OPC Protocol Is Used
OPC Protocol Is Used
The OPC protocol, an acronym for OLE for Process Control, has gained immense popularity and widespread adoption in numerous industries and applications. It is a highly regarded and extensively utilized communication standard that enables seamless data exchange between different systems and devices. Its versatility and reliability make it an indispensable tool for optimizing processes, streamlining operations, and ensuring efficient control in a myriad of industries across the globe. It is crucial to understand that the utilization of a standardized communication protocol is of utmost importance in enabling seamless interoperability between various devices and systems within the field of industrial automation. This protocol acts as a fundamental foundation, ensuring efficient and effective communication across diverse equipment and platforms. It eliminates any potential barriers or compatibility issues that may hinder the smooth operation of industrial automation systems, empowering them to work cohesively without any disruptions.
OPC Communication SCADA
OPC Communication, without a doubt, finds its application in numerous critical areas such as SCADA (Supervisory Control and Data Acquisition) systems. In these systems, OPC enables the seamless exchange of real-time data between a central server and remote devices or sensors. This efficient communication protocol ensures that crucial information is transmitted swiftly and accurately, enabling effective monitoring and control of various industrial processes. Its versatility makes it an indispensable tool for industries relying on real-time data acquisition and management. This feature allows for highly efficient monitoring and precise control of various industrial processes, empowering businesses to optimize their operations and enhance overall productivity. With the capability to closely observe and regulate every aspect of these processes, companies can ensure maximum efficiency, minimize errors, and achieve unparalleled levels of quality and precision.
OPC DA
OPC Data Access (OPC DA) is undeniably one of the most widely adopted and frequently encountered use cases of the OPC protocol. Its popularity stems from its ability to seamlessly facilitate data exchange between various industrial automation systems, making it an indispensable tool for efficient and reliable data communication. OPC DA not only simplifies complex data acquisition processes but also enables real-time monitoring and control, empowering industries to optimize their operations with utmost precision and effectiveness. It is worth noting that this remarkable OPC DA technology provides an efficient and reliable means to access real-time data from a multitude of sources, including the highly important Programmable Logic Controllers (PLCs), Distributed Control Systems (DCS), and other critical industrial devices. This capability empowers professionals to effortlessly gather crucial information for analysis and decision-making, ensuring streamlined operations and optimal performance in industrial settings.
SCADA Architecture
In the realm of SCADA (Supervisory Control and Data Acquisition) systems, client-server architectures play a crucial role in ensuring seamless connectivity between the SCADA software and the underlying hardware components. And when it comes to establishing this connectivity, OPC (OLE for Process Control) communication is often relied upon as a dependable solution. By leveraging OPC, SCADA systems achieve efficient and reliable data exchange, enabling real-time monitoring, control, and automation of industrial processes with utmost precision. This empowers organizations to gain a comprehensive understanding of their data within an industrial environment through effective visualization, meticulous control, and rigorous analysis. By harnessing the power of advanced technology, they are able to unlock valuable insights that drive strategic decision-making and optimize operations for maximum efficiency and productivity.
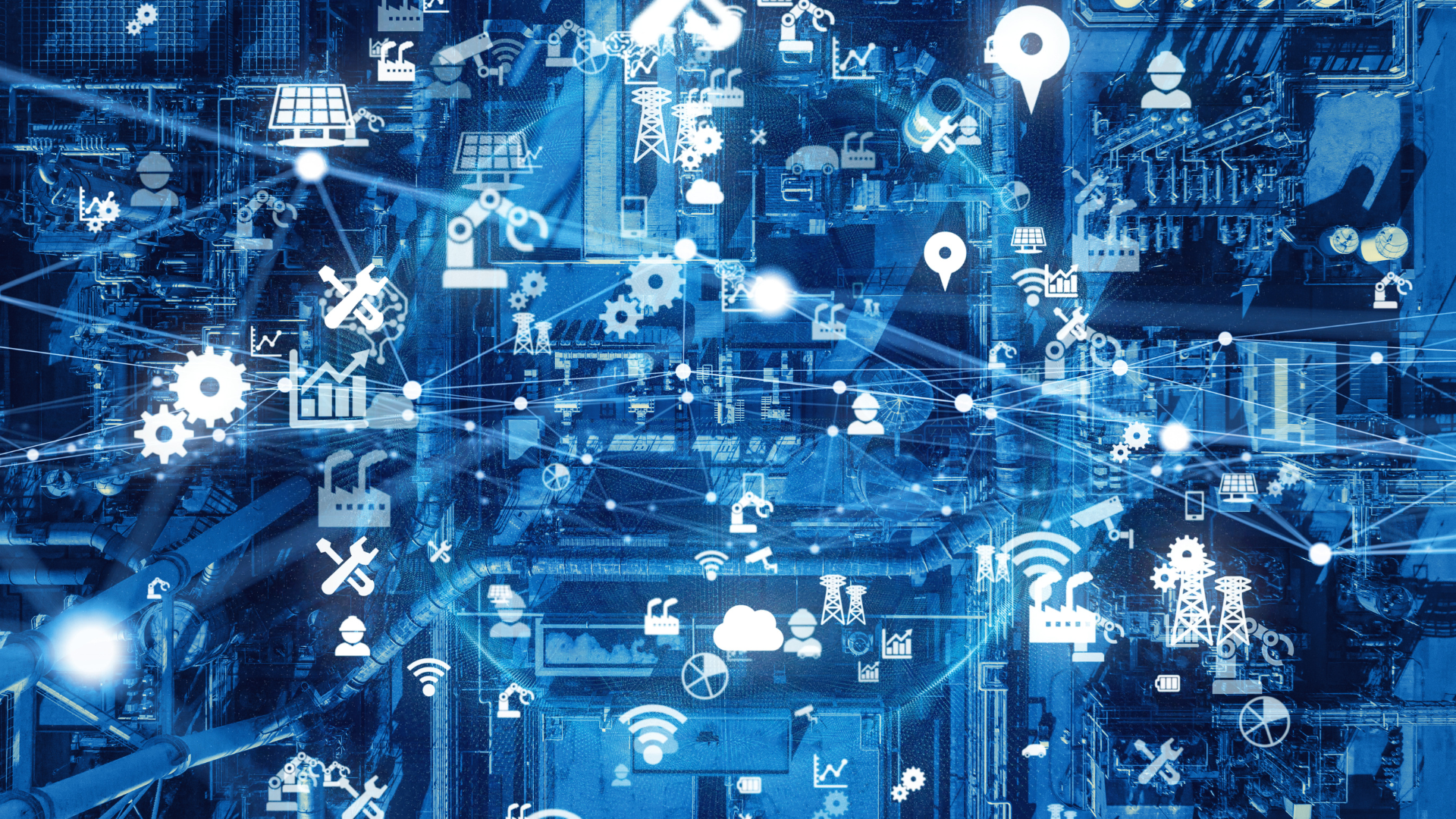
OPC Foundation
The OPC Foundation plays an absolutely crucial and indispensable role in tirelessly promoting and driving the widespread adoption and dynamic development of OPC standards. It is through their unwavering dedication and relentless efforts that these standards have gained significant traction in various industries, allowing for seamless interoperability, streamlined communication, and enhanced efficiency across diverse systems. The Foundation's influential leadership has undoubtedly propelled the OPC standards to become the gold standard in industrial automation, setting a benchmark that propels industries forward into a future of unparalleled connectivity and collaboration. They confidently and assertively provide comprehensive guidelines, industry-leading certification programs, and unwavering support to guarantee seamless compatibility among multiple vendors' diverse implementations.
In addition, it is worth mentioning that there are highly specialized software solutions available, such as Softing OPC Tunnel, which go above and beyond to ensure the secure transmission of OPC data over networks. These exceptional solutions prioritize the integrity and reliability of data, providing a trustworthy platform for seamless communication. It is crucial to emphasize that OPC comes in various versions, each specifically tailored to cater to different system requirements. For instance, there is "OPC Classic," which is designed to support older systems, and "OPC HDA," which specializes in accessing historical data. These distinct versions highlight the adaptability of OPC technology and its ability to meet the diverse needs of various industries and applications. No matter which version is utilized, the ultimate and unwavering objective remains resolute - to empower streamlined and highly efficient communication between a wide array of industrial devices by means of a universally recognized and standardized protocol.