Mastering Automatic Production for Maximum Efficiency
Mastering Automatic Production for Maximum Efficiency
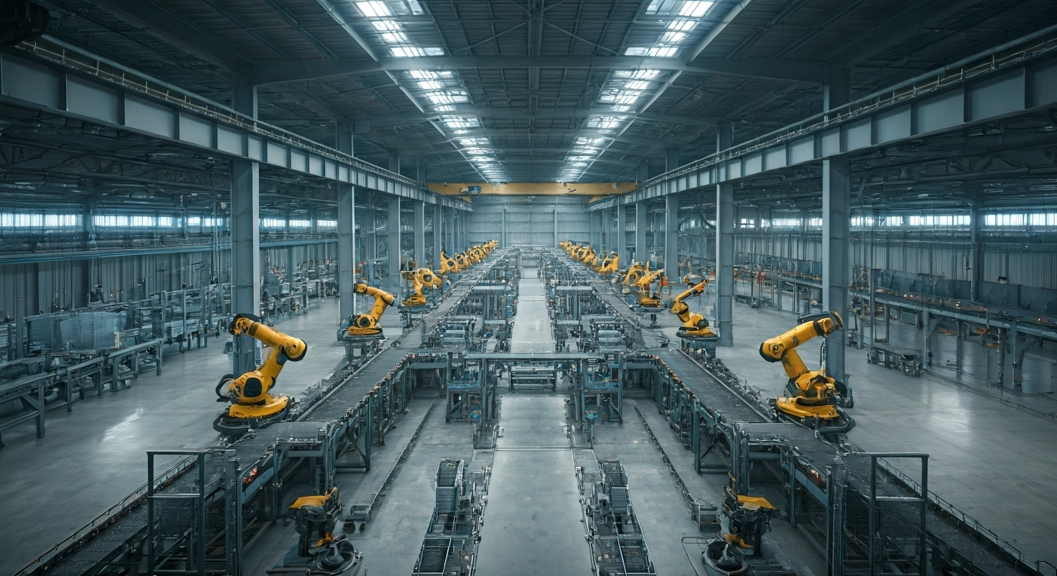
Key Highlights
- The automatic production line changes the manufacturing process. It cuts down on human intervention and helps everything run smoother.
- New technologies like the Internet of Things, artificial intelligence, and robotics make the production line faster and smarter.
- With automation, businesses get the same good product quality every time and can raise their production capacity.
- Automation also helps cut labor costs and brings down human errors, which are big benefits.
- Flexible systems let manufacturers deal with changes in market conditions and customer demand without trouble.
- Automation helps industries keep a competitive advantage while also making work more efficient and bringing new ideas.
Introduction
Today, in the world of manufacturing, using automation is not something extra. It is something every business needs to stay ahead. An automatic production line helps to change the whole manufacturing process. It takes away many problems and makes work more steady and reliable. With advanced automation, a business can keep up with what customers want and keep their product quality high, no matter how the market conditions change. When a company adds automation to the production line, it finds its work gets done faster and better. People see a new way of how things are made. In this guide, you will get a good understanding of production automation and learn what you have to do to use it in the right way.
The Complete Guide to Automatic Manufacturing System
Understanding Production Automation
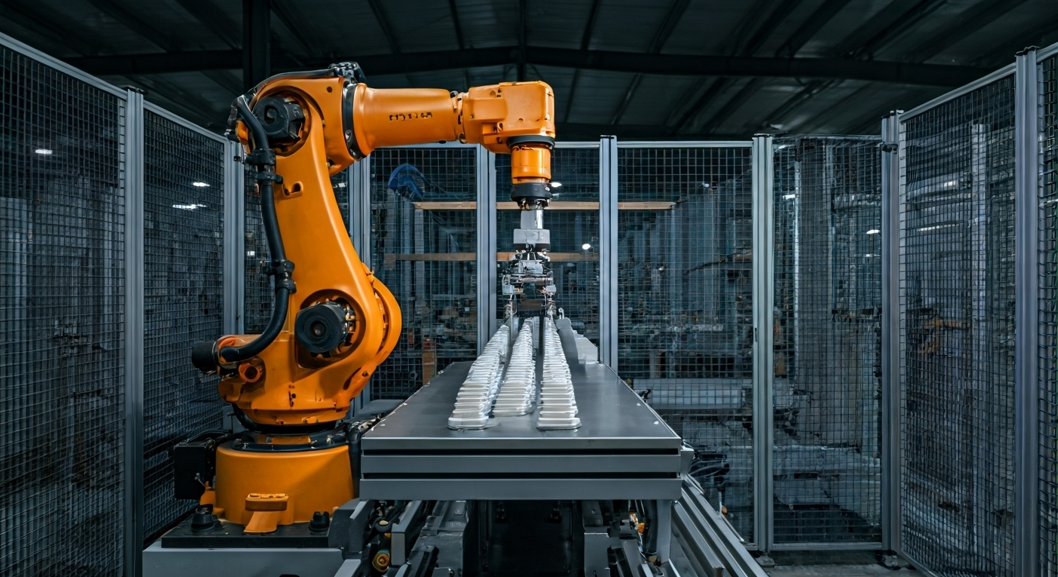
Automation is changing how industries work. It lets machines take over jobs that people do over and over again. These tasks can now be done by robots, which means there is not much human intervention. With the use of robots, these work systems can keep going day and night.
This new technology helps by giving more accuracy. It also brings down the cost to run a business. If manufacturers use automation, they have a better chance to stay in the game, be more flexible, and grow for a long time. In the next parts, we will talk more about what automation means and how it has changed different industries.
What is Production Automation?
Production automation is when a control system is added to a manufacturing process to make things run with very little human help. The main reason for this is to lower human errors, make production faster, and cut down on labor costs.
Control systems help machines and tools work together smoothly. When you use automation, there is less chance for mistakes that people might make if they get tired or lose focus. With this, you get steady and accurate work. Many businesses that use automation save real money as time goes on.
Setting up automation may mean you have to spend money first on machinery, software, and the control system. But, you also start spending less money on labor and avoid other ongoing problems. This helps bring good returns later. By choosing production automation, a company gets strong control over how things are made. This helps them keep up with what the market wants, deliver products faster, and make sure the quality is high.
Evolution of Automated Production in the United States
The history of automated production in the U.S. shows how the country changed in industry. Companies started using automation to keep up when market conditions called for faster work. Things like conveyor belts came in early. These new tools changed the manufacturing process for good.
When factories got bigger, automation started to give businesses a competitive advantage. The use of robotics and new machines helped them have more production capacity. At the same time, it let them keep their quality the same. By the late 1900s, automation had changed the way supply chains worked.
Now, Industry 4.0 brings together new ideas like AI and IoT. These things keep changing the manufacturing process all the time. The market will keep changing, and that means the push for newer ways to use automation will stay strong. This push helps U.S. companies stay ahead in the world
Key Components of Automated Production Systems
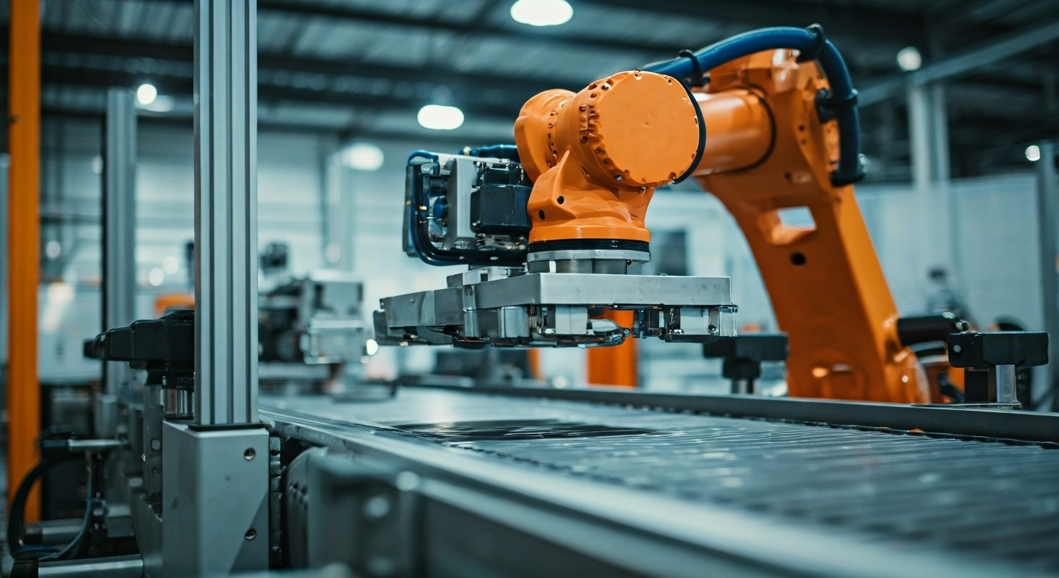
automated production systems have different connected parts. These include robotics, machinery, sensors, and controllers. Each one has a specific job that is important to the whole system.
Robotics and machinery help to cut down on manual labor. Sensors and controllers are needed to keep everything working together. All these components work together to make sure the work goes smoothly and the output stays the same every time. In the next sections, we will talk about robotics, machinery, and controllers to show how important they are in automation systems
Robotics and Machinery
Robotics and machinery are at the heart of any automated production line. They take on jobs that are either repetitive or risky. Some key pieces of equipment include:
- CNC machines that help with tasks needing precision.
- Conveyor belts that keep materials moving smoothly along the production line.
- Robotic arms that help with things like assembly or packaging.
- Automated lubrication systems that help cut down on machine downtime.
When companies use robotics in their systems, they get more accuracy and better reliability. The machines do not get tired, so they can keep working all the time and help a business meet tight deadlines.
The great thing about robotic machinery is its flexibility. These systems can be reprogrammed to handle different tasks. That means the production line can keep up when the market changes or when customers want something new.
Control Systems and Software
Control systems and software run an automated production line. They help things go smoothly. These systems use sensors and algorithms to watch the work, gather data, and make quick changes in real time.
Programmable Logic Controllers (PLCs) play a big role, making it easier to have automation for complicated steps. Algorithms help make right choices by using data. They react right away if the product quality drops or if something goes wrong with the equipment.
When businesses add supervisory software, they can see important information about the production line from far away. This helps them improve how things are done. Better control systems help keep product quality high, cut down how long things stop, and make the whole system work better for a long time.
Designing an Automated Production Line
Designing a good automated production line means making sure the right technology matches the learning goals for production. There has to be a balance between customer demand, product quality, and how efficient the work is. The main aim is to help people have less waste and get the most they can out of the work.
Manufacturers need to make each part of the line easy to use, with good systems that control things well based on what is needed. Next, we will talk about how to set clear goals and how to pick the right technology. Taking these steps leads to the best use of automation in the production line.
Assessing Production Goals and Objectives
Creating good automation starts with setting clear production goals. You need to know what you want, like to increase production capacity or to reduce costs. These goals help shape each decision.
First, look at what your production capacity should be. Think about market conditions and customer demand. Sometimes, you have to be ready for busy seasons. This can change when you start automation. Next, think about human factors in your work. There may be tasks that get more complicated because of human intervention. Try to swap these out with smarter automation systems.
If you focus on real results and on what your customers need, you can make a solid plan for your automation work. This will help you reach your goals in the best way.
Selecting the Right Technology and Equipment
Choosing the best technology is important for the success of your automation. The table below shows the key things you should think about:
Technology/Equipment | Key Benefits |
---|---|
IoT Sensors | IoT Sensors Watch things in real time and use data to make better decisions. |
AI Systems | IoT Sensors Watch things in real time and use data to make better decisions. |
CNC Machines | Give top precision and help you cut down on wasted materials. |
Advanced Robotics | Make it easy to change how you work when the market is different. |
Take time to check each piece of equipment. Make sure what you choose can work with what you already have and will continue to do so in the future. Pick the tools that match your production goals so the change is smooth and everything runs well. Automation, robotics, cnc, precision, sensors, and ai all help in this process.
Implementing Automation in Manufacturing
When you bring automation into the manufacturing process, it helps make products better and work faster. This step is about making the way work happens smoother. It also means adding strong control systems and doing a lot of testing to make sure everything works well together.
Good planning helps stop problems and makes sure the system is set up right. Go to the next parts to learn more about how to set up work steps and test everything, so your project goes well.
Workflow Planning and Process Mapping
A good workflow helps make automation run better. Start with a clear map of the current manufacturing process. You should look for places where things slow down or where people are needed again and again.
Once you have your workflow ready, put the tasks in order so you can cut down on waiting and help things move faster. Set up checkpoints to check quality. You should also spot any parts of the process that might need monitoring by sensors. Remember, people and their work, or human factors, are important. Try to make automation work with them, not against them.
When you map out the process well, you make a simple plan. This plan brings together people, automation, and new tools for better, faster results. This is the key to getting the most from every part of the job.
Integration and Testing Procedures
Integration helps machines and control systems work as a team on the production line. First, you connect all the hardware and software to let real-time data move between them.
The next step is testing. This means you use both simulation runs and live runs. It’s important to check if the sensors and controllers work well together at every step of the production line. Watch product quality and see if all parts stay in sync to make sure the system works well.
By testing and adjusting as needed, you make sure everything matches the needed standards. This helps make your automation strong and keeps product quality high.
Benefits and Challenges of Automation
Automation gives many good benefits but also brings some problems. For example, it can help lower labor costs and increase production capacity. At the same time, it needs a lot of money at the start.
When you know both the good and bad sides, you can get more from automation and handle any problems that come up. Next, we will see how automation makes things run better and helps with worker needs.
Increased Efficiency and Cost Savings
Automation helps boost efficiency and lower costs like never before.
- Fewer errors help keep product quality steady and cut down on spending.
- Better workflows help use less material and energy.
- Automated machines mean there is less need for workers, so you spend less money.
- Machines running all the time lets you make more, so it is easier to fill orders on time.
When companies focus on automation, they save a lot of time and money. This puts them in a better spot to keep making a profit and compete with others.
Addressing Workforce and Training Needs
Automation is changing the way people work. Workers need to learn new technical skills to handle and look after automated systems. Good training helps give operators more confidence. This also helps lower the effect of human factors on production.
Clear and open communication can make people less worried about change. If companies link their plans for workforce growth to their automation goals, they can help create a culture where people always keep learning and thinking about new ideas. This is good for long-term success with automation and people.
Conclusion
To sum up, automation in production is more than just a trend. It is a big step forward for manufacturers who want to be more efficient and save money. When you know the main parts, set up the right automated lines, and use the right technology, your business can get many good results. But, you should also be ready for some challenges. These can include training your workers and making sure everything works together. As you start this new path, remember that the future of making things is in new ideas like automation. If you want help, you can ask for a free consultation to learn how to automate your own processes in the best way.
Frequently Asked Questions
What industries benefit most from production automation?
Industries such as automotive, electronics, food and beverage, and pharmaceuticals get a lot from automation in their production. When they use robotics and better production lines, these companies make sure product quality stays high. They also meet customer demand in a good way.
How does automation impact jobs in manufacturing?
Automation is changing jobs in manufacturing. It cuts down on the need for human intervention in tasks that are done the same way over and over. But, there is now a bigger need for skilled workers who can look after and fix these automated systems. This helps balance labor costs and also keeps human factors in mind during the process.
What are the main costs involved in automating production?
Initial costs cover buying machinery, equipment, and software. You also need to think about labor costs, which come from training the workforce. Over time, you can get benefits such as less material waste and less downtime. These good things often help balance out what you first spend.
How can small businesses begin automating their production lines?
Start by looking at the production lines to find places where you can use automation. Choose technology that does not cost a lot, like sensors or controllers that can be set up to do certain tasks. Add these solutions slowly so they fit well with what you already have. This way, you can use automation to lower the need for human intervention and help things run better.
What future trends are shaping production automation in the U.S.?
New trends are changing the way companies use automation. These include advanced AI, robotics, and IoT sensors. With these, people can make smarter choices. It helps them adjust fast to new market conditions. The use of these tools also makes the work faster and better. Companies can see better results when they use sensors, ai, and robotics in production.