Is an OPC Server a SCADA
Is an OPC Server a SCADA
Let me clarify this for you: An OPC communication Server is unequivocally not a SCADA system but rather a crucial and indispensable component within SCADA systems. It plays a pivotal role in facilitating the seamless communication between various hardware and software components within the larger SCADA architecture. While the OPC Server acts as a bridge, enabling data exchange between different devices and applications, it is important to note that it is not synonymous with the entire SCADA system itself. The OPC (OLE for Process Control) standard is not just widely used but has become an absolute necessity in the field of industrial automation. It plays a crucial role in facilitating seamless communication between various devices and software applications. This standard has revolutionized the way information is exchanged, ensuring efficiency, accuracy, and reliability in industrial processes. Its widespread adoption underscores its indispensability in modern industrial settings, where swift and reliable communication between different components is paramount for smooth operations.
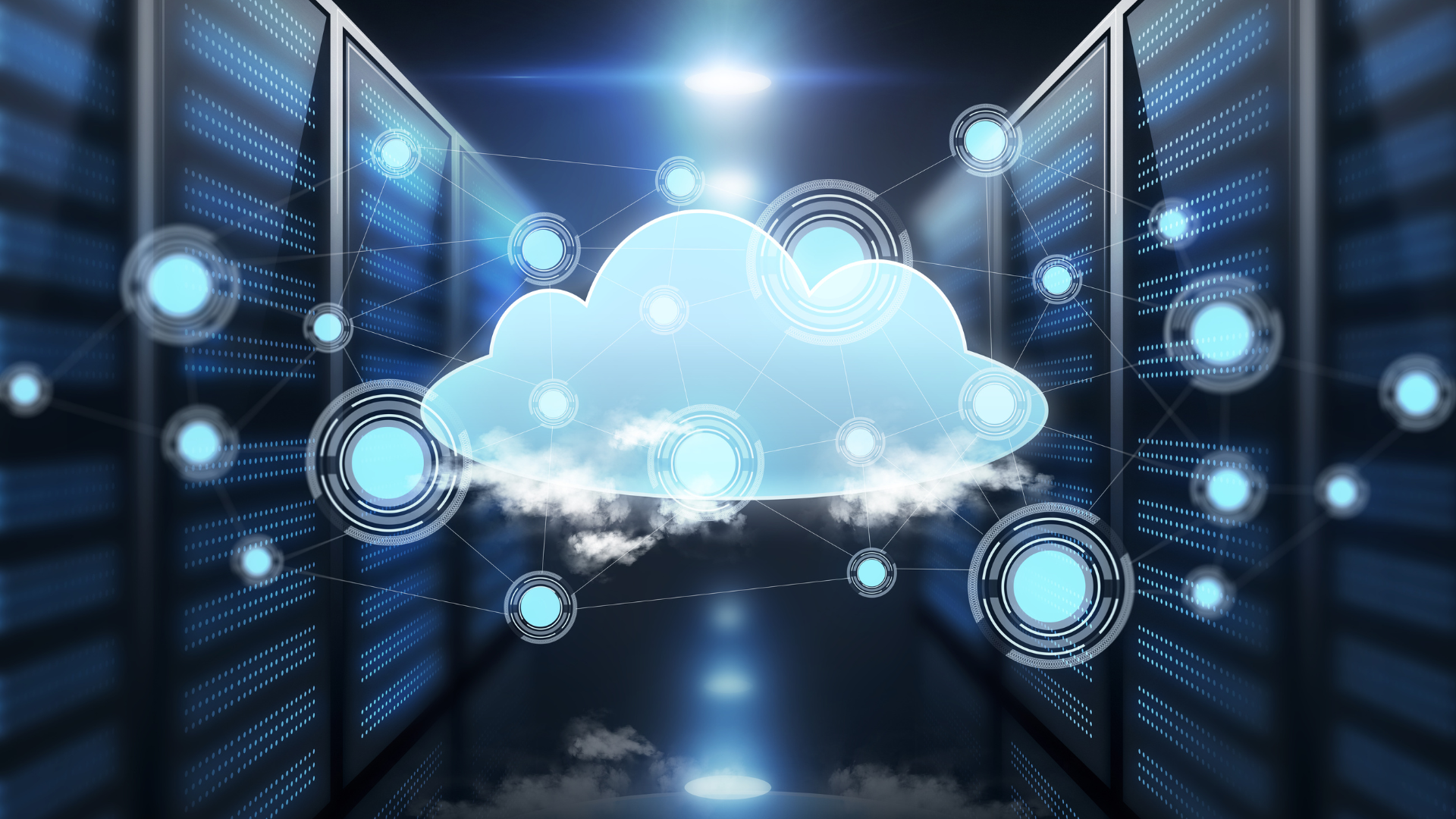
SCADA Systems
SCADA systems, also known as Supervisory Control and Data Acquisition, play a crucial role in monitoring and controlling numerous processes in industries. These advanced systems are specifically designed to ensure seamless supervision and precise control over industrial operations. With their robust capabilities, SCADA systems empower industries to maintain efficient workflows, optimize productivity levels, and enhance overall operational performance. By constantly collecting real-time data from various sensors and devices, SCADA systems provide invaluable insights that enable businesses to make informed decisions promptly. It is undeniable that SCADA systems have revolutionized industry operations with their unparalleled monitoring and control capabilities Servers play a crucial role as the assertive interface between various systems and the devices they communicate with, notably Programmable Logic Controllers (PLCs). They serve as the rock-solid bridge, ensuring seamless communication and efficient data exchange between these systems and devices. By leveraging OPC Servers, organizations can confidently harness the power of their PLCs, enabling robust control and automation processes with utmost reliability.
OPC SERVERS
A plethora of OPC Servers, including both commercially available and open-source alternatives, are accessible to cater to diverse needs. Commercial OPC Server software stands out by providing an array of advanced features and extensive support that can significantly enhance the functionality and performance of your system. On the other hand, open-source solutions offer unparalleled flexibility for customization, allowing you to tailor the server according to your specific requirements and preferences.
OPC Communications
OPC Servers, with their versatile capabilities, can be effortlessly configured to establish seamless and reliable communication with a wide range of devices or protocols. This includes the ability to interface efficiently with renowned Siemens PLCs, enabling streamlined data exchange and ensuring optimal performance in industrial automation environments. With OPC Servers at your disposal, you can confidently harness the power of connectivity and enhance productivity in your operations. These incredible OPC Servers empower seamless and efficient data exchange between devices and the SCADA system or any other client applications. They achieve this by utilizing standardized OPC interfaces, such as the powerful OPC DA (Data Access), which guarantees a smooth and reliable communication framework.
Let's take the example of an OPC Server configuration. When setting up this configuration, it is crucial to focus on various communication parameters that play a critical role in establishing a seamless connection. These parameters include configuring precise IP addresses and ports, which must be carefully selected to ensure efficient communication between client applications and the OPC Server. Additionally, attention should be given to selecting specific tags from a Programmable Logic Controller (PLC) that need to be accessed by client applications. By meticulously attending to these details, you can guarantee smooth and reliable data exchange within your system.
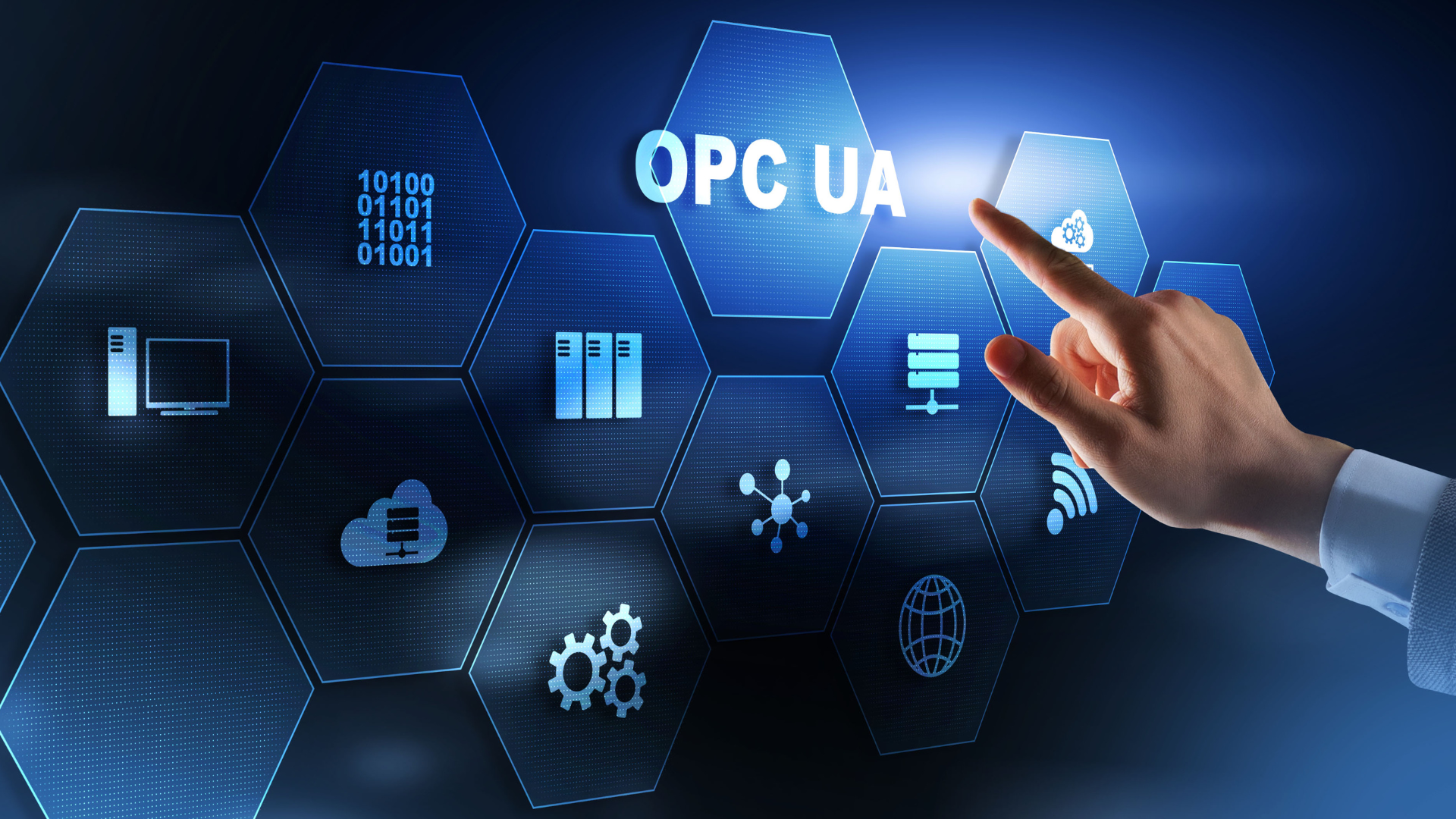
Comparing OPC Servers
When evaluating and comparing various OPC Server options, such as the renowned TOP Server vs Kepware, it is absolutely crucial to carefully take into account a multitude of factors. These factors include but are not limited to compatibility with specific devices or protocols, ease of use that ensures seamless integration into existing systems, scalability to meet future needs without any compromises, unwavering reliability for uninterrupted operations, the availability of top-notch technical support for prompt assistance when needed, and lastly licensing costs that align with your budgetary requirements. By conducting a comprehensive analysis of these critical aspects, you can confidently make an informed decision about which OPC Server solution best suits your unique needs and empowers your organization to excel in its operations.
In summary, it is crucial to note that an OPC Server, although not a SCADA system in itself, plays an absolutely pivotal role in facilitating seamless and efficient communication between various devices and software applications within robust SCADA systems. It acts as the vital bridge that enables data exchange and interoperability, ensuring smooth operations and streamlined information flow within the SCADA infrastructure. Without the presence of an OPC Server, the effectiveness and functionality of a SCADA system would be severely hindered.