What is a SCADA and HMI System?
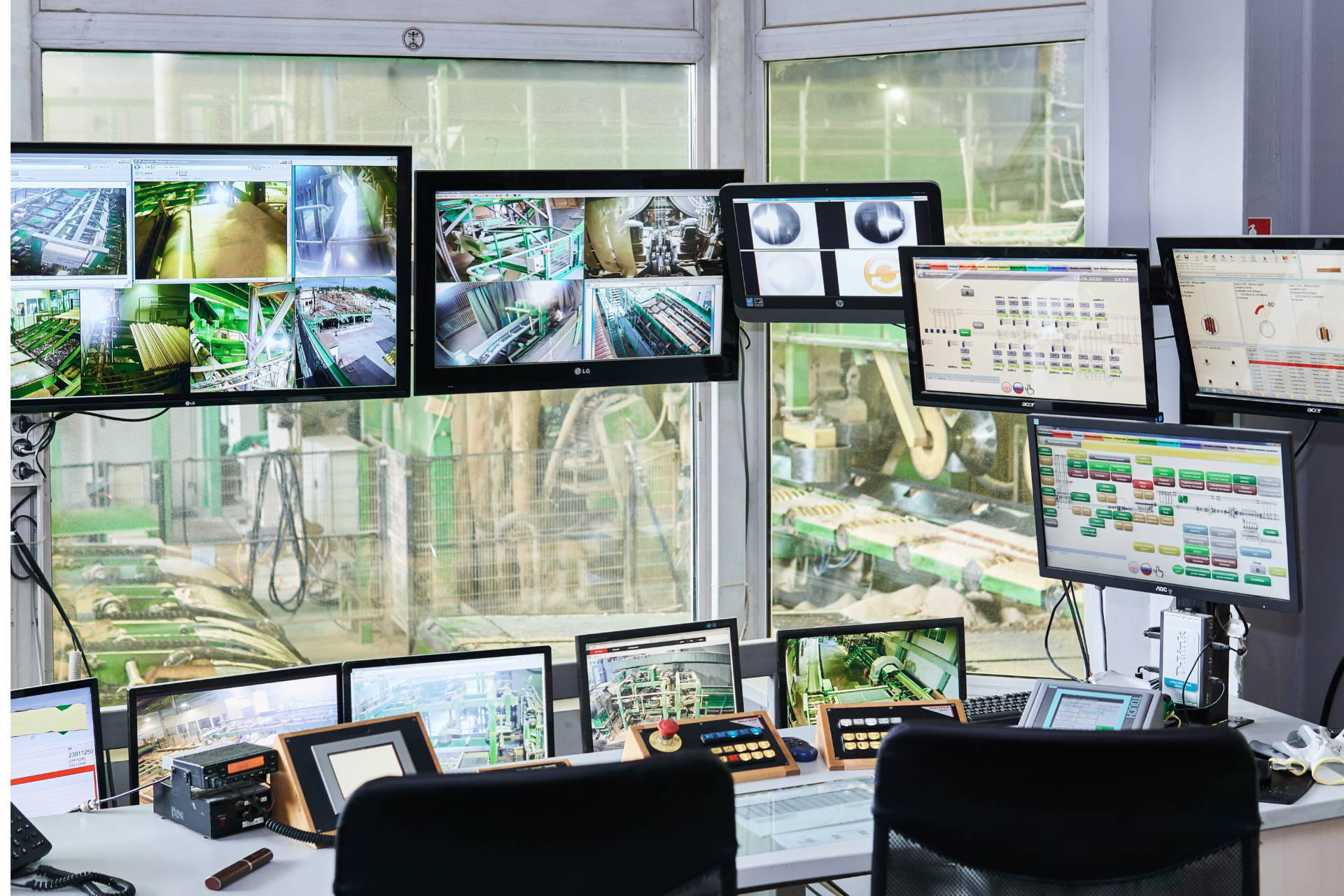
The SCADA system monitors the entire process through sensors connected to computers which then send data back to the central computer. The HMI displays this data in real-time on screens in order for operators to make decisions on how to handle any issues that may arise. Learn more about HMI SCADA.
A SCADA (Supervisory Control and Data Acquisition) system is a software application used to monitor and control industrial processes. It provides a centralized platform for collecting real-time data from sensors, analyzing and processing that data, and enabling operators to control the process remotely. The SCADA system plays a vital role in various industries, including manufacturing, energy, oil and gas, water and wastewater treatment, transportation, and more.
The key components of a SCADA system include:
Data Acquisition: SCADA systems acquire data from remote devices, such as sensors, actuators, and meters, distributed throughout the industrial process. These devices measure parameters such as temperature, pressure, flow rate, and level. The data is collected by programmable logic controllers (PLCs) or remote terminal units (RTUs) and transmitted to the central SCADA system for further processing.
Communication Infrastructure: SCADA systems rely on a robust communication network to facilitate data transmission between the field devices and the central SCADA server. This can include wired communication protocols like Ethernet, serial communication (RS-232, RS-485), or wireless technologies such as Wi-Fi, cellular networks, or radio frequency (RF) communication.
Data Processing and Analysis: Once the data is collected by the SCADA system, it is processed and analyzed to provide real-time insights.
An HMI system, which is a type of SCADA system, specifically focuses on the human-machine interface aspect. It combines hardware and software components to enable operators to interact with the SCADA system and control the industrial process. The HMI system provides an intuitive and user-friendly interface that allows operators to monitor the process, view critical parameters, and control equipment with ease.
The HMI system typically includes the following components:
Hardware: This includes displays such as touchscreens, monitors, and indicator lights that provide visual feedback to the operators. Input devices like keyboards, mice, and touch panels are used to interact with the HMI software.
HMI Software: The software component runs on the central SCADA server or a dedicated HMI workstation. It provides the graphical user interface (GUI) that operators use to monitor the process. The software enables real-time data visualization, trending, alarm management, historical data retrieval, and reporting. It also allows operators to control the process by adjusting setpoints, initiating commands, and executing predefined sequences.
The combination of SCADA and HMI systems provides numerous benefits for industrial processes:
Real-time Monitoring: SCADA and HMI systems offer real-time monitoring capabilities, allowing operators to have a comprehensive view of the process. This enables early detection of anomalies, deviations, and equipment malfunctions, facilitating proactive decision-making and reducing downtime.
Enhanced Control: Operators can remotely control the process through the HMI system, adjusting setpoints, changing operating parameters, and controlling equipment. This provides flexibility and agility in responding to changing process conditions and optimizing performance.
Data Storage and Historical Analysis: SCADA systems often include a data historian component that stores historical data for further analysis. This allows operators and engineers to analyze past trends, conduct performance evaluations, and identify areas for improvement. Historical data analysis can also aid in troubleshooting and optimizing processes.
Remote Access and Control: SCADA and HMI systems can provide remote access capabilities, allowing authorized personnel to monitor and control processes from anywhere with an internet connection. This feature is particularly valuable in scenarios where on-site presence is limited or where multiple locations need to be monitored simultaneously.
Improved Safety and Security: SCADA and HMI systems incorporate security measures to protect against unauthorized access, data breaches, and cyber threats. Implementing secure communication protocols, user authentication, and access control mechanisms ensure the integrity and confidentiality of the system and its data. Safety features such as emergency shutdown protocols and fail-safe mechanisms can also be implemented to ensure the protection of personnel and assets.
In conclusion, SCADA and HMI systems play a critical role in monitoring and controlling industrial processes. They provide a centralized platform for real-time data acquisition, visualization, analysis, and control. With their intuitive interfaces, operators can efficiently monitor processes, identify issues, and make informed decisions. The integration of SCADA and HMI systems with other software applications and systems further enhances operational efficiency, productivity, and safety. As technology continues to advance, the future of SCADA and HMI systems holds promising possibilities for even greater automation, connectivity, and intelligence in industrial operations.