What Is SCADA and How It Works?
What Is SCADA and How It Works?
SCADA (Supervisory Control and Data Acquisition) is an absolutely essential system that empowers operators with the ability to monitor and control industrial processes remotely, ensuring maximum efficiency and productivity. With SCADA in place, operators have the power to oversee operations from a centralized location, enabling them to make informed decisions swiftly and effectively. This technology enables seamless integration of real-time data, providing operators with comprehensive insights into the status of industrial processes. It goes without saying that SCADA is a game-changer in terms of enhancing operational efficiency and streamlining workflows in industrial settings. The combination of both hardware and software components is an absolute powerhouse that seamlessly collaborates to gather, analyze, and present data in real-time. This harmonious blend ensures not only the collection of crucial information but also the efficient processing and visualization of the operational status of a diverse range of devices.
There are precisely three fundamental types of SCADA systems:
1. Distributed SCADA: Is an innovative and efficient system that revolutionizes the control and monitoring of various industrial processes. Unlike traditional systems, this advanced type of SCADA incorporates multiple remote terminal units (RTUs) or programmable logic controllers (PLCs) that are seamlessly connected to a highly centralized control unit. This ensures robust communication and enables real-time data acquisition, analysis, and decision-making capabilities across the entire network. By leveraging this distributed architecture, organizations can benefit from enhanced operational efficiency, improved reliability, and unparalleled scalability in their industrial operations. The central unit, with its unparalleled efficiency and precision, diligently collects a vast amount of data from the remote units. It does so with utmost accuracy and speed, ensuring that not a single piece of valuable information is missed. Equipped with this comprehensive dataset, the central unit is empowered to make informed decisions and take decisive control actions whenever necessary. Its ability to seamlessly process complex data streams and issue precise commands sets it apart as an indispensable powerhouse in any system.
2. Centralized SCADA: All the crucial data acquisition and control functions are efficiently executed from a single, strategically located central hub. This approach ensures streamlined operations, as every piece of vital information is consolidated and managed in one place. By concentrating these functions at a central location, organizations benefit from enhanced coordination, real-time monitoring, and seamless control over their systems. This centralized approach enables effective decision-making by providing a comprehensive view of the operations while promoting optimal efficiency and reliability. Remote devices assertively communicate with the central unit via robust and efficient communication networks. This seamless connectivity allows for smooth and uninterrupted data transfer, ensuring that crucial information is transmitted accurately and swiftly. The utilization of advanced communication technologies enhances the efficacy of remote devices, enabling them to seamlessly connect with the central unit for data exchange, control, and coordination purposes.
3.
Hierarchical SCADA: This approach reigns supreme. This robust system is designed with multiple levels or tiers, each one meticulously engineered to fulfill specific functions that contribute to the overall efficiency and effectiveness of the operation. By employing this well-structured framework, organizations can ensure seamless coordination, enhance control, and optimize data acquisition at every level of their SCADA infrastructure. The lower levels of the system confidently handle a wide range of field devices, ensuring seamless integration and efficient communication. On the other hand, the higher levels of the system possess the capability to perform complex data processing and management tasks with utmost precision and efficiency. By dividing responsibilities in this manner, the system ensures optimal performance and allows for effective decision-making at all levels.
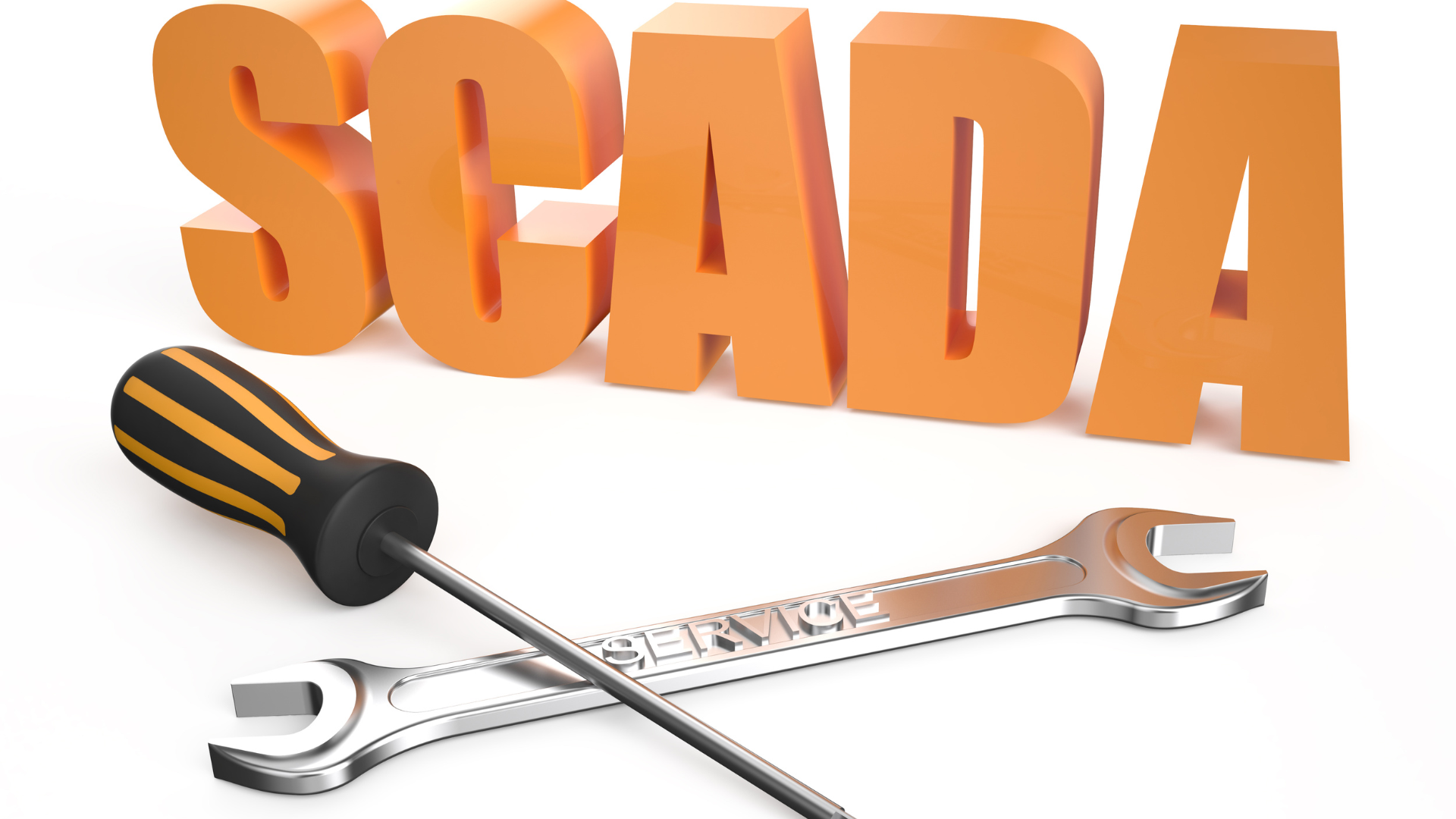
It is absolutely crucial to understand and acknowledge the fact that the Human-Machine Interface (HMI) and Programmable Logic Controller (PLC) are essential components of a SCADA system. However, it is important to emphasize that these two elements serve distinct and invaluable purposes in this complex system. While the HMI provides a user-friendly interface for operators to interact with and monitor the SCADA system, the PLC acts as the brain behind the scenes, responsible for controlling and automating various industrial processes. So, we must not underestimate or overlook the significance of both HMI and PLC in ensuring the smooth functioning and efficiency of a SCADA system. An HMI (Human-Machine Interface) serves as the crucial link between operators and the SCADA (Supervisory Control and Data Acquisition) system, facilitating seamless interaction. It empowers operators with a user-friendly interface that allows them to efficiently monitor and control various processes or machines. On the other hand, Programmable Logic Controllers (PLCs) take charge of specific processes or machines by executing control algorithms and ensuring precise control over critical operations. Together, these two indispensable components work in perfect harmony to optimize operational efficiency and ensure smooth system functionality.
A wide range of highly advanced Human-Machine Interfaces (HMIs) are readily available in the market, catering to diverse requirements and preferences. These cutting-edge interfaces include intuitive touchscreen panels, visually appealing graphical displays, and even innovative software-based interfaces that can be effortlessly accessed on both computers and mobile devices alike.
In a nutshell, a typical SCADA (Supervisory Control and Data Acquisition) system comprises three key components that work together harmoniously to ensure efficient monitoring and control. These components are crucial in maintaining optimal operational performance and enhancing productivity levels:
1. Remote Terminal Units (RTUs): Programmable Logic Controllers (PLCs), without a doubt, play an essential role in the field of data collection from sensors and actuators. These highly efficient devices are designed to seamlessly gather vital data from various points in the field, ensuring accurate and real-time monitoring. By harnessing their power, businesses can gain actionable insights and make informed decisions with confidence. With RTUs and PLCs at your disposal, you can effortlessly optimize processes, identify potential issues promptly, and maintain optimal operational efficiency across your entire system.
2. Communication Network: Plays a crucial role in seamlessly connecting the Remote Terminal Units (RTUs) and Programmable Logic Controllers (PLCs) with the central control unit for efficient and reliable data transmission. It ensures that critical information flows smoothly and without any disruptions, enabling real-time monitoring, control, and analysis. This network acts as the backbone of the entire system, facilitating seamless communication between different components and enabling swift decision-making processes. Its robustness guarantees that data is transmitted securely, accurately, and efficiently, making it an indispensable element in modern industrial operations.
3. Central Control Unit: This plays a crucial role in the efficient functioning of any system. This unit confidently receives valuable data from remote devices through a robust communication network. It then swiftly processes this data with precision and accuracy, enabling operators to have real-time monitoring and absolute control over operations. The Central Control Unit empowers operators with the tools they need to confidently manage and optimize system performance, ensuring seamless operations at all times.
If you're interested in expanding your knowledge about SCADA, PLCs, and HMIs, I highly recommend diving into specialized courses that delve into these topics with great detail. These courses offer comprehensive coverage on various aspects including programming techniques, configuration best practices, and troubleshooting methods. By enrolling in such courses, you will gain a deep understanding of these industrial automation technologies and equip yourself with invaluable skills essential for success in this field.