What Is the Difference Between PLC and HMI Programming?
What Is the Difference Between PLC and HMI Programming?
Programmable Logic Controllers (PLCs) and Human Machine Interfaces (HMIs) play a crucial role as integral components within a SCADA (Supervisory Control and Data Acquisition) system. PLCs are specialized computers designed to control industrial processes, utilizing a robust programming language specifically tailored for automation tasks. They serve as the brain of the system, executing programmed instructions and managing real-time data acquisition. On the other hand, HMIs provide the means for human operators to interact with the SCADA system. These user-friendly interfaces enable users to monitor and control various processes in real-time by presenting visual representations of data, such as graphs, charts, alarms, and status indicators. HMIs enhance operational efficiency by providing operators with valuable insights into process performance while also facilitating swift decision-making. When combined together within a SCADA framework, PLCs and HMIs create a powerful synergy that optimizes process control and monitoring capabilities. The PLC handles the automation aspect of the system by controlling devices and collecting data from various sensors. The HMI then visualizes this data in an intuitive manner, enabling operators to make informed decisions promptly. By leveraging these integrated technologies in SCADA systems across industries such as manufacturing, energy distribution, water treatment plants, and more; organizations can enhance productivity levels while ensuring safe and efficient operations. While they work together to control and monitor industrial processes, there are distinct differences between the two.
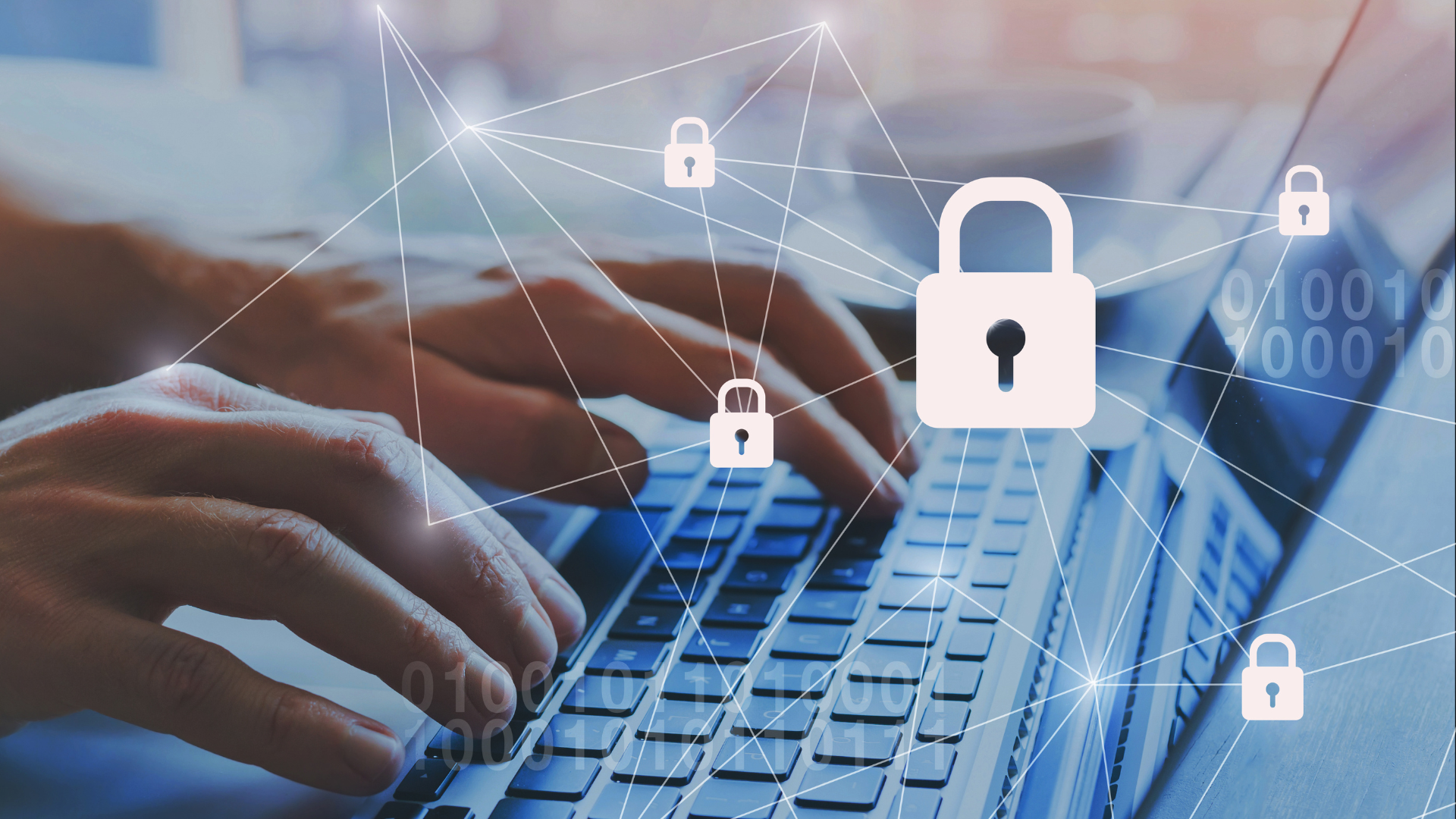
A Programmable Logic Controller (PLC) is an essential component in industrial automation that functions as a specialized computer. It is specifically designed to monitor and control machinery or processes in real-time, making it an invaluable tool in various industries such as manufacturing, energy, and transportation. PLCs are equipped with input and output modules that allow them to communicate with sensors, actuators, and other devices to gather data and execute control commands promptly. These intelligent devices provide real-time monitoring capabilities, enabling operators to effectively manage complex systems while ensuring optimal performance and safety at all times. It is programmed using ladder logic or other programming languages and is responsible for executing specific tasks based on input signals from sensors or other devices. PLCs are commonly used in automation systems to regulate variables such as temperature, pressure, and speed.
On the other hand, a Human-Machine Interface (HMI) plays a crucial role as the bridge between human operators and the complex industrial processes that are being controlled. The HMI serves as a user-friendly interface that allows operators to interact with and monitor various aspects of the industrial system. It provides a visual representation of real-time data, allowing operators to make informed decisions and adjustments based on the information presented. Additionally, HMIs often offer advanced features such as alarm systems, data logging, and remote access capabilities, further enhancing their functionality and usefulness in industrial settings. It provides a visual representation of data collected by the SCADA system, allowing operators to monitor and interact with the process. HMIs typically consist of touchscreens or graphical displays that present information in an intuitive manner.
SCADA (Supervisory Control and Data Acquisition) systems are vital in numerous industries for efficient monitoring and control of various processes. These systems are typically categorized into three main types: supervisory level, control level, and field level. The supervisory level SCADA system serves as the heart of the entire architecture, responsible for overseeing all connected devices and gathering data from the field. It acts as a central hub where operators can observe real-time data, make informed decisions, and analyze trends to optimize overall performance. At the control level, SCADA systems provide a more granular approach by managing individual components or subsystems within a larger process. This allows operators to have precise control over specific functions such as regulating temperature, pressure, or flow rates. The control level SCADA system ensures that each component operates within desired parameters to maintain efficiency and safety. Finally, at the field level, SCADA systems interact directly with physical devices on-site. This includes sensors, actuators, switches, or any other equipment that directly interfaces with the controlled process. Field-level SCADA systems play a critical role in collecting real-time data from these devices while also providing commands for remote operation or necessary adjustments. By incorporating these three tiers into SCADA systems, organizations can achieve comprehensive monitoring and control across their operations. This allows for seamless coordination between different levels of automation while ensuring optimal performance and productivity in industrial processes. The supervisory level handles data acquisition from various devices, while the control level manages the execution of commands sent by operators through HMIs. The field level comprises sensors, actuators, and other devices that directly interact with the physical process.
When it comes to programming Programmable Logic Controllers (PLCs), it is important to note that they require the use of specialized programming languages. These languages, such as ladder logic or structured text, are specifically designed for PLC programming and are essential for effectively controlling industrial processes. Ladder logic, which resembles electrical circuit diagrams, is commonly used for simpler control tasks while structured text offers a more traditional textual programming approach, often resembling high-level programming languages like C or Pascal. The choice of programming language depends on the complexity of the process being controlled and the preferences and expertise of the programmer. This programming focuses on defining inputs/outputs and creating logical sequences for controlling machinery. On the other hand, HMI programming involves designing graphical interfaces using software tools that allow operators to interact with the system visually.
To summarize, Programmable Logic Controllers (PLCs) play a crucial role in real-time control tasks by processing input signals received from sensors. They are responsible for executing logic-based instructions to ensure the smooth operation of industrial processes. On the other hand, Human Machine Interfaces (HMIs) serve as intuitive and user-friendly interfaces that allow operators to monitor and interact with these processes effectively. By employing visual representations such as graphical displays, charts, and diagrams, HMIs enable operators to comprehend complex data and make informed decisions promptly. Together, PLCs and HMIs form a powerful combination that optimizes industrial efficiency while enhancing operator productivity and safety. Both components are crucial in a SCADA system's overall functionality but serve different purposes within it.