Automatic Manufacturing: Transforming Production Processes
The industrial world is changing because many companies are using automatic manufacturing. Different types of automation, like flexible and programmable systems, change the manufacturing process. They make it more efficient and accurate. Industrial automation brings in tools such as robotic arms and automated machines. These help improve production lines and tackle issues like labor shortages and problems in the supply chain. This shift in technology helps businesses keep up with high production rates while ensuring better product quality and lower costs. Let’s look at how automatic manufacturing is changing industries.
Understanding Automatic Manufacturing
Automatic manufacturing is changing how businesses work in today's fast-paced economy. It mainly involves using advanced manufacturing systems to complete repetitive or complex jobs with little human help. With automation technology, manufacturers reach high levels of precision and efficiency in their production processes.
Its use includes flexible automation, programmable systems, and industrial robotics, which create chances for smoother workflows. This leads to better alignment with continuous improvement practices. As a result, the manufacturing process becomes more adaptable and competitive in different industries.
Definition and Core Concepts
Automatic manufacturing is a big step forward. It uses automation technology to be more accurate and efficient. This process automates tasks with programmable automation systems. This allows for batch production of different product types without needing constant manual changes.
Flexible automation is very important here. It helps industries adapt to changes in production needs. In the pharmaceutical industry, for example, it is crucial to quickly respond to different product formulas. Flexible systems allow for smooth workflows while meeting changing product demands.
Also, using advanced automated manufacturing systems, like industrial robots, reduces the risk of human error and keeps things precise. Robotic systems are often used for jobs like assembly and welding. They help keep processes running smoothly without losing quality. In summary, automatic manufacturing improves on traditional methods by offering innovation, scalability, and the latest technology to meet today's industry needs.
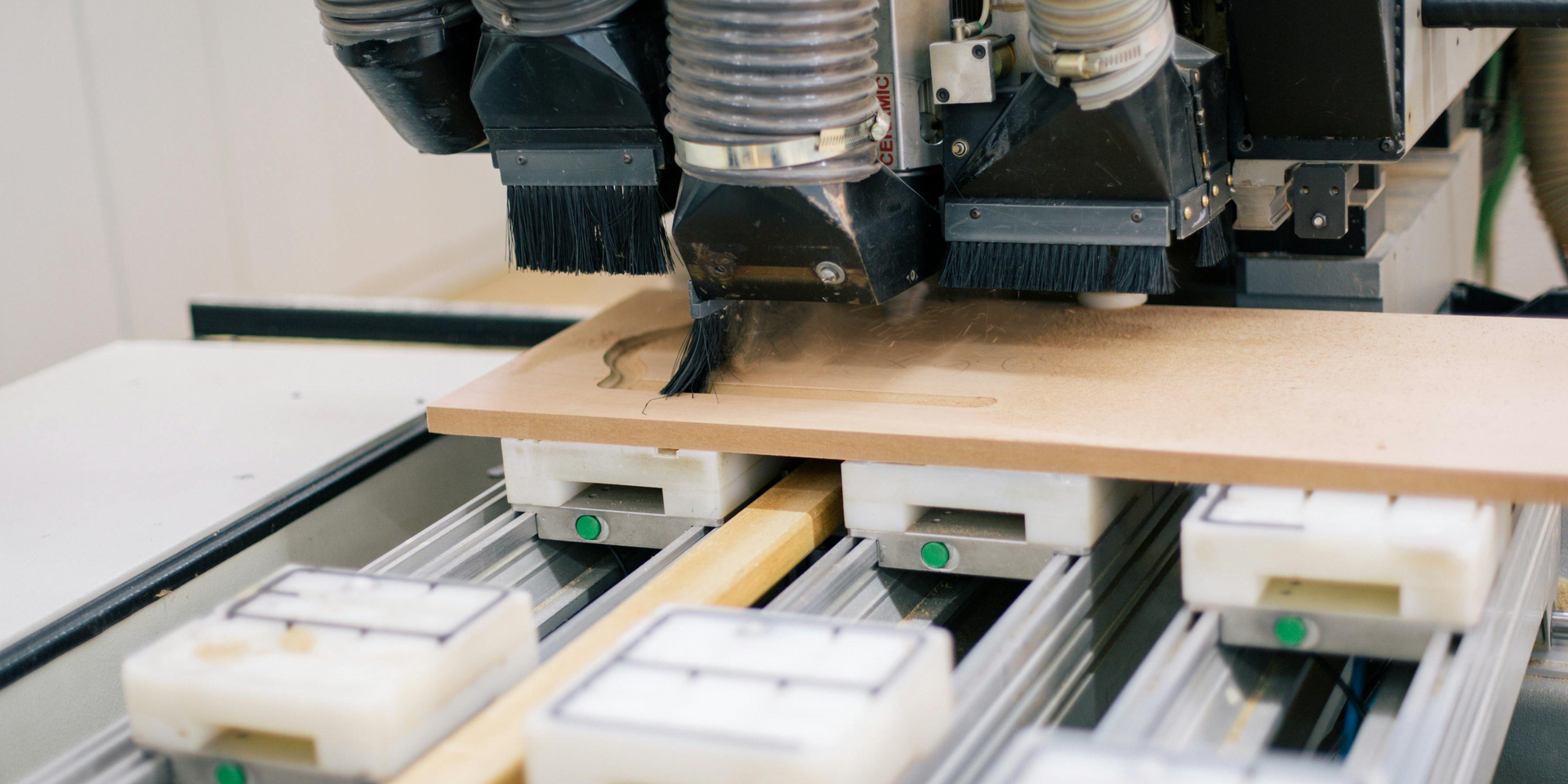
How Automatic Manufacturing Differs from Traditional Methods
The difference between automatic manufacturing and traditional methods starts with less human oversight. Traditional batch production relies on manual work. This leads to longer production times and inconsistent results. With automation, the production process runs smoothly, supported by control systems that focus on precision.
Automation also supports continuous improvement. This is different from traditional processes, which can get stuck without regular checks on performance. Using tools like robotic arms makes operations more efficient than manual assembly lines. This reduces mistakes and ensures good product quality.
Finally, automatic manufacturing uses data analytics to make decisions in real-time. Unlike traditional methods that grow slowly through small changes, automation technology encourages innovation and growth. The shift from manual work to automated systems changes how manufacturing works. It helps industries meet global demands easily and quickly.
Key Benefits of Adopting Automatic Manufacturing
Embracing automatic manufacturing offers many benefits for businesses. When companies use automation technology in their production processes, they can work more efficiently. This means faster production rates and lower operational costs. Robotic systems and automated assembly lines help complete tasks quickly while still keeping quality high.
Also, the risk of human error goes down a lot. This change leads to better precision in manufacturing systems. In addition to improving productivity, automation helps keep workers safe, especially in jobs that are high-risk. This shift in technology allows industries to stay innovative and competitive in the market.
Increased Efficiency and Productivity
Efficiency and productivity are important reasons why automatic manufacturing is appealing. Using automated systems like CNC machines and robotic arms changes the way things are made. These tools help finish repetitive and hard work faster than older methods.
One key point is the better production rates from automation technology. In sectors like automotive, robotic systems boost output while keeping quality high. This efficiency applies to batch quantities, so companies can easily respond to changing customer needs.
Also, automation improves workplace productivity. It allows human workers to focus on more complex or strategic jobs. Control systems help create smooth workflows, helping manufacturers stay ahead in a tough market. Automatic manufacturing is more than just making processes better. It marks a big move towards a more modern and productive industry.
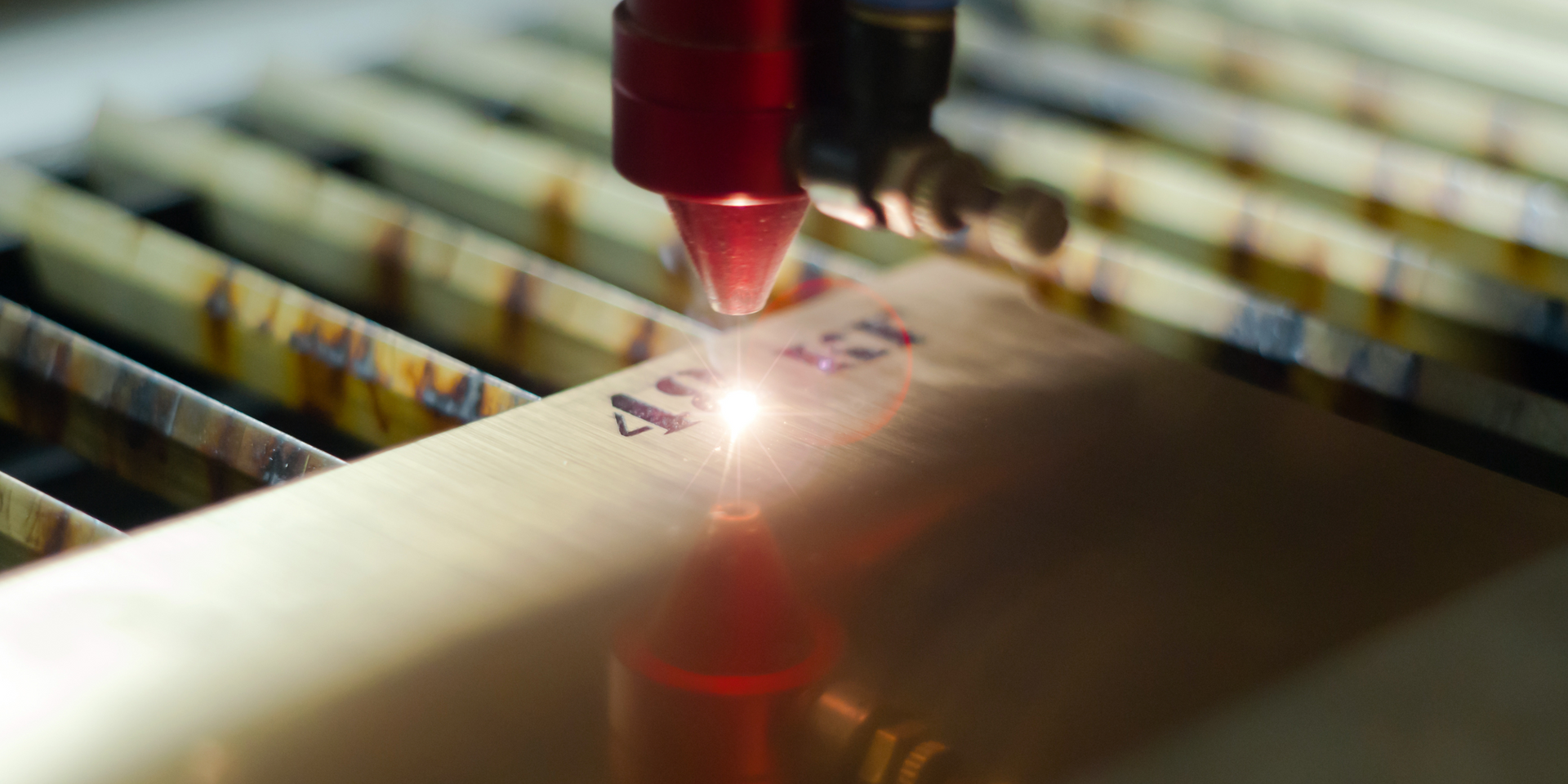
Enhanced Precision and Quality Control
Precision and quality control are key to the success of automatic manufacturing. Automated systems make processes smoother by reducing mistakes that happen in manual tasks. For instance, robotic systems in automated assembly work with great precision on repetitive jobs like welding or painting.
These systems help reduce the risk of human error, which improves product quality. Industries such as pharmaceuticals gain a lot from this. They use machine vision technology to keep strict quality standards in production. This helps them meet rules and ensure reliability.
Automation’s ability to carry out specific tasks in exact conditions also helps keep consistency in batch production. Control systems help maintain design specifications, leading to fewer defects and recalls. Better precision saves money and improves the industry's reputation for reliability and high product quality.
Beginner’s Guide to Starting with Automatic Manufacturing
Starting automatic manufacturing needs careful planning and good resources. Newcomers should look closely at their current manufacturing methods to find areas where they can improve. Important things to consider include how well the production line works, if it's cost-effective, and how easily it can adapt to changes in the market.
It's also key to choose automation technology that fits specific tasks, whether it is for assembly lines or inventory management. Training staff on how to use robotic systems will help make the change go smoothly. With these basics in place, businesses can achieve the great benefits of automated manufacturing systems.
Essential Equipment and Resources Needed
Starting with automatic manufacturing needs some important resources. First, it is vital to invest in production equipment like robotic arms and CNC machines. These tools can perform many tasks, from assembly lines to precise machining.
Next, businesses should have strong control systems and automation software to manage workflows well. For example, programmable logic controllers (PLCs) help with batch production while keeping operations flexible. Using resources designed for the manufacturing sector helps companies keep up with changing industry trends.
Companies should also focus on data analytics tools for real-time insights and ongoing growth. Spending money wisely on automation technology leads to better production speeds and quality. These key resources help build systems that make manufacturing processes more efficient and precise.
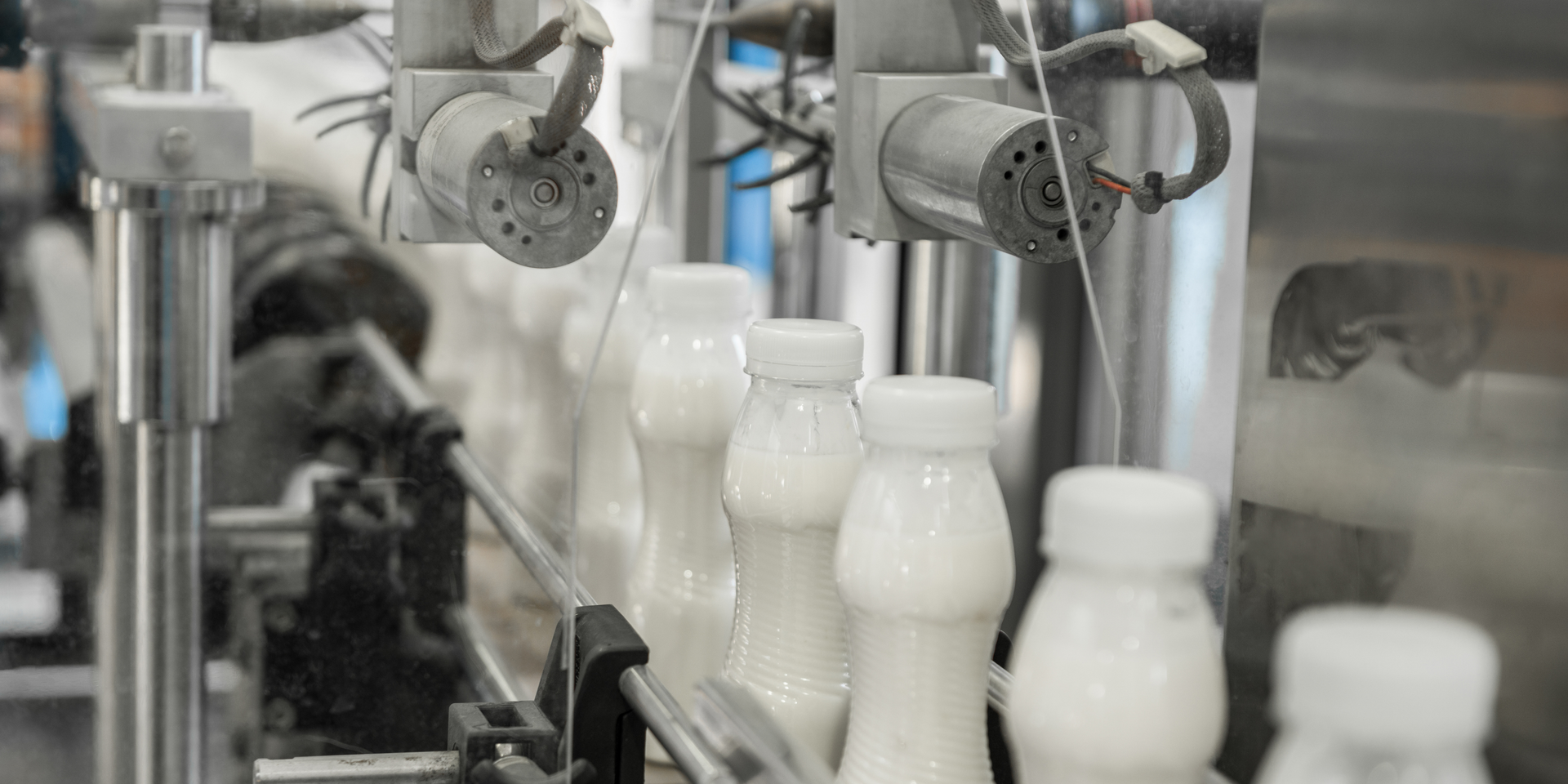
Step-by-step Guide to Implementing Automation
Transitioning to automation takes careful steps. This helps make sure everything goes well. Here’s what to do:
- Assess Current Processes: Look at the production line. Find areas that can be improved.
- Research Automation Opportunities: Use data to find which tasks can be automated.
- Select Technologies: Pick the right automation tools, like programmable systems or robots.
- Train Staff: Get human workers ready for the new systems.
- Monitor Implementation: Keep checking how well everything is working after it is set up.
By following these steps, manufacturers can improve their production line and product quality. This aligns their work with Industry 4.0 standards and boosts efficiency in different types of production.
Step 1: Assessing Your Current Manufacturing Processes
Before adding automation, businesses need to check their current processes for problems. A thorough review helps find the best areas to improve, like slow spots in the production line or tasks that are done repeatedly.
Using advanced tools and data analysis gives a clearer view of operational issues. For instance, looking at assembly workflows can show chances for higher production rates that match what automation can offer. This step is key in moving toward systems that can adapt to changing manufacturing needs.
By carefully reviewing their processes, manufacturers prepare for flexible automation. This helps them decrease cycle times or improve accuracy. This important step leads to long-term improvements in efficiency and reliability.
Step 2: Identifying Automation Opportunities
Identifying jobs that can be automated is important for using technology well. Tasks that often have human mistakes or are repeated, like stacking or labeling, are good choices for automation.
Data analytics play a big role here. By looking at real-time production data, manufacturers learn where automation can be most helpful. For example, certain tasks in assembly lines might be easier with robotic systems.
Making the change starts with knowing how automation can fix problems and improve flexibility. Businesses should use these insights to decide which jobs can improve production rates and product quality. This way, they can transition smoothly to modern manufacturing systems.
Step 3: Selecting the Right Automation Technology
Choosing the right automation technology helps meet manufacturing goals. Robotic systems, flexible automation tools, and programmable devices have various functions that fit different tasks.
For example, the automotive industry often uses robotic arms for assembly work. Precision and speed are very important in this area. CNC machines also provide high accuracy for complex production needs. They are a good example of advanced automation technology.
Manufacturers should consider their options carefully. They need to think about capacity, production style, and growth over time. Picking the right systems leads to better efficiency and supports continuous improvement in manufacturing processes.
Step 4: Training Staff and Integrating Systems
Comprehensive training helps make the switch to automated manufacturing easier. Human workers need to learn how to use control systems and robotic devices well. This cuts down on problems during setup.
Integration means matching new systems with current processes. This alignment keeps the production line running smoothly. It also boosts flexibility in the entire supply chain.
When training is prioritized, workers gain the skills to work well with automation technology. This relationship between human workers and systems keeps efficiency high. It also promotes innovation in manufacturing operations.
Conclusion
In conclusion, automatic manufacturing is more than just a trend. It can truly change how businesses work. This approach helps improve efficiency, accuracy, and productivity in production. By knowing its key principles and benefits, companies can lead in innovation. Start by looking at current practices and finding the right automation tools. Taking the right steps will help make the shift to automated systems easy. Embracing this change in manufacturing can lead to better quality control and a stronger competitive edge. If you want to see how automatic manufacturing can help your operations, think about contacting us for a consultation to talk about custom solutions for your business.
Frequently Asked Questions
What is the initial cost of setting up automatic manufacturing?
The starting cost to set up automatic manufacturing can be high. You often need to invest a lot of money. Expenses cover production equipment such as robotic arms, control systems, and software. With good financial planning, businesses in the manufacturing sector can manage this upfront cost well. This helps them gain long-term benefits.
How does automatic manufacturing impact employment?
Automatic manufacturing can change how jobs are done, but it does not take away job opportunities. Robotic systems usually do the repeated tasks. This lets human workers concentrate on more skilled jobs. As a result, job roles become bigger, and there is more chance for workers to learn new skills. This improves skills and makes the workforce stronger.
What is automatic manufacturing and how does it differ from traditional manufacturing?
Automatic manufacturing refers to the use of technology and machinery to automate production processes, reducing human intervention. Unlike traditional manufacturing, which relies heavily on manual labor, automatic manufacturing enhances efficiency, precision, and scalability, leading to faster production times and reduced operational costs, ultimately revolutionizing the manufacturing landscape.