What Is Industry 4.0 in Simple Words?
What Is Industry 4.0 in Simple Words?
Industry 4.0 technologies meaning, often referred to as the Fourth Industrial Revolution, is a concept that emphasizes the integration of cutting-edge technologies and automation across multiple industries. This revolutionary transformation is driven by advancements in artificial intelligence, robotics, the Internet of Things (IoT), big data analytics, and other emerging technologies. The main objective of Industry 4.0 is to create smart factories and interconnected systems that can optimize productivity, enhance efficiency, and enable seamless communication between machines and humans. By leveraging these advanced technologies, industries can unlock new possibilities for innovation, improve operational processes, and achieve significant economic growth in the digital age. The emergence of AI technology in manufacturing and other sectors signifies a profound transformation in the way these industries function. With the integration of AI, businesses can optimize their operations, streamline production processes, and enhance overall efficiency. This shift enables companies to leverage data-driven insights, automate repetitive tasks, and make more informed decisions. By embracing AI-powered solutions, organizations can unlock new levels of productivity and competitiveness in today's rapidly evolving business landscape.
In simplified terms, Industry 4.0 refers to the adoption and integration of various cutting-edge technologies, including artificial intelligence (AI), Internet of things (IoT), big data analytics, robotics, and cloud computing, in order to revolutionize manufacturing processes and establish smart factories. By harnessing the power of these technologies, companies can automate and optimize their operations, enabling them to achieve greater efficiency, productivity, and flexibility. AI enables machines to learn and make intelligent decisions autonomously, while IoT connects devices and facilitates data exchange for enhanced communication and collaboration. Big data analytics allows for the extraction of valuable insights from vast amounts of data generated by these systems. Robotics plays a pivotal role in automating physical tasks in a precise manner. Lastly, cloud computing provides a scalable infrastructure for storing and processing data securely. Together, these technological advancements propel the industry toward a more connected and intelligent future. The advent of these cutting-edge technologies has revolutionized the way machines and systems communicate with one another. They have empowered machines to not only exchange information but also collect vast amounts of data from various sources. This data is then analyzed in real time, allowing for quick and informed decision-making. These advanced systems have the ability to autonomously process and interpret complex information, leading to increased efficiency and accuracy in a wide range of industries.
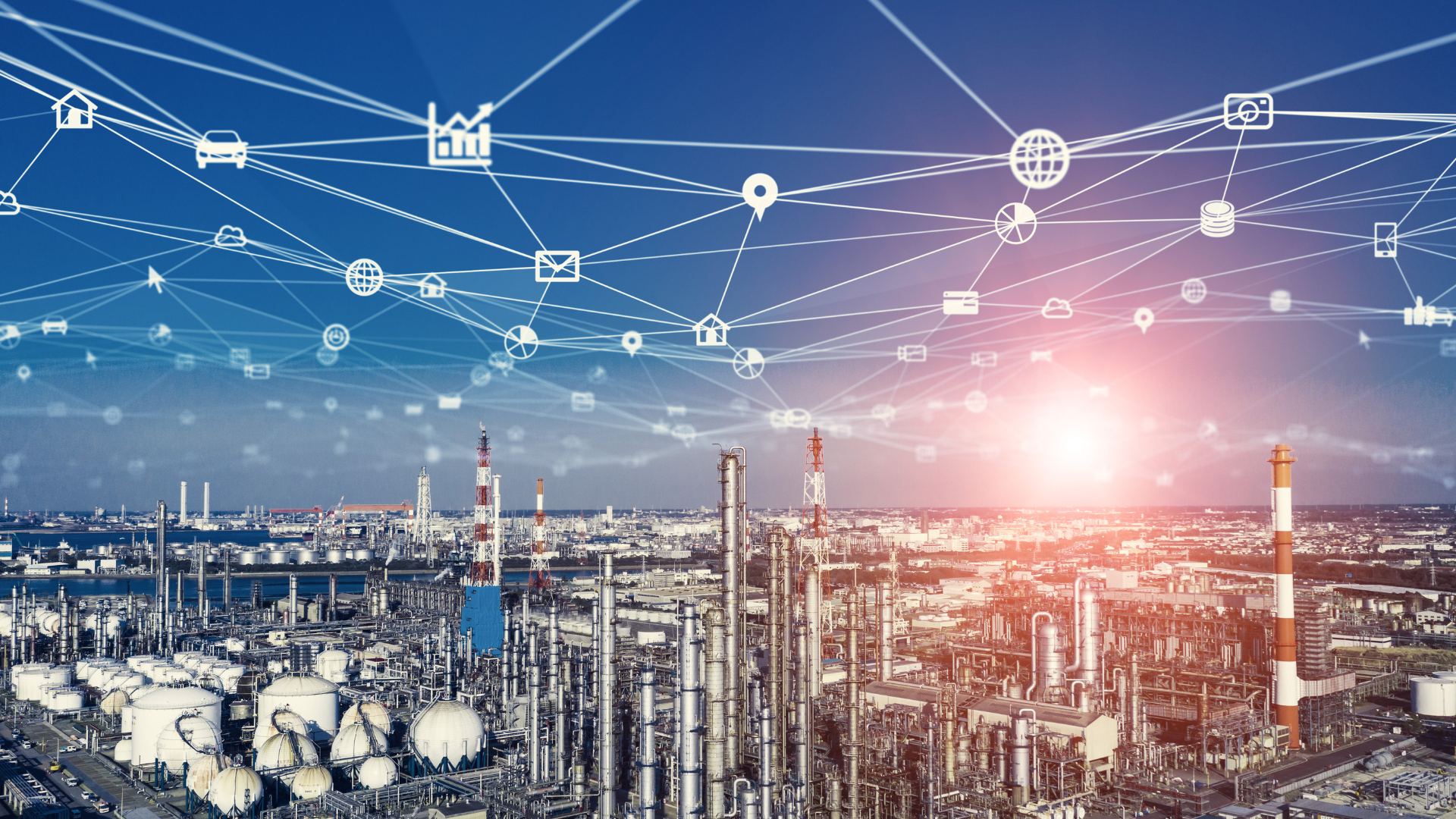
In the realm of Industry 4.0, numerous cutting-edge technologies have emerged, revolutionizing the way businesses operate. One such example is the utilization of smart sensors, which play a pivotal role in monitoring machine performance. These intelligent sensors have the capability to collect and analyze vast amounts of data in real time, enabling companies to make informed decisions regarding maintenance and productivity optimization. Another remarkable technology within Industry 4.0 is predictive maintenance systems. By leveraging advanced algorithms and machine learning techniques, these systems can detect potential failures before they even manifest, allowing businesses to proactively address issues and prevent costly downtime. This not only enhances operational efficiency but also helps save substantial amounts of time and resources that would otherwise be spent on reactive maintenance.
The integration of these Industry 4.0 technologies empowers organizations to achieve higher levels of productivity, reduce operational costs, and improve overall equipment effectiveness (OEE). It allows them to move away from traditional methods that heavily rely on manual inspection and intervention towards a more data-driven approach that promotes predictive decision-making for sustainable growth in today's increasingly competitive landscape. Collaborative robots, commonly known as cobots, have revolutionized the manufacturing industry by working in close collaboration with human workers on the factory floor. These intelligent machines are designed to assist and support human tasks, enhancing productivity and efficiency while ensuring safety. Another remarkable technological advancement is the concept of digital twins. Digital twins are virtual replicas of physical assets, such as machinery or equipment, that can be created for testing and optimization purposes. This innovative technology allows engineers and designers to simulate real-world scenarios without the need for physical prototypes, resulting in significant cost savings and accelerated development cycles. By deploying cobots in conjunction with digital twins, manufacturers can achieve seamless integration between physical and virtual realms. This symbiotic relationship enables companies to iterate designs efficiently, identify potential issues before production begins, optimize workflows, and streamline overall operational processes. The combination of collaborative robots and digital twins represents a powerful duo that not only enhances productivity but also contributes to improved product quality and reduced time-to-market. As automation continues to evolve alongside cutting-edge technologies like artificial intelligence and machine learning, the future of manufacturing looks promising indeed.
The benefits that can be derived from embracing Industry 4.0 are indeed numerous and far-reaching. This revolutionary industrial paradigm shift is characterized by the integration of advanced technologies such as artificial intelligence, the Internet of Things, big data analytics, and automation into traditional manufacturing processes. One of the key advantages of Industry 4.0 is increased efficiency and productivity. By leveraging intelligent systems and interconnected machines, companies can optimize their operations, improve production processes, and reduce downtime. This ultimately leads to cost savings, enhanced output quality, and shorter product development cycles. Moreover, Industry 4.0 enables greater flexibility in manufacturing operations. With the ability to quickly adapt to changing market demands through real-time data analysis and predictive modeling, businesses can respond more effectively to customer needs. This agility allows for customized production runs, just-in-time inventory management, and rapid prototyping. Another significant benefit lies in the realm of predictive maintenance. Through continuous monitoring of equipment performance using sensors and data analytics tools, potential failures can be detected early on. This proactive approach minimizes unplanned downtime and optimizes maintenance schedules for maximum equipment utilization. Furthermore, Industry 4.0 promotes sustainable practices by fostering resource efficiency in various ways. By leveraging advanced analytics to identify energy consumption patterns or optimize supply chains through smart logistics solutions, companies can minimize their environmental footprint while also reducing costs. Last but not leastly, Industry 4.0 brings about new business models and revenue streams through servitization - the shift towards offering not just products but also value-added services bundled with them.
Companies can leverage advanced technologies like IoT-enabled features or remote monitoring capabilities to provide additional services such as predictive maintenance or performance optimization programs for their customers. In conclusion, Industry 4.0 offers a multitude of benefits that span across various facets of business operations including increased efficiency, flexibility, improved maintenance practices, sustainability, and new revenue opportunities. Embracing this transformative era holds immense potential for companies seeking to stay competitive in the ever-evolving global marketplace. The utilization of Industry 4.0 in the workplace can have a significant impact on productivity and efficiency. By leveraging the power of artificial intelligence, these tools are able to optimize various processes and minimize downtime. This leads to streamlined workflows and improved overall output. With their ability to automate repetitive tasks, technology can free up valuable time for employees to focus on more strategic and high-priority activities. This not only boosts productivity but also allows for greater creativity and innovation within the organization. Furthermore, these advanced tools are equipped with algorithms that continuously learn from user interactions, making them increasingly efficient over time. By analyzing patterns, identifying common errors, and suggesting improvements, they help enhance the quality of written content while reducing the need for extensive editing or proofreading. In addition to optimizing processes. It enables better decision-making through real-time data analysis. It also offers opportunities for customization and personalization in manufacturing by leveraging data-driven insights.
However, like any technological advancement, there are advantages as well as disadvantages associated with Industry 4.0 implementation. Some advantages include improved safety conditions for workers through the automation of hazardous tasks and the creation of new job roles related to managing these advanced technologies. On the other hand, challenges such as cybersecurity risks, job displacement due to automation, and the need for upskilling or reskilling workers may arise.
The key impacts of the Fourth Industrial Revolution are far-reaching across industries globally. It disrupts traditional business models by transforming supply chains into interconnected networks with enhanced visibility and traceability. It fosters innovation through the convergence of physical systems with digital technologies.
To delve deeper into understanding Industry 4.0 concepts or their implications on manufacturing or other sectors specifically mentioned in PDF format or explore more about its various technological aspects, referring to industry-specific reports or research papers can provide valuable insights.