What Does an OPC Server Look Like?
What Does An OPC Server Look Like?
When considering the realm of Supervisory Control and Data Acquisition (SCADA) systems, it is of utmost importance to recognize and appreciate the pivotal role that OPC (OLE for Process Control) servers play. These servers serve as a crucial component within the SCADA infrastructure, facilitating seamless communication between various devices, sensors, and software applications. By leveraging OPC servers, organizations can ensure efficient data exchange and real-time monitoring capability within their SCADA systems, ultimately enhancing overall operational efficiency and system reliability. These servers serve as a vital conduit, enabling uninterrupted and efficient communication between an array of devices and diverse software applications. The OPC (OLE for Process Control) protocol is widely embraced and adopted within the industrial automation domain. This protocol plays a pivotal role in facilitating seamless interoperability among various industrial automation systems, regardless of their diverse configurations and manufacturers. By utilizing the power of OPC (OLE for Process Control), organizations can effectively integrate and establish seamless communication channels between various heterogeneous systems. This integration leads to a remarkable enhancement in operational efficiency, as well as the streamlining of essential processes. As a result, productivity levels experience a significant boost across the entire industrial landscape.
An
OPC server plays a crucial role as a vital intermediary, facilitating the smooth and efficient exchange of data between SCADA (Supervisory Control and Data Acquisition) systems and a diverse range of devices. These devices encompass an extensive array of components, including sensors, controllers, and various other equipment. The OPC server acts as a seamless bridge, enabling seamless interoperability among these different components to ensure uninterrupted communication and effective data management in industrial automation processes. By acting as a bridge between these components, the OPC server enables the smooth flow of information, ensuring optimal communication and synchronization within the industrial ecosystem. It functions as a crucial intermediary, seamlessly bridging the gap between the multitude of devices and the SCADA software. With utmost grace and precision, this interface diligently takes on the formidable task of seamlessly translating the intricately complex and diverse data generated by these sophisticated devices into a meticulously standardized format that effortlessly resonates with SCADA systems. Through its unparalleled ability to harmonize disparate data sources, this interface enables a seamless exchange of information, thereby ensuring smooth communication between various components within the industrial ecosystem.
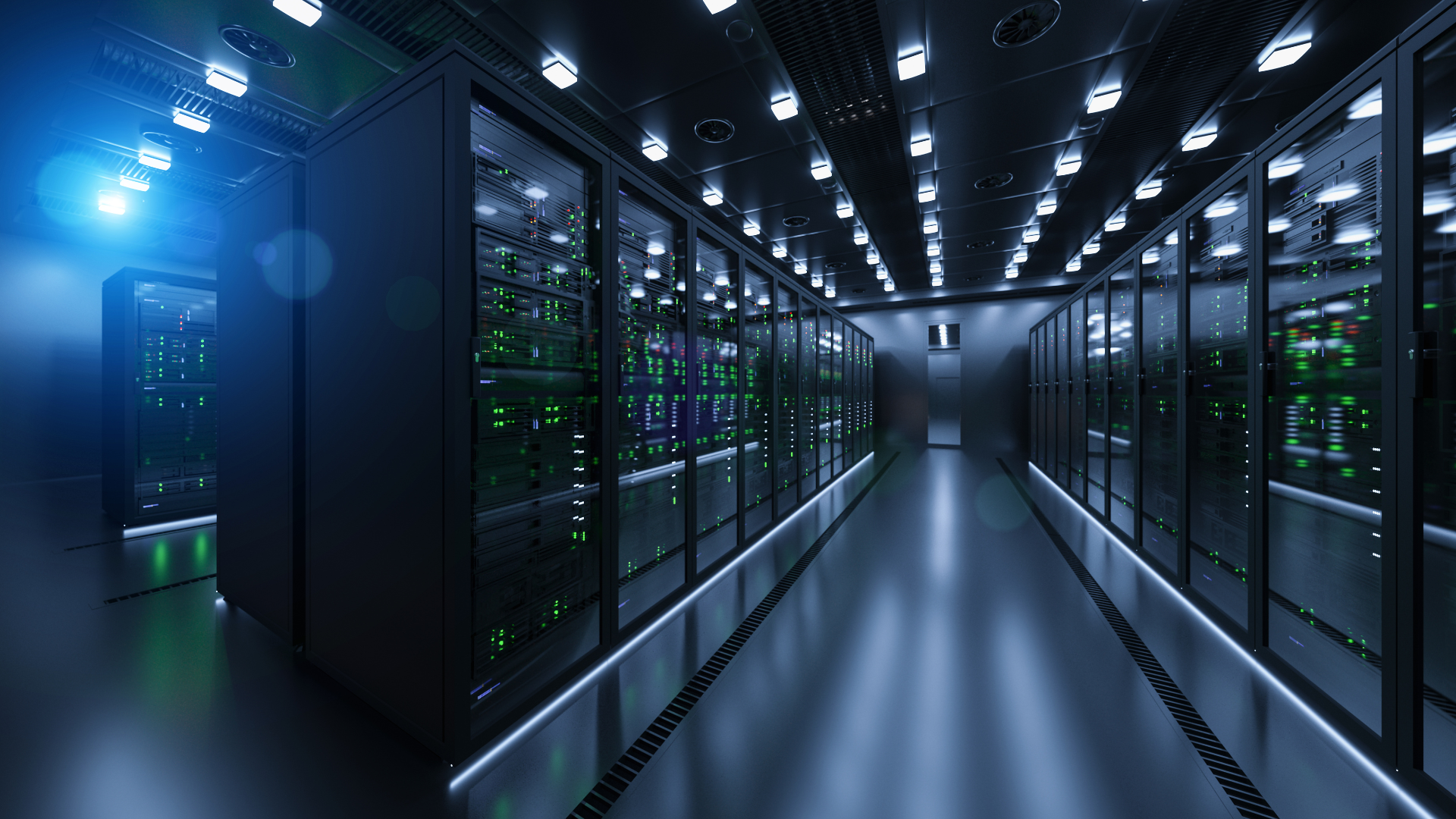
When examining the domain of OPC (OLE for Process Control) servers, it is essential to acknowledge the presence of a wide array of diverse alternatives. These encompass the well-established OPC DA (Data Access) servers as well as the more modern OPC UA (Unified Architecture) servers. Both serve distinct purposes and offer unique features, catering to various requirements in the fields of process control and industrial automation. OPC DA, which stands for OLE for Process Control Data Access, primarily emphasizes the exchange of real-time data. On the other hand, OPC UA, which stands for Unified Architecture, provides a more comprehensive solution by offering advanced security features and supporting complex data models. By adopting OPC UA, organizations can ensure heightened protection of their data and communication channels while also benefiting from the ability to handle intricate data structures efficiently. The enhanced functionality offered by OPC UA makes it an optimal and highly suitable choice for industries that prioritize stringent security measures and handle intricate data exchanges in their day-to-day operations. This advanced protocol ensures robust protection against potential security threats and addresses the complex requirements of data transmission in a seamless manner, making it a preferred solution for such industries.
To successfully set up an OPC server, it is customary and recommended to employ specialized software that is exclusively developed to facilitate this specific functionality. This dedicated software solution is designed with the primary purpose of enabling the seamless establishment and smooth operation of an OPC server. By utilizing such sophisticated software, organizations can ensure a more efficient and effective deployment of their OPC servers, allowing for seamless integration and communication between different devices and systems. Several prominent examples of such software include the Matrikon OPC server software, as well as various commendable offerings from reputable vendors within the industry. It is of utmost importance to emphasize that while certain vendors may provide free trial versions of their products, it should be noted that this may not be the case for all OPC server software offerings.
The OPC Foundation holds an esteemed and paramount position in the realm of diligently developing and tirelessly advancing the standardization of the OPC protocol. Through its unwavering dedication, the foundation actively engages in shaping, fostering, and propelling the widespread adoption of this protocol across diverse industries. It is through their steadfast efforts that they have become a driving force in promoting interoperability and seamless communication in industrial automation systems. By fostering collaboration and consensus among industry experts, the OPC Foundation ensures that businesses can seamlessly integrate their systems and devices through a well-established, universally accepted communication framework.
Through its tireless efforts, the foundation paves the way for enhanced interoperability, improved efficiency, and increased productivity across diverse sectors. These OPC Servers go above and beyond by offering a comprehensive array of resources, including meticulously crafted tutorials and detailed guidelines. These invaluable resources have been meticulously crafted with the intention of not only assisting users in understanding the intricacies of this state-of-the-art technology but also empowering them to effortlessly incorporate it into their daily operations with the utmost efficacy.
In its fundamental essence, it can be concisely expressed that an OPC server assumes a pivotal and indispensable role in facilitating resilient and reliable communication between Supervisory Control and Data Acquisition (SCADA) systems and diverse industrial devices. In the realm of server options, there exists a diverse range of choices one can consider. Nevertheless, it is imperative to meticulously evaluate and choose the server that best aligns harmoniously with your distinct and precise requisites.