Understanding the Basics of Automatic Manufacturing
Understanding the Basics of Automatic Manufacturing
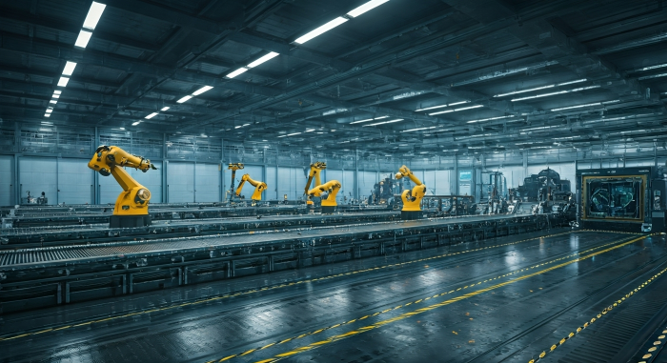
Key Highlights
- Automatic manufacturing uses advanced automation technology to make the manufacturing process smoother with very little human intervention.
- There are three main types of automation: fixed, programmable, and flexible. Each one has its own best use in the modern manufacturing world.
- Leading technologies in use include industrial robots, programmable logic controllers (PLCs), and the Internet of Things (IIoT). These tools help the whole process run well.
- Some of the biggest benefits are better efficiency, lower labor costs, steady product quality, and quick changes to match market needs.
- Many industries, like automotive, consumer electronics, and renewable energy, count on automated systems. They need these for a strong edge over others and to keep making things better all the time.
- New ideas like artificial intelligence and IoT have changed the way the manufacturing process works. These bring much higher productivity and help industries be part of the growing digital transformation.
Introduction
Automation is changing the way the manufacturing process works. It does this by adding industrial automation and control systems to new production lines. With the use of these systems, manufacturers can get better work done with fewer mistakes. They can also keep up with changes in what people need. This move is now at the center of industrial growth. It helps make many manufacturing systems better. If you want your business to do well in a world that is always chasing new technology, you have to know how automatic manufacturing works. In the next parts, we will talk about the most important things you need to know about this changing industry.
The Complete Guide to Automatic Manufacturing System
What is Automatic Manufacturing?
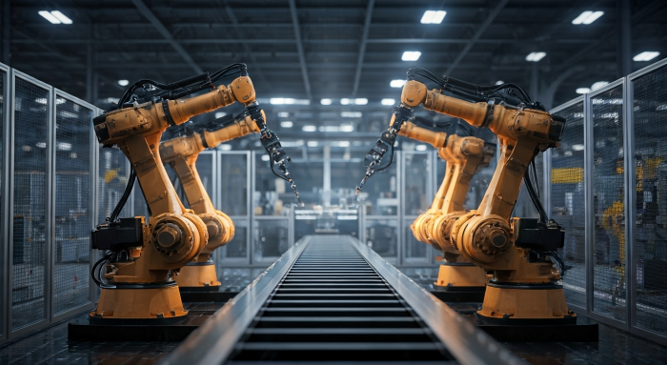
Automatic manufacturing means using automation technology to run machines and do production work with very little help from people. The goal is to make things flow better and make sure each item is made the right way. It also helps companies make more products quickly.
When companies use robotics and control systems, they do not need people to do the same work again and again. This helps to cut down on human error. It also makes the work faster and smoother. In the end, you get a reliable manufacturing system that can handle more orders as they come in. Now, let’s look at the main ideas behind automatic manufacturing.
Definition and Core Concepts
Automatic manufacturing uses automated manufacturing systems. These use networks of machines and control systems to run the production process with as little human intervention as possible. This way of making things is based on getting work done faster, making each thing the same, and being sure the process will work every time.
At the heart of this idea is moving from manual processes to automation technology. It lets machines do repeated work with fewer mistakes. These automated systems are good at checking performance and giving the same results each time. They do not get tired like people do. For example, conveyor machines can move materials without people needing to help, so there are no slowdowns you would get with manual operations.
Control systems are very important. These systems connect machine tools, sensors, and robotic arms so they all work together. Using these systems, everything from moving raw materials to putting finished products together can be automated. This makes the workflow smooth and ready to change fast if needed. Automatic manufacturing is now a well-coordinated and improved way to meet today’s production needs.
Key Components of Automatic Manufacturing Systems
An automated manufacturing system uses a group of connected parts that work well together to help companies make products faster and more accurately. The different parts keep the production line running smoothly:
- Machine Tools: These are needed to cut, shape, and put together materials.
- Control Systems: These help things run at their best and keep everything organized.
- Robotic Arms: These give more accuracy when putting parts together or moving materials.
- Programmable Logic Controllers (PLCs): These be like the 'brain' that helps the automated manufacturing system run the steps in the right order.
- Sensors and Actuators: These give quick feedback, so work can be more correct.
All these things together help lower the need for a lot of people doing the work by hand, but still keep everyone safe and the work good. For example, when sensors find something wrong very fast, the system can fix it quickly and not stop the production line. Control systems with PLCs help set and keep the right speed of the whole manufacturing system to make sure everything looks and works the same, and also helps make more products in less time.
Evolution of Manufacturing: From Manual to Automated
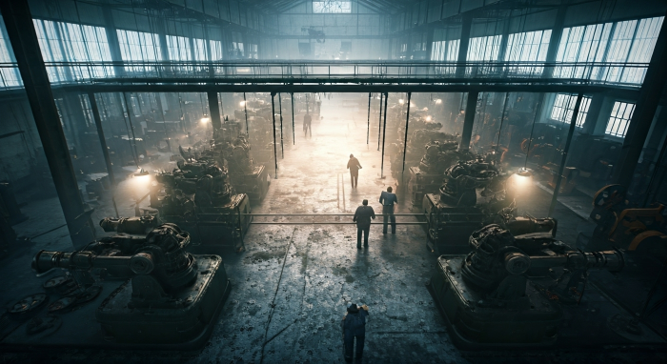
move from old ways of making things to using machines marks a big step for how industries grow. In the past, most jobs were done by hand. This meant needing workers with special skills, and it often led to different results each time.
But now, digital transformation has changed the way we see production. Automated manufacturing brings precision, steady results, and gives companies the chance to grow faster. This makes it easier for them to keep up with others. In the next sections, we will talk about where manual processes started and look at some big moments in automation history.
Traditional Manufacturing Methods
Traditional manufacturing used manual processes, where people had to work machines by hand and do many hard tasks themselves. This way of working gave some room for making things how people wanted, but it often made the production line slow and pushed labor costs up.
Mistakes by people, called human error, made quality worse and changed what came out of the production line each time. Delays happened often. There were also times when there were not enough workers. These problems held the work back and made it hard for manufacturing plants to grow.
Still, these old methods helped get things going for better manufacturing systems later. As time went on and new things were invented, industries wanted to use automation to deal with the problems from using so much labor on the production line.
Major Milestones in Automation History
The story of automation shows big changes that have shaped the world we see today. In the early days, big steps like moving belts and transfer lines played a big role. These systems were used a lot by General Motors in the middle of the last century.
Now, the Fourth Industrial Revolution is here. This new age uses smart tools, like AI, and people use computers more than ever. Manufacturers use these advances to make things in new ways. They also help people save money, make more, and see more economic growth.
Milestone | Era | Impact |
---|---|---|
Assembly Line (Ford) | Early 1900s | Mass production, lower costs |
Transfer Lines (GM) | 1950s | Faster and more reliable production |
CNC Machines | 1970s | Precision-based flexibility |
Industrial Robots | 1980s | Enhanced safety, reduced waste |
IIoT & AI Integration | 2000s-present | Real-time data, ongoing evolution |
Essential Types of Automatic Manufacturing Systems
Automatic manufacturing systems use different types of automation. Each one works best in some production situations. It’s important to know these types so you can choose the right option for your factory’s needs.
Fixed, programmable, and flexible automation all have their own good points. Fixed setups are best for making many of the same thing. Programmable systems can be changed for different product batches. Flexible automation lets you change quickly when demand goes up or down. Next, we’ll take a closer look at these types of automation.
Fixed (Hard) Automation
Fixed automation, also called hard automation, is a type of automation made for high-volume work. It needs little human intervention. You often see this in manufacturing plants where the same product is made in large batches. Assembly lines in the automotive industry are one good example of this system. Here, it helps to get the same output each time and keeps product quality high.
This setup uses machine tools and transfer lines that are made for one job. With this, companies can cut labor costs and make products faster. But a high initial investment in the system can hold some groups back if they want to use this type of automation.
Programmable Automation
Programmable automation is set up to handle batch production. In this, you make certain programs or steps to produce different product groups. Programmable logic controllers (PLCs) help to make changing tasks easier and smoother.
These systems give you more flexibility and can deal with many kinds of manufacturing jobs. You do not need to pay the high costs that come with fixed types of automation. For example, you can reprogram the system quickly. This means you can change batch sizes or even the features of a product when needed. That is why programmable automation works well if market needs change a lot.
While it is more flexible than fixed setups, there is still some time needed when you switch from one job to another. This limits how fast you can shift, which means programmable automation is best for when you need some, but not complete, flexibility.
Flexible (Soft) Automation
Adaptability is what makes flexible automation work well. It helps manufacturing systems answer changing production needs in a good and easy way. This type of automation uses things like programmable logic controllers and industrial robots. They help workers change the assembly process fast and with very little downtime. This is very useful in batch production, where you need to make different products. When you use better control systems and data analytics, you get more production speed and stop more mistakes because of human error. Being able to answer quickly to what is needed helps companies get better over time and makes the whole supply chain management stronger. Continuous improvement is another big plus, which helps the supply chain get even better with time.
Technologies Powering Automatic Manufacturing
Modern manufacturing gets its power from new automation technology. Using things like industrial robots, artificial intelligence, and computer systems, the way businesses work is changing.
When people use these technologies, they get better control, can grow their work, and they make fewer mistakes. Let’s take a look at some big changes that are now the base of modern manufacturing.
Robotics and Machine Vision
Industrial robots and machine vision systems are key parts of modern manufacturing. Robotic arms can move in many ways to do things like welding or handling materials. They do this with less risk to people.
Machine vision uses sensors and cameras. It keeps an eye on things like how parts line up and how good the products are. The real-time feedback helps fix mistakes right away. This helps make every item look and work the same on the line.
These technologies work together. They help companies get things done faster and help cut down on mistakes. These tools are a big part of what makes modern manufacturing work well.
Industrial Internet of Things (IIoT)
The integration of the Industrial Internet of Things (IIoT) makes the manufacturing process much better. When you connect things like industrial robots, machine tools, and other systems in manufacturing plants to the internet, you get real-time data analytics. This means you can react faster in your factory and solve problems right away.
This kind of connection helps with predictive maintenance. You can fix things before they break down. It also helps use less energy and lowers the risk of human error. Because of all this, supply chain management gets better. This brings more efficiency and new ideas into manufacturing plants. The use of the internet of things supports digital transformation and is good for economic growth. It helps the whole manufacturing process move forward and reach those big goals.
Computer Numerical Control (CNC) Machines
CNC machines change the manufacturing process by using computers to run machine tools with great accuracy. This type of automation helps the machines do the same job again and again without mistakes. There is less need for people to step in, so there are fewer errors. By bringing together new machining skills with programmable logic controllers, these machines increase production speed and keep up good product quality at the same time. CNC technology makes the assembly process simple and supports various manufacturing processes. This lets industries like automotive and aerospace meet their changing needs in a better way.
Benefits of Implementing Automatic Manufacturing
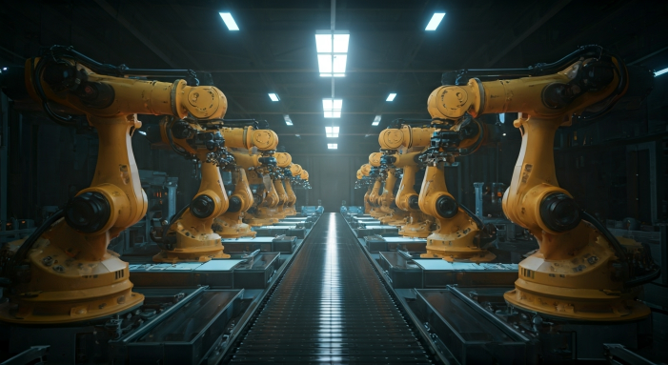
When you start using automatic manufacturing, it helps boost productivity. This happens because the assembly process gets smoother. There are fewer workers needed, so labor costs go down. Since there is less human intervention, the risk of human error is lower, and you get better product quality that stays the same every time. Many companies find that they save money fast and get their money back more quickly when they bring in automation. Using data analytics alongside these tools makes it easier for them to adapt and work well. In the end, it puts them in a better spot for economic growth as they keep up with other businesses.
Increased Efficiency and Productivity
Bringing automatic manufacturing into various manufacturing processes helps raise how well and how much you get done at work. By using industrial robots and programmable automation, production lines can cut down on labor costs and reduce human error. This shift means operations run smoother, so things move faster, and there is more consistency in what gets made. Also, when you use control systems, you can keep an eye on what is happening in real-time and study data for the assembly process. This lets you find new ways for continuous improvement and make things better over time. In the end, these changes help companies meet market needs better and use their resources in the best way possible.
Improved Product Quality and Consistency
Boosting product quality and making sure things stay the same every time is one big benefit of using automatic manufacturing systems. When you add good control systems and robotic arms, you cut down on human intervention. That means there is less risk of mistakes, and what comes off the production line is much more even.
With programmable automation, you can make real-time changes to keep up the right standards. This helps make sure that what gets made is always of good product quality. When there is less difference in what comes out, people like what they get more. This helps the brand look better, too. Right now, with so much competition out there, it’s important for businesses to use change like this if they want to do well.
Cost Reduction and Return on Investment
Using automatic manufacturing systems can help lower labor costs that come with manual processes. At first, these systems may need a big investment. But over time, you can save a lot of money because there will be less human intervention and less risk of human error.
They also make production speed go up, and things run more smoothly. This means your return on investment comes faster. Manufacturing plants can use their resources better, too.
When you use this kind of system, it helps with continuous improvement and makes sure that resources are used well. In the end, it not only helps the automotive industry, but it also supports economic growth in other areas.
Conclusion
Embracing automatic manufacturing is very important for any group that wants to stay ahead in today's tough market. When businesses cut out human error and improve process automation, they see big boosts in how well and how fast they work. Bringing in new tools, like the industrial internet of things and artificial intelligence, helps build smarter systems. These systems let you be quicker and react faster to changes. As the world moves forward, using more automation is not just a good idea. It is needed to keep the economy growing and to do well in the fourth industrial revolution.
Frequently Asked Questions
What industries benefit most from automatic manufacturing?
Automatic manufacturing helps many industries, like automotive, electronics, and consumer goods. These areas use automation to make the production process smoother. It helps them have more accuracy when they make things. It also lowers the cost to run everything. Because of this, they can do their jobs better and stay ahead of others in the market.
How does automation impact workforce requirements?
Automation changes what the workforce needs. It cuts down on the need for people who do hands-on jobs. At the same time, it makes it important to have skilled workers who can run and look after automated systems. Because of this, there is a big need for training and learning new skills. To work with these new technologies in manufacturing, people have to be ready to learn and change.
What are the main challenges in adopting automatic manufacturing?
High starting costs can get in the way of bringing in automatic manufacturing. The technology can also be hard to add to the current setup. Training the people who work there is needed. Some in the company may not want to change what they do. Plus, the cost to keep gear running is always there. On top of that, there is the need to keep the computer systems safe from threats online. Companies have to handle all of this if they want to make it work.
Is automatic manufacturing suitable for small businesses?
Automatic manufacturing can work well for small businesses. It helps make the work faster and better. You will need to look at the starting cost, how much you want to make, and the needs of your business. These things will tell you if it is a good idea. If you do it right, it can help your business grow and improve your product quality.
How does automatic manufacturing contribute to sustainability?
Automatic manufacturing helps make things more sustainable. It uses resources better, makes less waste, and cuts down on energy consumption. When you make things run smoother and use new tech like IIoT, it’s possible for manufacturers to create high-quality products with less harm to the environment. This can help to build a more sustainable way of working for everyone