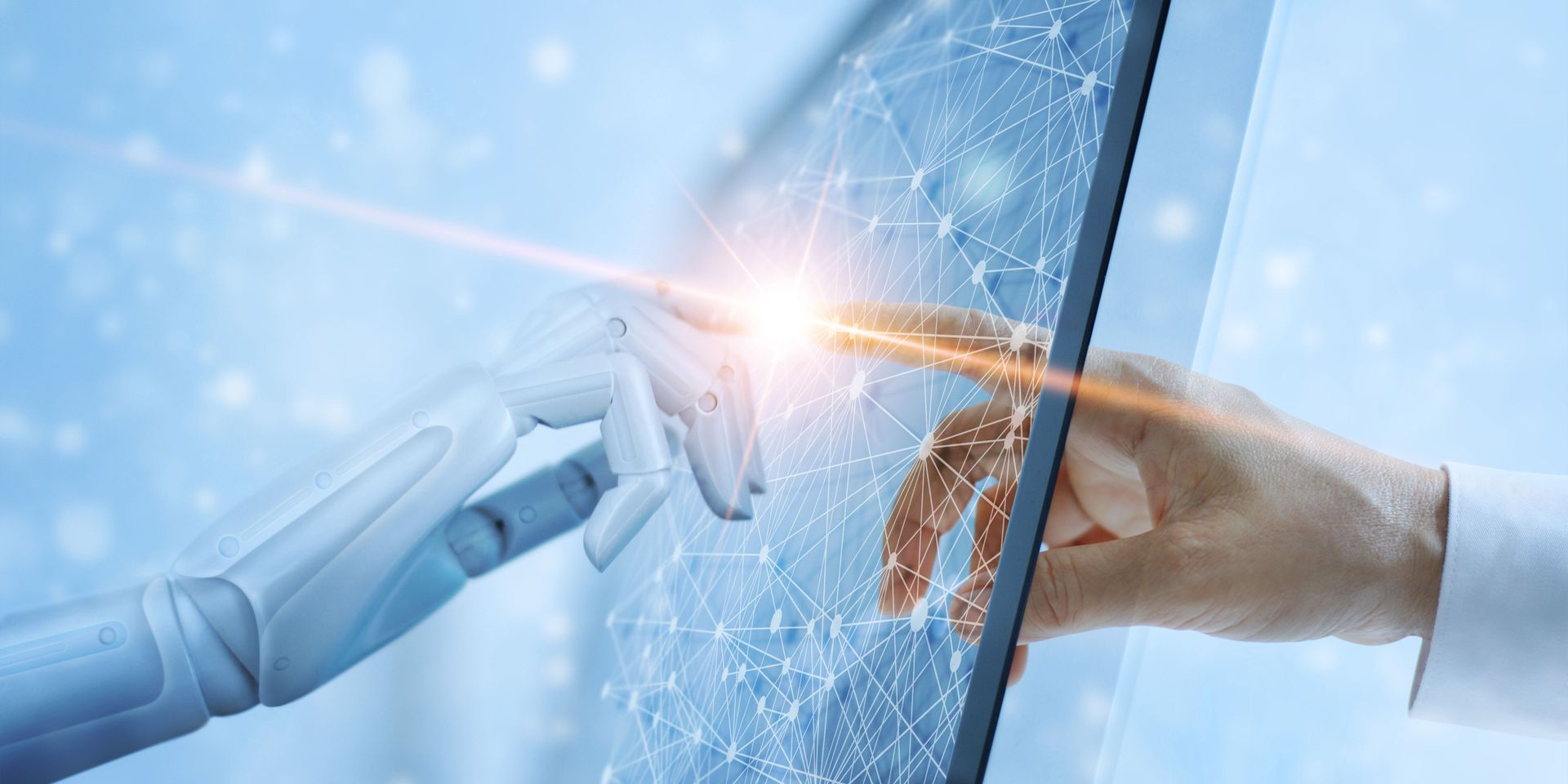
What Is HMI in PLC
HMI (Human-Machine Interface) in PLC (Programmable Logic Controller) refers to the graphical interface that allows operators to interact with and monitor the PLC-controlled machinery or processes. The HMI typically consists of a display screen, buttons, switches, and indicators that provide real-time feedback and control capabilities. Operators can use the HMI to view system status, adjust parameters, input commands, and respond to alarms or alerts. HMI in PLC systems plays a crucial role in facilitating user-friendly control and monitoring of industrial automation processes, enhancing efficiency, and ensuring smooth operation.
Advantech HMI Software
Advantech HMI software refers to the suite of visualization and control applications developed by Advantech for use in its human-machine interfaces. Advantech, a leading provider of industrial computing solutions, offers software that is specifically designed to help users create customizable, scalable, and robust HMI systems to monitor and control industrial processes. The software typically features intuitive design tools, powerful data handling capabilities, and supports connectivity with a wide range of automation hardware. This allows operators to efficiently manage industrial operations, visualize process data, and interact with automated systems, enhancing overall productivity and operational safety in industrial environments.
Advantech Panel PC
An Advantech Panel PC is an all-in-one industrial computer integrated into a flat panel display, designed to provide powerful computing capabilities along with robust HMI features for various industrial applications. These panel PCs are built to withstand harsh environments, featuring rugged construction with dust and water resistance, and often include touch screen interfaces for easy interaction. Advantech Panel PCs are equipped with powerful processors, a variety of input/output options, and are capable of running various operating systems, such as Windows or Linux, making them suitable for tasks ranging from factory automation to control room operations. They are commonly used in sectors like manufacturing, logistics, healthcare, and retail, where reliable and efficient computer access is crucial in the operational environment.
Advantech Operator Panel
An Advantech operator panel is a type of human-machine interface (HMI) device designed for industrial applications, allowing operators to interact with machines and control systems. These panels typically feature a combination of display screens, input buttons, and function keys, providing a user-friendly interface for monitoring and controlling industrial processes. Advantech operator panels are known for their durability, reliability, and versatility, making them suitable for use in harsh environments such as manufacturing plants, warehouses, and outdoor installations. They often integrate seamlessly with Advantech's software solutions and can communicate with various industrial devices and networks, facilitating efficient operation and management of industrial equipment and processes.
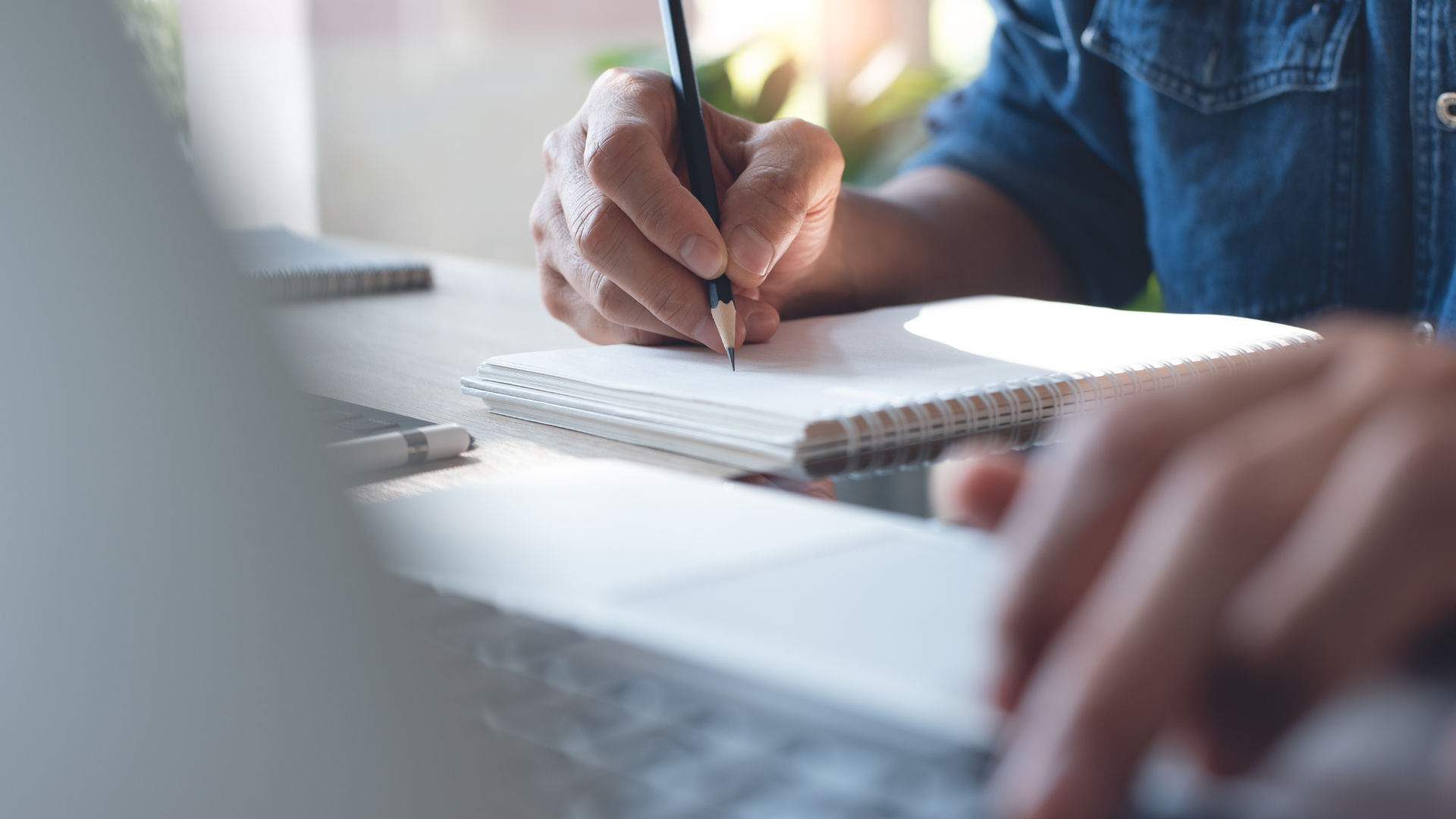
What Is HMI in Scada
In SCADA (Supervisory Control and Data Acquisition) systems, HMI (Human-Machine Interface) refers to the graphical user interface through which operators interact with the SCADA system. The HMI provides real-time data visualization, control, and monitoring functionalities, allowing operators to oversee industrial processes and machinery. It typically includes features such as dynamic graphical displays, alarm management, trend analysis, and reporting tools to facilitate efficient decision-making and control. HMI in SCADA systems plays a crucial role in enabling operators to monitor process variables, issue commands, and respond to alarms, ultimately ensuring the smooth and safe operation of industrial processes.
What Is an Example of HMI
An example of HMI (Human-Machine Interface) is the touchscreen display on a manufacturing machine that allows operators to monitor the machine's performance, adjust settings, and input commands. For instance, in a factory setting, a large touchscreen panel mounted on a production line machine may display real-time data such as temperature, pressure, and speed. Operators can interact with the HMI by tapping icons or inputting values using the touchscreen to make adjustments or respond to alarms. This HMI enables operators to efficiently control and monitor the machine's operation, contributing to improved productivity and quality in the manufacturing process.
Advantech Webaccess HMI
Advantech WebAccess HMI is a software platform developed by Advantech for building and managing human-machine interface (HMI) applications in industrial automation and control systems. It provides a web-based environment for creating, deploying, and managing HMI projects, allowing users to visualize and control industrial processes remotely through standard web browsers. WebAccess HMI offers features such as intuitive drag-and-drop interface design, real-time data visualization, alarm management, historical data logging, and secure remote access. It is compatible with various Advantech hardware platforms and supports integration with different industrial protocols and third-party devices, enabling flexible and scalable solutions for diverse industrial applications.
Phoenix Contact Display
Phoenix Contact offers a range of displays primarily designed for industrial applications. These displays, often referred to as Human-Machine Interfaces (HMIs), are used in conjunction with automation systems to provide operators with a user-friendly interface for monitoring and controlling processes.
Phoenix Contact displays typically feature rugged construction to withstand harsh industrial environments, including resistance to dust, water, and temperature extremes. They often come in various sizes with options for touch screen functionality, allowing operators to interact directly with the display to input commands and access data.
These displays may also integrate with Phoenix Contact's automation software and hardware solutions, providing seamless communication and integration within industrial control systems. Overall, Phoenix Contact displays serve as essential components in industrial automation setups, facilitating efficient and intuitive operation of machinery and processes.
Phoenix Contact Software
Phoenix Contact offers a variety of software solutions tailored to meet the needs of industrial automation and control systems. These software offerings cover a range of functions, including programming, configuration, monitoring, and maintenance of automation equipment.
Some of the common types of software provided by Phoenix Contact include:
- Programming Software: This software is used for programming programmable logic controllers (PLCs), human-machine interfaces (HMIs), and other automation devices. It allows users to create logic sequences, configure input/output modules, and develop custom applications to control industrial processes.
- Configuration Software: Configuration software is used to set up and customize Phoenix Contact's hardware components, such as industrial switches, routers, and I/O modules. It enables users to configure network settings, assign IP addresses, and optimize device parameters to suit specific application requirements.
- Monitoring Software: Monitoring software provides real-time visualization and data logging capabilities for monitoring industrial processes. It allows operators to view process variables, analyze trends, and receive alarms or notifications when abnormalities occur, enabling timely intervention and troubleshooting.
- Maintenance Software: Maintenance software helps streamline the maintenance and diagnostics of automation systems by providing tools for asset management, predictive maintenance, and remote troubleshooting. It enables users to monitor equipment health, schedule maintenance tasks, and perform diagnostics to ensure the reliability and availability of industrial assets.
These software solutions from Phoenix Contact are designed to work seamlessly with their hardware products, offering integrated solutions for industrial automation applications across various industries.
What Are the Three Types of HMI
The three main types of HMI (Human-Machine Interface) commonly found in industrial settings are panel-based HMIs, PC-based HMIs, and web-based HMIs. Panel-based HMIs typically consist of physical displays mounted on machinery or control panels, featuring touchscreen functionality for direct interaction with operators. PC-based HMIs utilize personal computers or industrial-grade PCs as the platform for the interface, running specialized software for advanced visualization and connectivity features. Web-based HMIs leverage web technologies to provide remote access to control and monitoring interfaces through web browsers, enabling operators to monitor processes from anywhere with internet access. Each type of HMI offers unique advantages and applications, catering to diverse industrial needs and preferences.
The three main types of HMI (Human-Machine Interface) commonly used in industrial settings are:
- Panel-based HMIs: These HMIs typically consist of a physical display panel mounted on a machine or control panel, often with touchscreen capabilities. Panel-based HMIs are directly integrated into the machinery or equipment they control and provide operators with a localized interface for monitoring and controlling processes.
- PC-based HMIs: PC-based HMIs utilize standard personal computers or industrial-grade PCs as the platform for the interface. These HMIs often run specialized software that provides advanced visualization, data processing, and connectivity features. PC-based HMIs offer flexibility and scalability, allowing for the integration of additional software applications and connectivity with various industrial networks.
- Web-based HMIs: Web-based HMIs leverage web technologies to provide remote access to control and monitoring interfaces through web browsers. These HMIs are accessed via network-connected devices such as computers, tablets, or smartphones, enabling operators to monitor and control processes from anywhere with internet access. Web-based HMIs offer increased accessibility and flexibility, making them ideal for distributed control systems and remote monitoring applications.