Automatic Manufacturing
Key Benefits of Automation in Manufacturing
Automation in manufacturing has revolutionized the industry by bringing about significant benefits that enhance workflows and product quality. A key advantage of automation is the reduction in manual labor requirements, leading to increased production rates, reduced production time, and continuous process improvement. Robotic systems play a crucial role in maintaining precise production processes, ultimately minimizing human errors and ensuring consistency in output.
Furthermore, automation contributes to maintaining superior product quality and consistency through the utilization of advanced control systems. By reducing waste and enhancing efficiency, manufacturers can save costs and redirect their focus towards more intricate tasks. As industries evolve, the advantages of automation continue to drive improvements in operations and elevate customer satisfaction levels.
The integration of automation technologies not only streamlines manufacturing processes but also opens up opportunities for innovation and adaptation to changing market demands. By embracing automation, manufacturers can stay competitive, agile, and responsive to dynamic industry trends while delivering high-quality products efficiently.
Enhancing Production Efficiency and Speed
Automation revolutionizes the manufacturing process by enhancing speed and efficiency. The utilization of tools such as robotic arms and programmable logic controllers in production facilities leads to heightened production rates. These automated systems excel at executing repetitive tasks with precision, ensuring timely delivery of products without compromising on quality.
One notable advantage of flexible automation systems is their capacity for continuous improvement. They possess the ability to adapt to evolving production requirements and incorporate technological advancements seamlessly. By leveraging automation technology, companies can significantly reduce production timelines, enabling quicker product launches to meet market demands effectively.
Take, for instance, the integration of robotic systems in the automotive sector. Not only do these robots accelerate assembly lines, but they also streamline the process of assembling parts with remarkable efficiency. These enhancements result in increased production rates, streamlined workflows, and heightened overall productivity, providing businesses with a competitive edge in the market.
Automation's capability to expedite numerous tasks translates into improved production efficiency and sets new benchmarks for contemporary manufacturing practices. As these automated systems evolve further, they are poised to redefine industry standards and drive operational excellence across various sectors.
Improving Product Quality and Consistency
Automation plays a crucial role in enhancing product quality and maintaining consistent output levels across various industries. By implementing control systems in the manufacturing process, the likelihood of human error is significantly reduced, ensuring that all products adhere to the same high standards. Advanced technologies like Computer Numerical Control (CNC) machines excel in providing precision, especially for intricate designs, guaranteeing impeccable results consistently.
Manual labor often poses challenges for industries striving to maintain consistent quality. Automation resolves this issue by employing systems that strictly adhere to predefined specifications and protocols, resulting in enhanced consistency even during batch production runs or when producing diverse product variations.
The adoption of automation technology not only improves quality but also optimizes costs for manufacturers. An illustrative example is the use of automated inspection systems in pharmaceutical manufacturing, which play a vital role in verifying that products meet stringent quality benchmarks. Automation emerges as a necessity for instilling trust and dependability in manufacturing processes globally, underscoring its indispensable role in achieving excellence with every manufactured product.
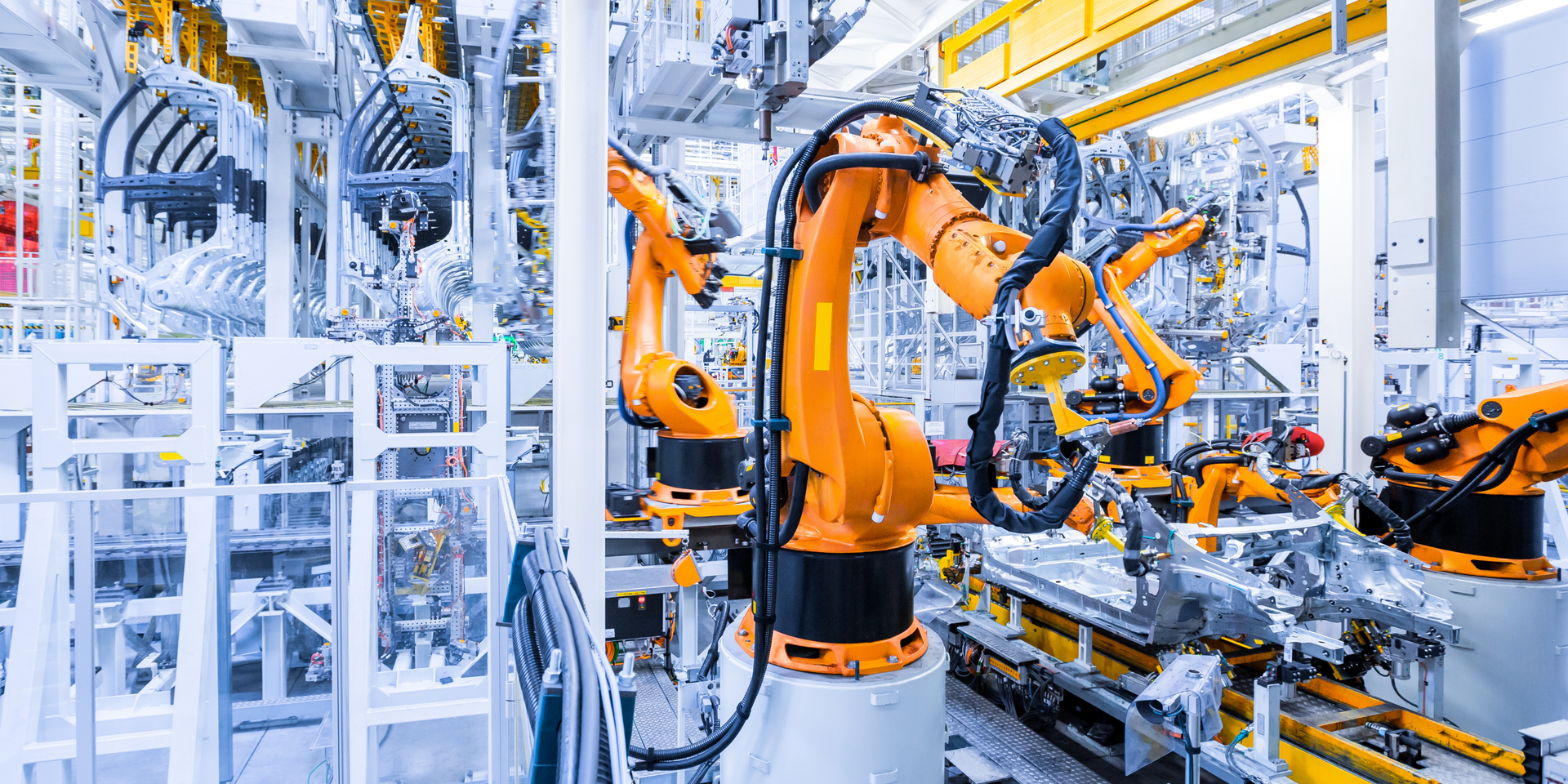
Core Challenges of Implementing Automation
While automation offers significant advantages, manufacturers encounter substantial challenges when implementing it. One major hurdle is the high initial investment costs, which can be particularly daunting for small to mid-sized manufacturing plants. Acquiring new production equipment and integrating automation technology demands substantial financial resources.
Another critical aspect is the necessity to cultivate a skilled workforce capable of operating these systems efficiently. Implementing comprehensive training programs becomes imperative to upskill employees and bridge any knowledge gaps they may have. These challenges underscore the importance of strategic planning and resource allocation in leveraging automation effectively.
Moreover, the transition to automation requires thorough analysis of existing processes, identification of optimal areas for automation implementation, and seamless integration with current operations. Manufacturers must also consider factors such as cybersecurity risks, maintenance requirements, and scalability to ensure a successful automation deployment. By addressing these challenges proactively and investing in both technology and human capital, manufacturers can unlock the full potential of automation in enhancing productivity and competitiveness in the industry.
High Initial Investment Costs
Implementing automation technology can indeed pose a significant initial financial investment for businesses, particularly smaller manufacturing plants. The costs associated with automation technology encompass the procurement of advanced equipment such as robotic arms, sensors, and production lines that seamlessly integrate with automation systems. Additional expenses may include installation costs and ensuring that all components function cohesively. It's worth noting that some manufacturing plants might need to undergo modifications to support automated systems, thereby contributing to the overall expenditure.
While the upfront costs of automation technology can be substantial, the long-term benefits in terms of enhanced efficiency and cost savings are undeniable. To navigate these initial expenses prudently, businesses should devise a comprehensive financial plan that encompasses not only the implementation phase but also the upkeep and potential upgrades of automation equipment.
Sustaining and enhancing automation equipment necessitates continuous financial commitment from manufacturers. Consequently, it is imperative for businesses to have a robust financial strategy in place to manage these ongoing costs effectively. Strategies like phased implementation or seeking grants for technological adoption can serve as viable solutions to mitigate financial obstacles associated with automation technology integration.
Despite the considerable initial investment required, companies transitioning to automation often discover that the enduring advantages far outweigh the associated costs, making it a strategically sound decision in the long run. By carefully managing expenses and leveraging available resources, businesses can unlock the full potential of automation technology to drive operational efficiency and competitiveness within their industry.
Need for Skilled Workforce and Training
Finding skilled workers who can effectively manage new automation systems poses a significant challenge for manufacturing plants. These facilities require employees who are proficient in working with robotic systems, operating industrial robots, and troubleshooting programmable logic controllers.
To address this issue, customized training programs play a crucial role in cultivating a workforce with the necessary skills. These programs provide hands-on experience with automation technology, enabling employees to adapt smoothly to the evolving industrial landscape. In the absence of proper training initiatives, companies may encounter operational difficulties and run the risk of damaging their costly production equipment.
Continuous learning is essential for workforce development, particularly in light of advancing technologies. As manufacturing processes undergo transformations, it is imperative for employers to invest in upskilling their teams to keep pace with industry innovations. This involves bridging traditional production methods with state-of-the-art manufacturing systems. By prioritizing comprehensive training for their workforce, businesses empower employees to leverage automation effectively, thereby ensuring seamless operations and facilitating transitions in contemporary production environments.
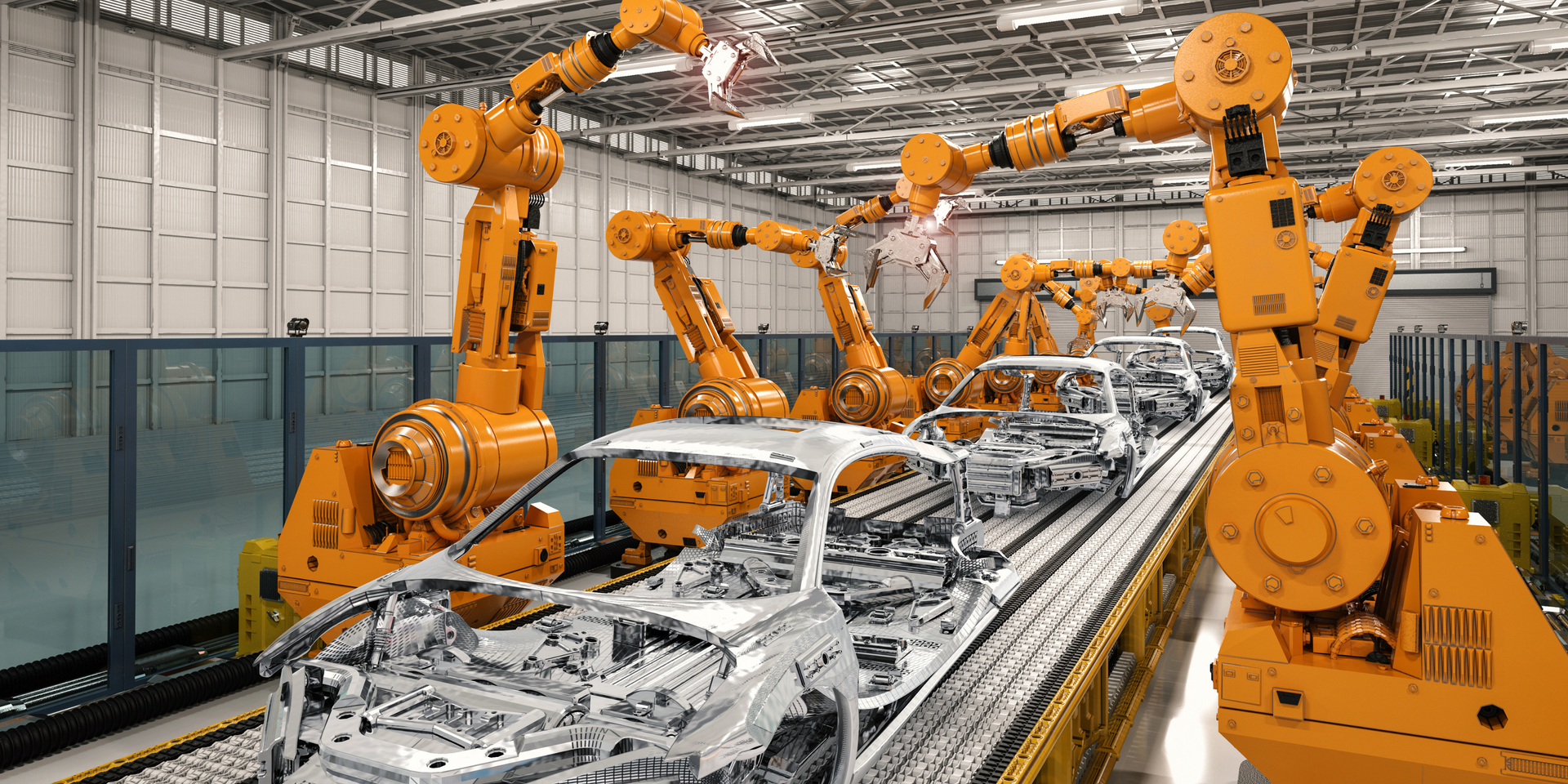
Technological Advances in Automated Manufacturing
Automation has emerged as a game-changer in the realm of manufacturing, with notable advancements in technologies like artificial intelligence and the Internet of Things (IoT) spearheading a drive towards heightened operational efficiency. By incorporating real-time data and machine learning into automated systems, manufacturing facilities are experiencing a continuous enhancement in their processes. These technological innovations not only optimize production procedures but also fortify supply chain management and facilitate greater flexibility in product customization.
The ongoing technological evolution within the manufacturing sector promises enhancements in precision, scalability, and responsiveness, propelling an era that challenges conventional practices for the better. As automation continues to evolve, we anticipate witnessing even more profound transformations in how goods are manufactured and distributed to end consumers.
Furthermore, the integration of automation technologies such as robotics and autonomous vehicles is streamlining logistical operations within manufacturing facilities. These advancements not only enhance productivity but also ensure safer working environments for employees by delegating hazardous tasks to automated systems. The shift towards smart factories equipped with interconnected devices and sensors allows for predictive maintenance, reducing downtime and optimizing overall equipment effectiveness.
In conclusion, the amalgamation of cutting-edge technologies into manufacturing processes signifies a paradigm shift towards increased productivity, cost-efficiency, and adaptability. As businesses embrace automation to stay competitive in today's market landscape, we can anticipate a future where innovation continues to revolutionize the industry on an unprecedented scale.
Role of Artificial Intelligence and Machine Learning
Artificial intelligence (AI) and machine learning are revolutionizing the operations of factories worldwide. By harnessing these advanced technologies, production lines are becoming increasingly efficient. This is achieved through the application of predictive analytics and intelligent algorithms, enabling informed decision-making based on data-driven insights.
The implementation of AI in manufacturing plays a crucial role in identifying process inefficiencies and suggesting solutions for optimization. On the other hand, machine learning contributes to tasks such as quality control inspections and inventory management, streamlining these processes with precision and accuracy. When integrated seamlessly, these tools empower companies to enhance their operations continuously and swiftly adapt to evolving product demands.
A prime illustration of this transformative impact can be observed in General Motors' utilization of AI to streamline their supply chain operations effectively. By leveraging AI capabilities, General Motors has achieved operational excellence by accurately predicting market trends and refining workflows to drive cost efficiencies. As more manufacturers embrace AI and machine learning technologies, a paradigm shift is unfolding across industries, setting new benchmarks for intelligent and agile production practices.
Integration of the Internet of Things (IoT)
The integration of IoT (Internet of Things) in automated manufacturing processes has revolutionized productivity levels within the industry. By enabling seamless communication between machines, sensors, and control systems in real time, IoT facilitates enhanced monitoring and management of manufacturing operations. This interconnected network not only reduces the likelihood of human errors but also contributes to heightened production efficiency.
One of the key advantages of IoT in manufacturing is its support for predictive maintenance. Through continuous data analysis, industrial robots and equipment can be maintained proactively, minimizing downtime and optimizing operational continuity. As a result, manufacturers are able to streamline their processes, enhance efficiency, and swiftly adapt to fluctuations in demand across their supply chain.
Moreover, the implementation of IoT technology opens up avenues for advanced analytics and machine learning applications. By harnessing data insights generated by connected devices, manufacturers can make informed decisions, identify optimization opportunities, and drive continuous improvement initiatives. This data-driven approach empowers businesses to stay competitive in dynamic market environments and meet evolving consumer expectations effectively.
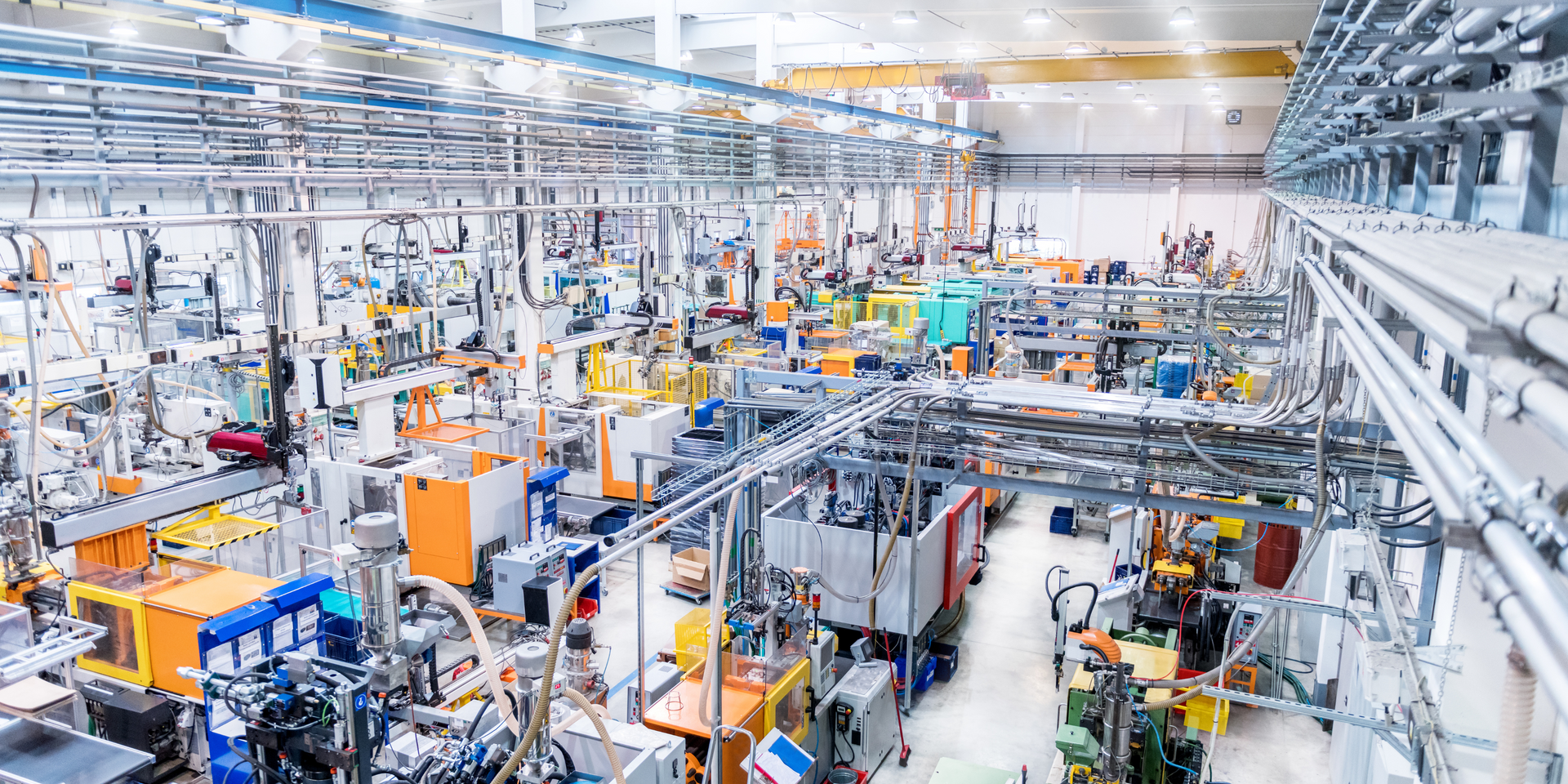
Impact of Automation on Workforce Dynamics
Automation is revolutionizing work processes across various industries, reshaping traditional job roles while also creating new opportunities in technology and engineering sectors. The impact of automation on job roles is evident, with a growing demand for skills in programming, maintenance of robotic systems, and troubleshooting IoT devices. As automation continues to advance, individuals are presented with the opportunity to acquire new skills, enabling them to transition into emerging roles that will drive the future of the manufacturing sector.
The evolution of automation has not only transformed job requirements but has also emphasized the importance of adaptability and continuous learning in the workforce. Embracing automation opens avenues for upskilling and reskilling, allowing individuals to stay relevant in an increasingly automated landscape. By acquiring proficiency in areas such as data analysis, artificial intelligence integration, and cybersecurity, workers can position themselves for success in the evolving industrial environment.
Furthermore, the integration of automation technologies has led to enhanced efficiency and productivity in manufacturing processes. Automation streamlines operations, minimizes errors, and accelerates production timelines, leading to cost savings and improved competitiveness for businesses. By leveraging automation tools effectively, organizations can optimize resource utilization, drive innovation, and deliver high-quality products to meet evolving consumer demands.
In conclusion, while automation undeniably alters job landscapes by phasing out certain roles, it simultaneously paves the way for skill diversification and career advancement. Embracing automation not only enhances operational capabilities but also fosters a culture of lifelong learning and professional growth within the workforce. By adapting to the changing demands of automated industries, individuals can seize opportunities for career development and contribute to driving innovation and progress in their respective fields.
Job Creation in Technical and Engineering Fields
Automation in manufacturing has not only transformed production processes but has also opened up new avenues for job opportunities in technical and engineering fields. The incorporation of advanced machinery and robotic systems demands skilled individuals who can design, operate, and maintain these technologies effectively.
For manufacturing plants transitioning to automation, it is essential to implement training programs that enhance the skills of their workforce to keep pace with technological advancements. Companies that deploy industrial robotics often look for engineers who are adept at managing complex systems. Providing employees with proficiency in areas like machine learning and data analytics can streamline production processes.
This shift towards automation allows professionals to take on more specialized technical roles, leading to increased efficiency in production speed and product quality. By investing in ongoing training for their employees, businesses can harness automation to create innovative job prospects and foster a sustainable industry that relies on specialized expertise.
Moreover, the integration of automation technology not only boosts productivity but also improves workplace safety by assigning hazardous tasks to machines instead of human workers. This results in a safer work environment and reduces the risk of accidents or injuries.
In conclusion, embracing automation in manufacturing not only enhances operational efficiency but also elevates job standards by emphasizing specialized skills and knowledge. It is crucial for businesses to adapt to this technological shift and invest in upskilling their workforce to thrive in an automated future.
Shifts in Labor Requirements and Roles
Automation has revolutionized the workforce, shifting the demand from traditional labor-intensive roles to more technologically advanced positions. As automation takes over tasks that once required physical exertion, there is a growing necessity for workers to acquire new skills to remain relevant in the evolving job market.
The advent of modern manufacturing systems has given rise to job roles such as IoT specialists, control system engineers, and data analysts. Employees are now expected to adapt to roles that involve overseeing machines and interpreting complex data sets. Through continuous training and upskilling initiatives, workers can equip themselves with the necessary competencies to thrive in this changing landscape.
While industries leveraging automation may experience reduced labor costs, they also witness an expansion in job opportunities within specialized domains. This transition underscores the importance of workforce adaptation, as it paves the way for the emergence of novel roles aligned with technological advancements. By embracing these changes, both employees and organizations can effectively navigate and excel in a contemporary automated manufacturing environment.
Conclusion
Automating manufacturing processes presents a myriad of opportunities and obstacles for industries to consider. The benefits, including enhanced production efficiency and elevated product quality, serve as compelling reasons for businesses to explore automation. Nevertheless, challenges such as the initial high costs of implementation and the requirement for skilled personnel are equally significant factors to take into account.
As technology continues to advance with the integration of artificial intelligence (AI) and the Internet of Things (IoT), manufacturers must address these challenges effectively to unlock the full potential of automation in their operations. Making investments in training programs and adapting the workforce to embrace automation will be crucial steps towards a successful transition.
Embracing automation in manufacturing requires a strategic approach that considers not just the technological aspects but also the human element within the workforce. By proactively addressing these challenges, industries can position themselves for greater success in an increasingly automated landscape. If you are considering integrating automation into your manufacturing processes, we invite you to reach out to us for expert guidance and consultation tailored to your specific needs.