PLC vs. HMI: What's the difference between these two industrial automation technologies?
Introduction: The Differences Between PLC and HMI
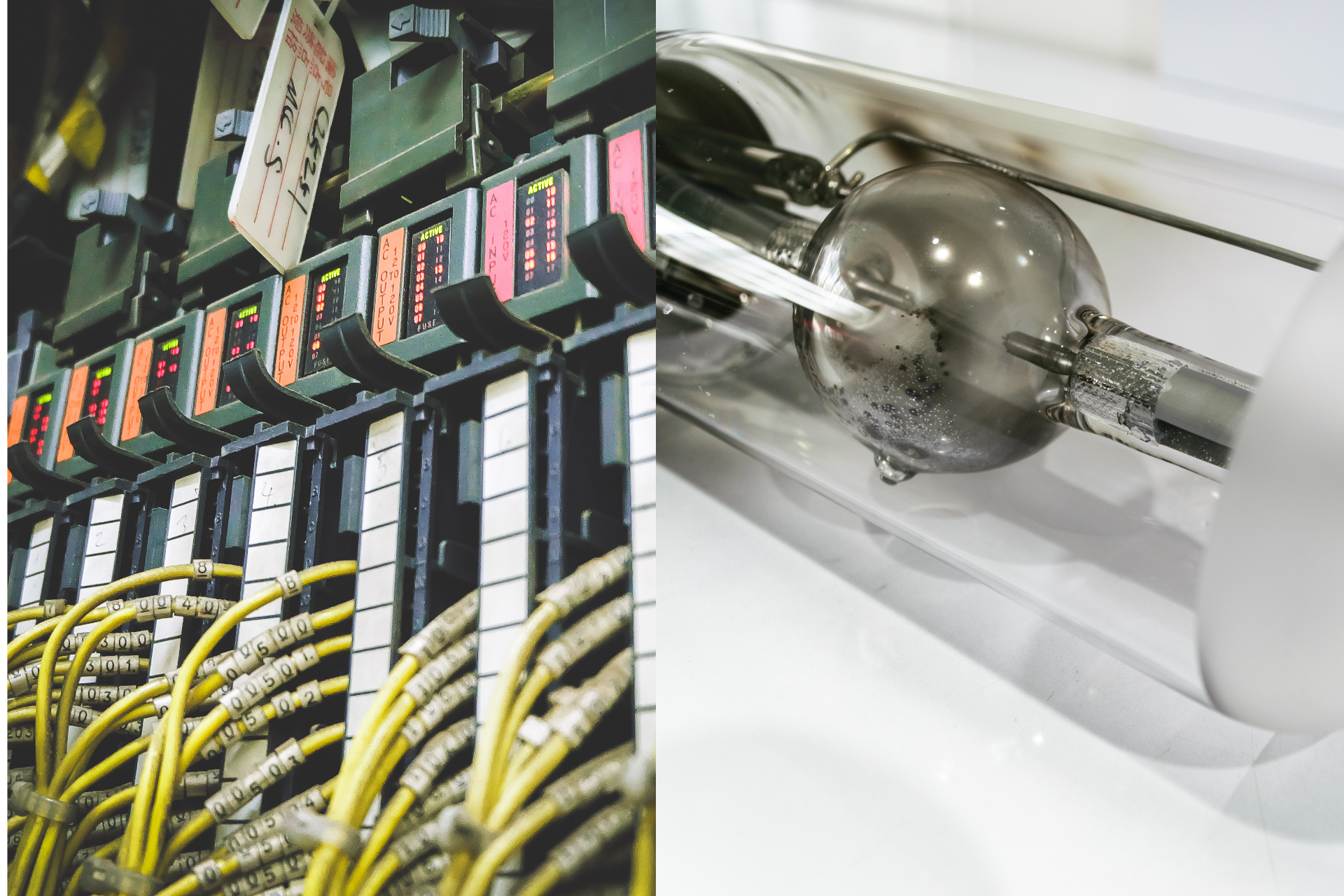
The differences between a PLC and an HMI are significant.
PLCs are the more traditional technology, and they are used to control equipment in the industrial setting. An HMI is a newer technology that is used for more of the human-machine interface.
An HMI is typically easier to use than a PLC because it has a graphical user interface that can be controlled with a mouse or touchscreen. This means that people without much knowledge of programming can still use a
SCADA and HMI System to control machinery. Learn more about
HMI SCADA.
PLCs, on the other hand, are designed for automation and control purposes and require more programming knowledge to operate effectively. They are often used to control complex industrial processes, such as assembly lines, manufacturing plants, and power generation systems. PLCs utilize a ladder logic programming language, which requires users to have a solid understanding of programming concepts and syntax.
One of the key differences between a PLC and an HMI is their primary function. While a PLC is responsible for executing control logic and managing inputs and outputs, an HMI focuses on providing a user-friendly interface for operators to interact with the system. The HMI system serves as a bridge between the user and the underlying PLC, enabling operators to monitor the process, view real-time data, and make necessary adjustments.
Another difference lies in their hardware components. PLCs are standalone devices that consist of a processor unit, input/output modules, and communication interfaces. They are built for rugged environments and have high reliability and durability. On the other hand, HMIs are typically software applications that run on a computer or dedicated hardware device. They rely on the processing power and storage capacity of the host device to provide the graphical interface and communication capabilities.
In terms of programming, PLCs require the use of ladder logic or other programming languages specific to the brand or model. This programming language is based on relay ladder logic and is used to define the control logic and behavior of the PLC. Programmers need to have a deep understanding of ladder logic and the specific programming software used by the PLC manufacturer.
HMIs, on the other hand, utilize software applications that offer a more visual and intuitive approach to programming. The software provides a range of tools and pre-built components that can be used to design screens, create graphical objects, and define user interactions. This makes it easier for operators with limited programming knowledge to create and customize the HMI interface to meet their specific needs.
When it comes to connectivity, both PLCs and HMIs are designed to communicate with various field devices and systems. PLCs typically support a wide range of communication protocols, such as Modbus, Profibus, or Ethernet/IP, to exchange data with sensors, actuators, and other devices. HMIs also support these protocols but primarily focus on communicating with the PLC or other control devices to retrieve data and issue commands.
Overall, the choice between a PLC and an HMI depends on the specific requirements of the industrial process. If the main objective is to automate and control complex machinery and processes, a PLC is the more suitable choice. It offers advanced programming capabilities and is designed to handle intricate control tasks.
On the other hand, if the emphasis is on providing a user-friendly interface for operators to monitor and interact with the system, an HMI is the preferred option. Its graphical interface, ease of use, and customization capabilities make it ideal for operators without extensive programming knowledge.
In many cases, a combination of both PLC and HMI systems is employed to achieve optimal control and monitoring in industrial settings. The PLC handles the control logic and manages the hardware components, while the HMI provides an intuitive interface for operators to visualize and interact with the process.
the choice between a PLC and an HMI depends on the complexity of the control tasks and the level of user interaction required in an industrial process, ultimately leading to efficient and optimized operations.
In conclusion, while both PLCs and HMIs play essential roles in industrial automation, they have distinct differences in terms of their functions, programming complexity, hardware components, and user interfaces. Understanding these differences is crucial for selecting the most appropriate system to meet the specific needs of an industrial process. Whether it's the robust control capabilities of a PLC or the user-friendly interface of an HMI, these technologies contribute to efficient and effective monitoring and control of industrial operations.