Implementing Industry 4.0 technologies, which refers to the integration of advanced digital technologies in the manufacturing sector, can undoubtedly bring a multitude of benefits to businesses across various industries. By leveraging automation, data analytics, artificial intelligence, and Internet of Things (IoT), companies can optimize their operational processes, improve efficiency, and maximize productivity. Furthermore, Industry 4.0 technologies enable real-time monitoring and predictive maintenance, allowing businesses to identify and address issues proactively before they escalate into more significant problems. This not only minimizes downtime but also reduces costs associated with maintenance and unplanned disruptions. Additionally, the adoption of these cutting-edge technologies enables companies to gain deeper insights into their operations through data-driven decision making. By harnessing machine learning algorithms and advanced analytics tools, businesses can optimize their supply chain management strategies, streamline production processes, and enhance overall customer satisfaction. Ultimately, embracing Industry 4.0 technologies empowers businesses to stay competitive in an increasingly digital landscape while unlocking new opportunities for growth and innovation. These include increased productivity through automation and optimization of processes, improved quality control with real-time monitoring systems, enhanced flexibility to adapt to changing market demands, reduced costs through efficient resource utilization, and better decision-making based on data-driven insights.
What Are the Industry 4.0 Standards?
What Are the Industry 4.0 Standards?
Industry 4.0 technologies, often referred to as the fourth industrial revolution, represents a significant shift in various industries with the integration of advanced technologies and automation. This transformation involves the convergence of cutting-edge technologies such as artificial intelligence, Internet of Things (IoT), big data analytics, robotics, and cloud computing. These innovations are reshaping traditional manufacturing processes by creating smart factories that are more efficient, flexible, and interconnected. The adoption of Industry 4.0 enables businesses to optimize production processes, enhance product quality, reduce costs, and improve overall productivity levels. It also opens up new opportunities for customization and personalization while fostering innovation and sustainable growth in industries across the globe. It represents a significant shift in manufacturing and production processes, driven by digitalization and connectivity.
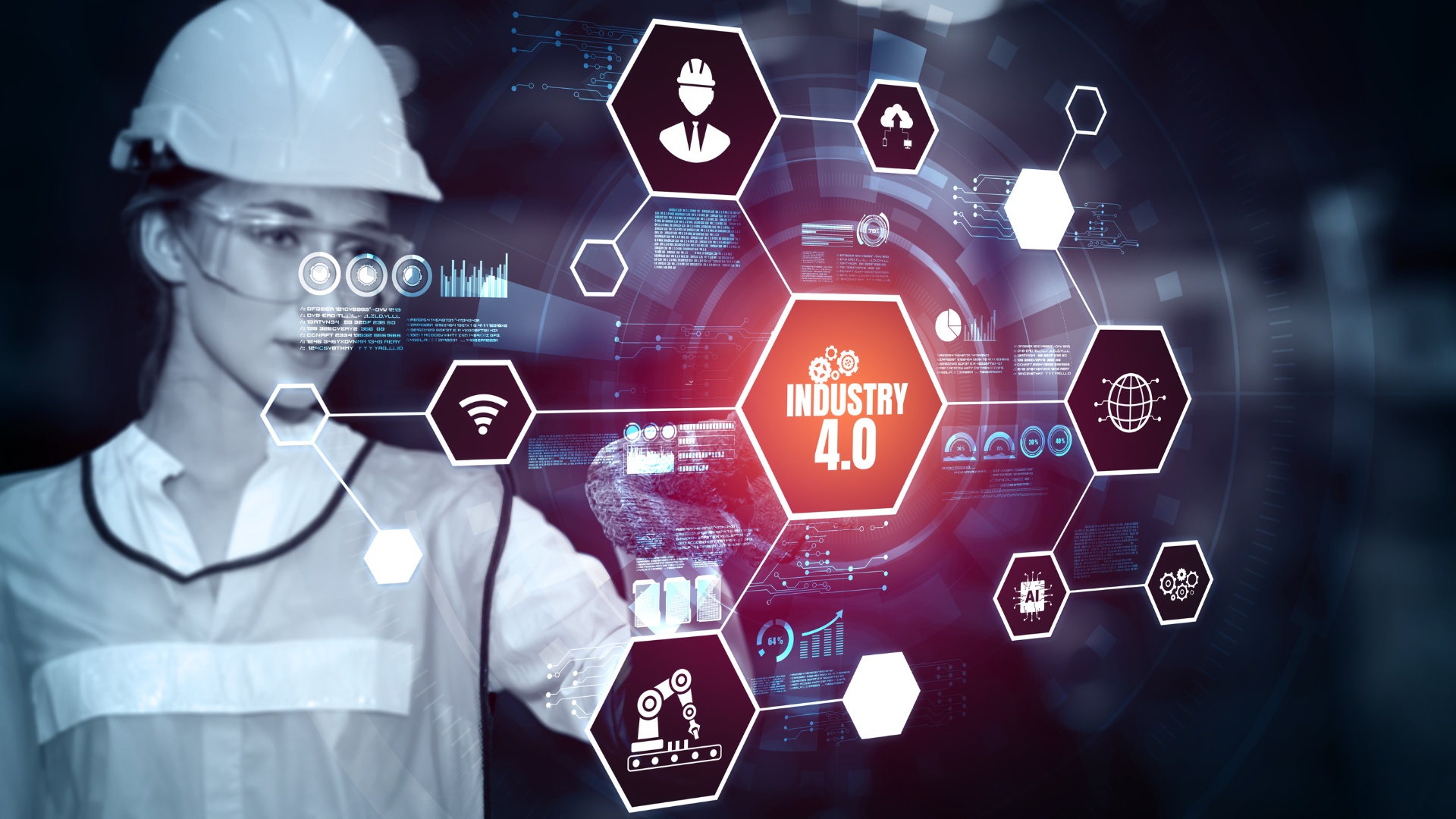
The widely recognized term "Industry 4.0" originated in Germany and has now gained significant global recognition. Coined by the German government, this term refers to the fourth industrial revolution, which emphasizes the integration of digital technologies into manufacturing processes. The concept behind Industry 4.0 revolves around the use of advanced technologies such as artificial intelligence, big data, internet of things (IoT), and robotics to enhance productivity, efficiency, and overall competitiveness in various industries worldwide. As a result, this transformative approach has captured the attention of businesses and policymakers across different countries who are keen to leverage these technological advancements for their economic growth and development strategies. It encompasses a range of technologies such as artificial intelligence (AI), internet of things (IoT), big data analytics, robotics, cloud computing, and more.
When discussing the revolutionary concept of Industry 4.0, it is crucial to highlight some of the cutting-edge technologies that are driving this transformation. One notable example is smart factories, which leverage interconnected machines capable of seamless communication and autonomous decision-making. These intelligent systems not only optimize production processes but also enhance overall efficiency and productivity. Another significant Industry 4.0 technology is predictive maintenance systems. By leveraging advanced data analytics techniques, these systems can analyze real-time data and predict potential equipment failures or maintenance requirements before they occur. This proactive approach allows for optimized maintenance schedules, minimizing downtime and maximizing operational efficiency. Furthermore, virtual reality (VR) simulations have emerged as a game-changer in the training arena within Industry 4.0. By creating immersive and interactive environments, VR simulations offer a safe and cost-effective way for employees to acquire hands-on experience in complex tasks or hazardous situations without any real-world risk. This technology has proven to be highly effective in enhancing training outcomes while reducing time and resources required for traditional training methods. Overall, these examples showcase how Industry 4.0 technologies are revolutionizing various aspects of manufacturing and beyond, enabling businesses to achieve greater levels of automation, efficiency, and innovation in our rapidly evolving digital landscape.
As we delve into the era of the fourth industrial revolution, it is crucial to weigh the advantages and disadvantages that accompany this transformative period. On one hand, the fourth industrial revolution brings forth unprecedented advancements in technology, such as artificial intelligence, robotics, and automation. These innovations have the potential to enhance productivity, efficiency, and convenience across various industries. By harnessing the power of AI and automation, businesses can streamline their operations and reduce human error. Tasks that were once time-consuming can now be automated, freeing up valuable resources and allowing employees to focus on more strategic endeavors. Additionally, AI-powered systems can analyze vast amounts of data at incredible speeds, enabling companies to make data-driven decisions with greater accuracy. However, it is imperative to acknowledge the potential drawbacks as well. As technology continues to evolve at a rapid pace during this revolution, concerns about job displacement arise. The fear that automation may replace human workers looms large for many individuals who rely on traditional employment. Furthermore, there are ethical considerations associated with emerging technologies like AI. Issues regarding privacy protection and data security must be addressed carefully to ensure that individuals' rights are safeguarded in this increasingly connected world. In summary, while the fourth industrial revolution holds immense promise for progress and innovation in various sectors of society, it is crucial to approach its benefits with a critical mindset. Balancing its advantages with potential challenges will enable us to navigate this new era responsibly and ensure equitable outcomes for all stakeholders involved. While Industry 4.0 offers immense potential for growth and innovation, it also raises concerns about job displacement due to automation and the need for upskilling or reskilling the workforce.
The fourth industrial revolution has had profound impacts that extend across numerous sectors. These sectors include manufacturing, healthcare, transportation, energy management, logistics, and many others. This revolution has brought about significant advancements in technology and automation, leading to increased efficiency and productivity in these industries. In manufacturing, for example, the implementation of smart technologies and robotics has revolutionized production processes, resulting in faster turnaround times and higher quality products. Similarly, in healthcare, the use of artificial intelligence and data analytics has improved patient care through personalized treatment plans and more accurate diagnostics. The transportation industry has also been transformed with the development of autonomous vehicles and smart infrastructure systems that enhance safety and optimize traffic flow. Furthermore, energy management has been greatly enhanced by leveraging IoT devices to monitor consumption patterns and optimize energy usage. As a result of these advancements brought forth by the fourth industrial revolution, we are witnessing an unprecedented level of interconnectedness between various sectors as they embrace innovative technologies to drive progress forward. The integration of advanced technologies enables increased efficiency in operations while transforming business models towards more customer-centric approaches.
If you are eager to explore the vast realm of Industry 4.0 standards and its profound impact on the manufacturing industry, you'll be pleased to know that a plethora of online resources exist that offer detailed and comprehensive information. Whether you prefer a concise PDF format or a wealth of specific examples and technologies, these resources are designed to provide insights into this ever-evolving subject matter. By delving into these materials, you will gain an in-depth understanding of the latest trends, advancements, and best practices within the Industry 4.0 landscape.