The Complete Guide to Automatic Manufacturing System
The Complete Guide to Automatic Manufacturing System

Key Highlights
- Explore the different kinds of automation systems that the manufacturing industry uses, like fixed, programmable, and flexible automation.
- Learn how robotics and the Industrial Internet of Things (IIoT) are changing old factories into smart factories with better connectivity.
- See the good things that automation brings, like cost reduction, making work more efficient, and better quality control.
- Get to know about the problems companies face, such as workforce adaptation and dealing with complex systems to make the most of their investments.
- Look at real case studies from the automotive and food and beverage industries to see how they use automation with good results.
- Find out about what’s coming next, like new uses for artificial intelligence and green manufacturing initiatives that help make the industry more sustainable.
Now, let’s look at the basics of industrial automation with an easy-to-read introduction.
Introduction
If you want to know how automation can change a manufacturing system, you are in the right place. Industrial automation uses the latest automation technology, including robotics and special software. These carry out jobs with care and with less help from people. This changes how the automation process works. It helps make more products quickly and lowers human error. Today, more factories are becoming smart factories. With automated systems, these factories handle rising costs and fewer workers in better ways. Automated systems are now key to how we make things. Factory automation is a big part of the current world of manufacturing.
Understanding Factory Automation
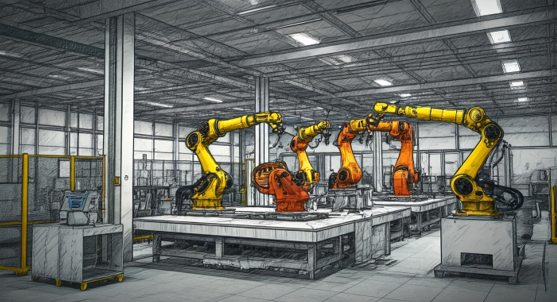
When you look at the manufacturing process, it is important to be clear. Industrial automation makes everything move faster. It helps products be the same every time, and keeps people safer at work. When you know the types and the ways automation works, you can make things in the factory run better.
Factory automation does more than just make production tasks easier. It lets people and machines handle complex systems together. When automated systems work with people, the company can get more done. But what is factory automation, and how did it change over the years?
Defining Factory Automation
At the most basic level, factory automation is about using technology and machines to do work on their own in a production process. These automated manufacturing systems use advanced machinery, such as robotics, systems you can program, and setups that control things right away. All of this is done to lower how much people need to do and to make everything run better.
In manufacturing, automation does more than just make products faster. It helps things be more precise, cuts down on things that get wasted, and helps every product reach high quality control again and again. For example, robotic arms, with sensors, can put together parts of a product much quicker and with better precision than if people did the job by hand.
Another big reason for automation is to lower risk, especially in places that are unsafe for people. Robots and machines in the entire production process can handle tasks like working with harmful chemicals or operating in really hot or cold areas. This makes dangerous work safe for everyone by letting the machines do it. Because of these good things, many places use automated methods now, and they have become an important part of the entire production process.
The Evolution of Automation in Manufacturing
Modern industrial automation started because of many years of new inventions and changes in technology. The manufacturing industry has seen big changes during four industrial revolutions. The first one began in the 18th century, with steam-powered machines changing the way things were made.
In the 1900s, Henry Ford’s assembly line showed everyone how “fixed automation” works. Here, machines helped to make products the same way every time. Then, the 1960s and 1970s brought in programmable tools like CNC machines. These machine tools made it easier to change how things were built when new products came out. After that, we saw Industry 4.0, which uses AI, machine learning, and the IoT to let devices talk to each other in real time and do more by themselves.
Over time, we now see many types of automation to handle the changing needs of making things. The manufacturing process today is better because of automated systems. Some setups use fixed automation, and some use flexible automation. But what is powering all this change? Let’s take a look at the most important technologies in automation right now.
Core Technologies Powering Factory Automation
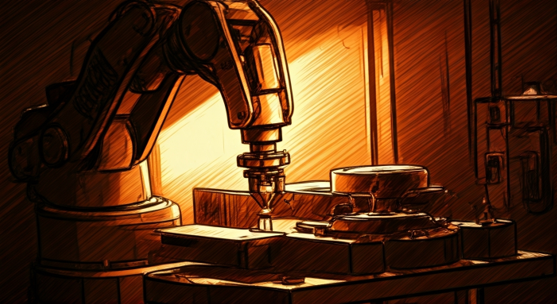
The efficiency in today’s industrial systems happens because of the use of new automation technology. The main things that make this possible are control systems, information technologies, and robotics that help change the way production works.
These systems help connect different parts of the workflow and make manufacturing systems more accurate. For example, smart sensors watch over the production line in real time and help create better communication as things get made. Key tools like robotic arms, IoT devices, and analytics that use data are pushing factories to new heights. These advancements show us just how much the use of automation, sensors, and new technology can do for modern production.
Robotics and Collaborative Robots (Cobots)
Robotics and collaborative robots, or cobots, are now a key part of industrial automation. These robots work with people in the factory to take care of repetitive tasks. By working together, cobots and humans can raise overall efficiency and get more work done in less time. Cobots have sensors and advanced control systems that help them do complex tasks with great precision.
Many manufacturers use flexible automation to let these robots handle different jobs. This way, they can scale their work, manage workflows better, and cut down human error. The result is stronger quality control and better production outcomes for everyone involved.
Industrial Internet of Things (IIoT)
The Industrial Internet of Things (IIoT) is changing the manufacturing industry. It links machines, devices, and control systems. This helps with real-time data and better connectivity. With IIoT, companies can watch production more closely and reduce human error and downtime.
Smart sensors and analytics help manufacturers get the most out of each machine. They also can know when a machine will need fixing and handle inventory in a good way.
This blend of IIoT and control systems helps overall efficiency and supports flexible automation. It lets operations in the production environment run smoothly, even when things get complex.
Types of Automation Systems in Factories
There are different types of automation built to fit the needs of the factory. Fixed automation is good for jobs that stay the same and need to be done in large amounts, like making cars. If you have to make things in smaller sets, then programmable automation is better.
Flexible automation is changing the way people work. It can quickly adjust in real time to new product ideas. These types of automation cover simple jobs like putting parts together on assembly lines, and also help create different products without big changes to setup.
Let’s take a look at what makes fixed-hard automation and programmable-flexible automation systems special.
Fixed and Hard Automation
Fixed automation, which people sometimes call hard automation, uses fixed setups made for doing the same task many times, like you see in assembly lines. This type of automation is built for high output. The machinery keeps working nonstop. It does not need changes.
A good example is the automotive industry. They use fixed automation a lot. Conveyor belts and robots help put cars together, step by step. But since this equipment is set up to do just a few things, it cannot handle new designs well or change jobs easily.
Starting out with hardware for this type of automation can cost a lot. But over time, the cost goes down because you make so much at once. Companies that need strong precision and do a lot of repetitive tasks really gain from using hard automation.
Programmable and Flexible Automation
Unlike setups that are fixed in place, programmable automation lets you adjust and change what you produce for different batches. For example, in manufacturing, people use programmable logic controllers (PLCs) to change settings. This means they can make updates quickly and do not have to change the whole process each time.
Flexible automation takes this idea even further. This type of automation uses systems that can change as needed in real time. It works well when you need high precision, such as in 3D printing unique car parts or meeting packaging needs for medicines. Flexible automation stands out because you can change it easily when needed, but there may be a little bit of downtime at first when making adjustments.
The ability to work with different products and switch between them quickly is one reason why flexible automation has become so popular. It helps companies that need to be quick and responsive but still keep good, steady quality. Because the market can change fast, many companies now use flexible automation and programmable automation to stay ahead.
Let’s now focus on certain factory processes and look at how automation helps in the setup of production lines or the handling of storage and logistics.
Key Areas for Automation Within a Factory
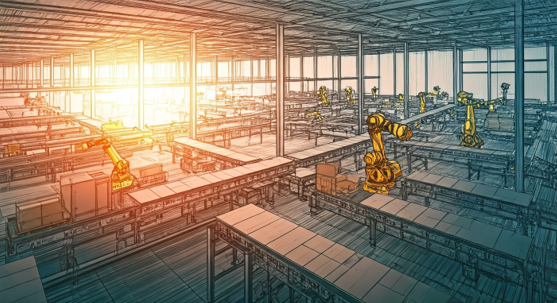
To make a factory work better, you need to look at a few things that can be automated. Using programmable automation helps your production line because it makes repeating jobs much easier. It also cuts down on human error. When you add strong inventory management and software systems, you can follow your stock in real-time and see helpful analytics. This makes warehouse management smoother and builds better connectivity in the supply chain. Focusing on these important areas gives your manufacturing system more flexibility. That can change your whole production process for the better.
Production Line Automation
Improvements in production line automation have a big effect on the whole manufacturing process. Using programmable logic controllers (PLCs) and robots, you can now make workflows run with high efficiency. This helps cut down on human error and reduces downtime. When you bring automation technology into the process, the production line can handle different products and change fast to meet new production needs. In smart factories, automation in assembly lines helps take care of many repetitive tasks. It also helps improve overall efficiency, so you get lower operational costs and more output. For any company, this makes a huge difference in how well they work.
Inventory and Warehouse Management
Good inventory and warehouse management are important in an automated production process. When you use automation technology, your business can cut down on human error. It also helps to move goods quicker and makes it easier to watch inventory in real time. By putting sensors and programmable logic controllers (PLCs) in place, you get smart inventory control. This can help make the right amount of stock is always there and stop downtime from bottlenecks.
Also, when you add information technologies like enterprise resource planning (ERP) systems, you get better analytics and can make smarter choices. These tools help you control the entire production process and make your automated operation more flexible. Everything works faster and can change when you need it to.
Benefits of Automating Your Factory
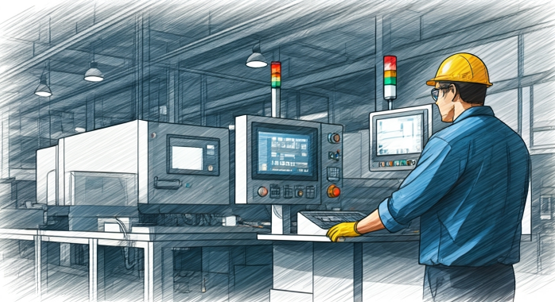
Automation in a factory helps make the production process better and faster. The use of programmable logic controllers (PLCs) and top-notch control systems cuts out human error. This keeps the quality high and downtime low.
Automated systems help save money because machines do repetitive tasks much better than people can. This leads to less waste and lets the workforce work on complex tasks that need more skill. All of this creates new opportunities for workers and makes the overall efficiency of the production environment better.
Cost Reduction and Improved Efficiency
Cutting down costs and making things work better are very important for manufacturing companies these days. When a company uses automated manufacturing systems, it can lower human error and speed up how things get made. The use of advanced robotics, programmable logic controllers, and smart manufacturing tools can help fix bottlenecks and help companies make better use of what they have in the production environment. By doing this, companies save money, boost their overall efficiency, and get ready to change when the market or customer needs shift.
Enhanced Safety and Quality Control
By bringing in robotics and automation technology, the production process becomes a lot safer. This big step lowers the risk of accidents at work. In the manufacturing industry, collaborative robots—called cobots—work with people to take on repetitive tasks that can be dangerous. This helps cut down on human error.
With automation, quality control also gets better. It uses sensors and vision systems to watch the entire production process in real time. This way, every product meets the high standards set by the industry. Because of this, there is less downtime and fewer problems with defects, and the quality stays consistent.
Challenges and Considerations in Factory Automation
Dealing with factory automation brings many things to think about. The cost at the start for things like programmable logic controllers and robotics can be high. So, you need to take a good look at ROI to decide if the long-term gain is worth it. The workforce also has to change with automation. Workers need to learn new skills to work with automated systems. Setting up training helps close the learning gap. It also makes it easier for people and machines to work together. This kind of teamwork cuts down on human error and helps the manufacturing process run well. It is important to get everyone on board to make automation work and get the best overall efficiency out of it.
Upfront Investment and ROI Analysis
Looking at the upfront investment for an automated manufacturing system shows that there are many things to think about. These things affect the overall efficiency of the whole production environment. To get the best value out of your manufacturing system, you need to pick the right mix of programmable logic controllers (PLCs), industrial robots, and other types of machinery. This can help you make a good ROI analysis. When you add up the possible savings from spending less on labor and lowering human error, you get a better picture of your finances.
Using analytics and enterprise resource planning (ERP) systems also helps. With ERP, your team can track important data about how well your system is working. This makes it easier to make smart choices about investments in automation technology for your automated manufacturing system. So, you can get a clear view of how much these choices can pay off for your company.
Workforce Adaptation and Skill Development
Moving to automation means the workforce needs to adapt and learn new skills. When factories bring in automated systems and advanced tools, people need to be ready. It's important to have training that covers robotics, analytics, and how to run machines. This will help employees handle automated systems every day and cut down on human error. When companies support ongoing learning, the workforce will be better at solving complex tasks and handling change. This focus on being ready for anything helps companies stay strong and make the most of new opportunities in a changing, automated world of work.
Real-World Examples of Factory Automation
Many industries use automation and see big changes. In the automotive field, assembly lines use industrial robots to get more precision and to cut down on human error. This helps raise the number of cars they make. In the food and beverage business, sensors and automated machines help pack products faster. These tools cut downtime and make quality control better. These real-world changes show how different types of automation work well. Both programmable and flexible automation help smart factories turn old ways of working into something much more efficient.
Automotive Industry Automation Success Stories
Examples of automation in the automotive industry show big steps forward in how we make vehicles. When companies use industrial robots on assembly lines, they make the production process smoother. This helps cut down on human error and boosts overall efficiency. With flexible automation, manufacturers can switch to making different products quickly. There is less downtime, and this lifts productivity.
Smart factories are leading the way by using real-time analytics and programmable logic controllers. They use this data and technology to run operations better every day. Bringing in automation technology changes complex tasks into easier jobs and helps companies stay strong in the market.
Food & Beverage Manufacturing Automation
Automation in the food and beverage sector helps the production process run better and faster. It uses new control systems like programmable logic controllers (PLCs) and vision systems. These systems help people avoid mistakes and give real-time updates on the whole process. With automated systems, workers can handle the ingredients and manage the packaging in a more accurate way. This means there is less downtime, the assembly lines flow quicker, and everything runs smoothly. These new ideas in automated technology let companies keep up with high standards and also bring new opportunities. Now, businesses can change the way they work and react quickly when customers' needs change.
Future Trends in Factory Automation
Factory automation keeps changing how manufacturing works. Now, artificial intelligence and machine learning help with fixing machines before they break and making better choices. This means companies can be more efficient with their work. As smart factories grow, the use of sensors in IoT helps to watch things in real time. These sensors send data to analytics tools, so information from complex systems is always up-to-date. With this, people can make quick changes when needed. Also, there is a big focus on using green and energy-saving technology. Companies now try to work in ways that are good for the environment. This shift creates new opportunities in production, as automation and smart ideas help solve both efficiency and environmental problems together.
Artificial Intelligence and Machine Learning Integration
Bringing artificial intelligence and machine learning into factory automation changes how things are made. With these advanced tools, companies can make work better and improve overall efficiency. These systems help cut down on human error in the process. They use algorithms and analytics to look ahead and warn people about possible machine failures. This way, there is less downtime, and things can keep moving.
AI can also help with quick decision-making in hard or tricky systems, so production runs in real time and meets the current demand. As smart factories grow and change, using AI and automation together will bring new opportunities for businesses to do better and come up with new ideas across many factory jobs.
Sustainability and Green Manufacturing Initiatives
Bringing sustainable ways into the automated manufacturing system helps factories be more efficient and use less of their resources. When you use programmable logic controllers (PLCs) and sensors, you can keep an eye on energy use in real time. This helps to make the process better and waste less. Using flexible manufacturing systems in the manufacturing industry also means you can work with eco-friendly materials and have less chance for human error. Going for green choices does not just support a better world, but it also brings in consumers who care about the environment. There are new opportunities for the manufacturing system to grow when it stays automated and uses PLCs and sensors.
Conclusion
Moving to an automatic manufacturing system is now very important for factories that want to be better and faster. When businesses use things like automation technology, they make their ways of making products much better. This helps them lower human error and makes quality control stronger across different parts of the manufacturing industry. Using robotics, sensors, and programmable logic controllers is a good way to add automation to the workflows these companies already use.
As the manufacturing industry keeps moving forward, being able to use new automation technology can open up new opportunities for getting ahead. With automated systems, factories become more ready to face competition in the world and be more sustainable as well. When factories use automated solutions, they can be better than others and stay strong in the market.
Frequently Asked Questions
What is the best starting point for factory automation?
The best way to begin with factory automation is to look at your current ways of working. Find where problems or slow spots, known as bottlenecks, exist. Take the time to study how production moves step by step. Talk to everyone involved to get their thoughts. Focus on parts of your work that could most help if they were faster or easier. This helps you plan well for automation and get the most out of your efforts.
How does automation affect employment in manufacturing?
Automation in manufacturing can take over jobs, as machines start to do some tasks done by people. But it can also help to make new jobs that need advanced skills. This means that the workforce has to learn new things to keep up. The automated workplaces show how important it is for people to keep training and growing their skills so they can do new jobs when things change. This helps employees be ready for the new roles in a world with more automation.
How long does it take to see ROI from factory automation?
The time it takes to see ROI from factory automation can be different for everyone. Most people see it happen between six months and three years. The speed depends on a few things, like how big the automation project is, the type of industry, how well it gets set up, and how good the team is at making improvements as they work. These things help to boost productivity and bring costs down over time.
Can small and medium factories afford automation?
Yes, small and medium factories can have automation for their needs. They can do this with options that can grow as they do, money plans to help pay, and tech made just for them. When factories pick ways to use automation that do not cost much, they can get more work done in less time. They can also do better than others in the same line of work. Over time, the factory can get back the money it spends, thanks to fewer work costs and things running better with the help of automation.
What are common mistakes to avoid when automating a factory?
Some common mistakes to avoid in factory automation are not giving enough importance to training employees, not joining new technologies the right way, and not doing a good check on what you get back for your investment. It is also a mistake to forget about taking care of the machines and leaving out people who have a say in the process. These things can stop you from making automation work well and getting better results.
What is an automatic manufacturing system and how does it work?
An automatic manufacturing system is a technology-driven process that utilizes machinery and software to produce goods with minimal human intervention. It streamlines operations by integrating robotics, sensors, and data analytics to enhance efficiency, reduce errors, and increase production speed, ultimately leading to optimized resource management and cost savings.