What is the Integration Between MES and ERP?
What is the Integration Between MES and ERP?
The integration between MES (Manufacturing Execution System) and ERP (Enterprise Resource Planning) systems involves linking these two critical components of the manufacturing ecosystem to streamline operations. MES System Integration focuses on real-time monitoring and control of production processes on the shop floor, while ERP manages broader business functions like finance, procurement, and inventory management. By integrating MES with ERP, organizations can synchronize production data with business processes, facilitating better decision-making and resource optimization across the enterprise. This integration enables seamless communication and data exchange between planning and execution, allowing for improved efficiency, visibility, and coordination throughout the manufacturing process.
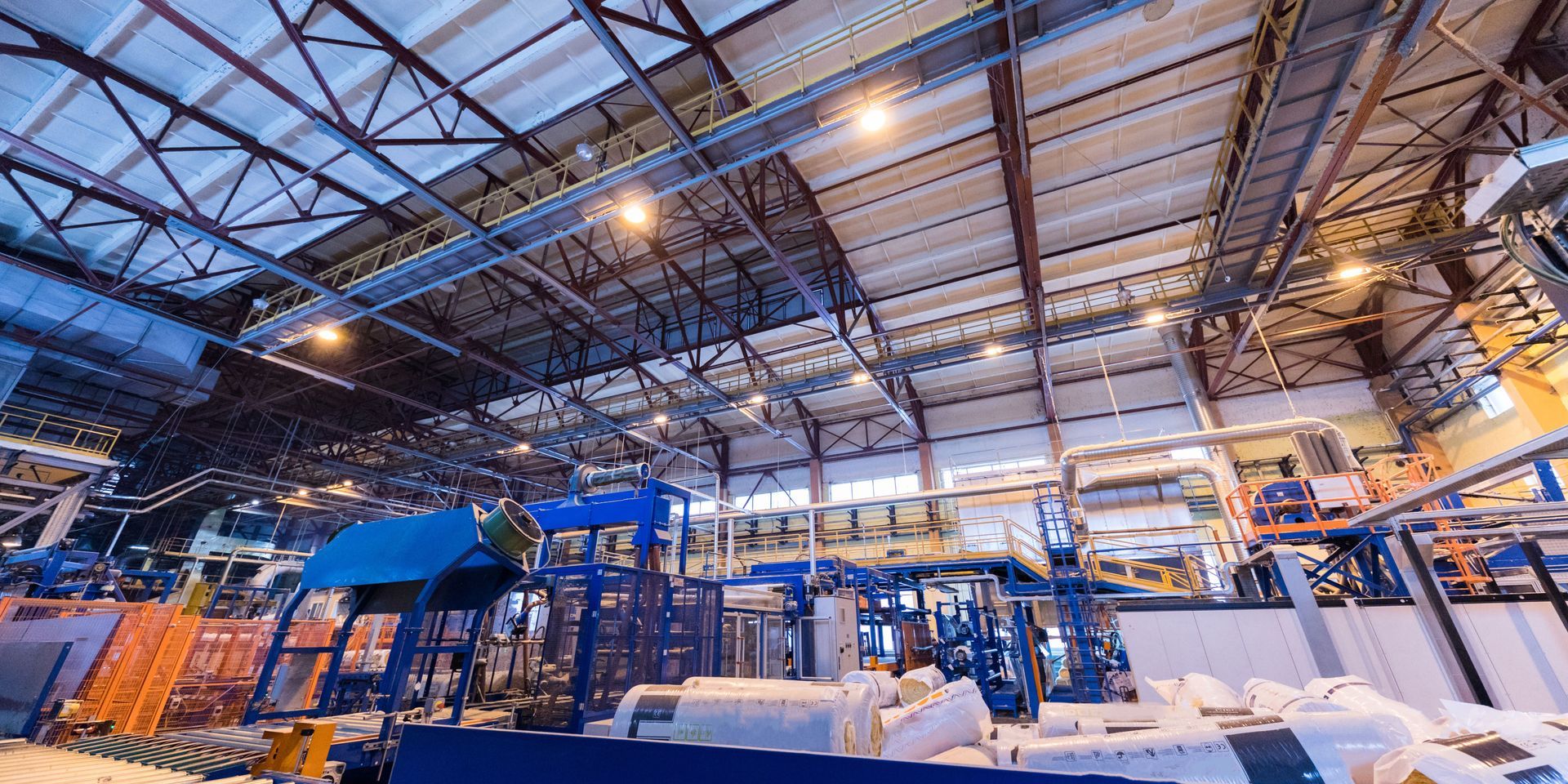
MES vs ERP
MES (Manufacturing Execution System) and ERP (Enterprise Resource Planning) systems serve distinct but complementary roles in manufacturing. While MES system integration focuses on optimizing and controlling production processes on the shop floor, ERP manages broader business functions such as finance, inventory, and procurement. MES provides real-time visibility into production activities, while ERP integrates data from various departments to facilitate strategic decision-making at the enterprise level. Integration between MES and ERP systems ensures seamless flow of information, enabling organizations to achieve greater operational efficiency and agility.
MES ERP Integration
MES ERP integration involves linking Manufacturing Execution Systems with Enterprise Resource Planning systems to streamline manufacturing operations. By integrating MES and ERP systems, organizations can synchronize production data with business processes, enabling better decision-making and resource optimization. MES ERP integration facilitates real-time communication between shop floor activities and enterprise-wide functions, enhancing visibility and control over the entire manufacturing process. This integration ensures that production activities align with business objectives, leading to improved efficiency and responsiveness.
What is MES?
MES stands for Manufacturing Execution System, which is a software solution designed to optimize and control manufacturing operations on the shop floor. These systems provide real-time visibility into production processes, enabling organizations to monitor and manage activities such as production scheduling, quality control, and resource allocation. MES software captures data from machines, operators, and other sources to facilitate decision-making and improve overall efficiency. By implementing MES, organizations can streamline their manufacturing processes, reduce costs, and enhance product quality and customer satisfaction.
Manufacturing Execution System
A Manufacturing Execution System (MES) is a software solution designed to streamline and optimize manufacturing operations. MES software enables real-time monitoring, control, and tracking of production processes on the shop floor. By providing visibility into machine performance, inventory levels, and workforce efficiency, MES systems help organizations identify bottlenecks and inefficiencies to improve overall productivity. Additionally, MES facilitates data collection and analysis, empowering decision-makers with actionable insights to drive continuous improvement initiatives.
MES Software
MES software encompasses a range of applications and tools designed to support various aspects of manufacturing execution. These software solutions typically offer functionalities such as production scheduling, quality management, and inventory tracking. MES software vendors provide customizable solutions tailored to the specific needs of different industries and production environments. By implementing MES software, organizations can enhance operational efficiency, reduce lead times, and ensure compliance with regulatory standards, ultimately driving greater profitability and competitiveness.
What Does MES Stand For?
MES stands for Manufacturing Execution System, which is a software solution designed to optimize and control manufacturing operations on the shop floor. These systems provide real-time visibility into production processes, enabling organizations to monitor and manage activities such as production scheduling, quality control, and resource allocation. MES software captures data from machines, operators, and other sources to facilitate decision-making and improve overall efficiency. By implementing MES, organizations can streamline their manufacturing processes, reduce costs, and enhance product quality and customer satisfaction.
List of MES Software
A variety of MES software solutions are available to address the diverse needs of manufacturing industries. Some notable MES software options include Siemens MES, Wonderware MES, and Apriso MES, each offering comprehensive features for production management and control. Other prominent MES software vendors include Rockwell Automation, Aegis Industrial Software Corporation, and Plex Systems, providing solutions tailored to various manufacturing sectors. By selecting the right MES software, organizations can optimize their production processes and achieve greater efficiency and competitiveness.
MES Software Vendors
Several companies specialize in providing MES software solutions to industries worldwide, offering a combination of technology and industry expertise. Leading MES software vendors include Siemens, Wonderware, Rockwell Automation, and Aegis Industrial Software Corporation, each offering comprehensive solutions to optimize manufacturing operations. These vendors provide scalable and customizable MES software tailored to the specific needs of different industries and production environments. By partnering with reputable MES software vendors, organizations can leverage advanced technologies to improve productivity, quality, and agility.
Is SAP an MES System?
While SAP offers some MES functionalities within its suite of solutions, it is primarily known as an Enterprise Resource Planning (ERP) system rather than a dedicated MES system. SAP's Manufacturing Execution module provides features for shop floor control, production tracking, and quality management, but it may not offer the depth of functionality found in standalone MES software. However, organizations can integrate SAP ERP with specialized MES solutions to achieve end-to-end visibility and control over their manufacturing processes. This integration allows organizations to leverage the strengths of both SAP ERP and MES systems, ensuring efficient production operations and optimized business processes.
SAP MES
AP MES (Manufacturing Execution System) is a solution offered by SAP to optimize and control manufacturing operations. SAP MES provides functionalities such as shop floor control, production tracking, and quality management to improve efficiency and productivity. While SAP is primarily known for its Enterprise Resource Planning (ERP) software, SAP MES complements ERP systems by providing real-time visibility and control over production processes. Integration between SAP MES and SAP ERP enables organizations to synchronize production activities with business processes, leading to improved operational efficiency and responsiveness.
What is the Difference Between MES and SAP?
The difference between MES (Manufacturing Execution System) and SAP lies in their primary functions and scope within the manufacturing environment. MES is specialized software designed specifically for managing and optimizing manufacturing operations on the shop floor, focusing on real-time monitoring, control, and analysis of production activities. On the other hand, SAP (Systems, Applications, and Products) is an Enterprise Resource Planning (ERP) system that integrates various business functions such as finance, supply chain, and human resources into a unified platform. While MES specializes in managing production processes, SAP ERP covers broader business processes, with MES often integrated as a module to provide real-time production data and control capabilities within the SAP ecosystem.
ERP vs MES vs SCADA
ERP (Enterprise Resource Planning), MES (Manufacturing Execution System), and SCADA (Supervisory Control and Data Acquisition) systems serve different purposes in manufacturing. ERP systems focus on managing business functions such as finance, procurement, and inventory management, while MES systems optimize and control production processes on the shop floor. SCADA systems, on the other hand, are used for real-time monitoring and control of industrial processes, often at the machine or equipment level. While ERP provides a broad view of the enterprise, MES offers detailed insights into production activities, and SCADA focuses on real-time control and monitoring.
What is ISA 95 in Connection With MES and ERP Integration?
ISA-95 is a standard developed by the International Society of Automation (ISA) for the integration of manufacturing and enterprise systems. ISA-95 defines models and terminology to facilitate seamless communication and data exchange between Manufacturing Execution Systems (MES) and Enterprise Resource Planning (ERP) systems. By adhering to ISA-95 standards, organizations can establish efficient integration between MES and ERP systems, enabling better decision-making and resource optimization across the manufacturing enterprise. This standardization ensures interoperability between MES and ERP systems, facilitating smoother communication and data exchange between the shop floor and the enterprise.
How do Manufacturing Execution Systems Work Together with ERP Systems
Manufacturing Execution Systems (MES) and Enterprise Resource Planning (ERP) systems collaborate to streamline and optimize manufacturing operations. MES systems provide real-time visibility and control over production processes on the shop floor, capturing data related to production activities, quality, and inventory. This data is then integrated with ERP systems, enabling better coordination of production planning, resource allocation, and order fulfillment across the enterprise. By working together, ERP and MES systems ensure that production activities align with business objectives, leading to improved efficiency, quality, and customer satisfaction.
MES SERP and MES Systems
Manufacturing Execution Systems (MES) and Enterprise Resource Planning (ERP) systems collaborate to optimize manufacturing operations and improve overall efficiency. MES systems provide real-time visibility and control over production processes, capturing data related to production activities, quality, and inventory. This data is then integrated with ERP systems, enabling better coordination of production planning, resource allocation, and order fulfillment across the enterprise. By working together, ERP and MES systems ensure that production activities align with business objectives, leading to improved efficiency, quality, and customer satisfaction.
At Which Level of MES and ERP Systems Falls
MES and ERP systems operate at different levels within the manufacturing hierarchy. MES systems typically operate at the shop floor level, focusing on real-time monitoring and control of production processes. In contrast, ERP systems operate at the enterprise level, managing broader business functions such as finance, sales, and supply chain management. However, with integration between MES and ERP systems, organizations can achieve seamless communication and data exchange, enabling efficient coordination between shop floor operations and enterprise-wide activities.