OPC UA (Unified Architecture) is not just a simple upgrade, but rather a powerful evolution of the OPC standard. It brings with it a wide range of benefits that significantly enhance the reliability and efficiency of industrial communication systems. One of the most notable advantages is its enhanced security features, which ensure that sensitive data remains protected from unauthorized access or malicious attacks. Additionally, OPC UA offers exceptional scalability, allowing businesses to seamlessly expand their operations without compromising performance. Furthermore, it promotes platform independence, enabling interoperability between different hardware and software platforms, thus eliminating compatibility issues that may arise in complex industrial environments. Overall, OPC UA is a game-changer in the world of industrial automation and sets new standards for secure and efficient communication protocols. It empowers and guarantees secure communication over a wide range of network protocols such as Ethernet and TCP/IP. With its robust encryption capabilities, it ensures that sensitive information remains confidential and protected from any potential threats or unauthorized access. By implementing state-of-the-art security measures, it fortifies the integrity of data transmission, making it an indispensable tool for organizations seeking to maintain a strong and impenetrable network infrastructure.
What Is the Main Purpose of OPC
What Is the Main Purpose of OPC
The primary objective of OPC (OLE for Process Control), without a doubt, is to empower seamless and efficient OPC communication among various devices and systems within the realm of industrial automation. This groundbreaking technology serves as a vital facilitator, ensuring that the exchange of data and information between different components is swift, seamless, and error-free. By streamlining interconnectivity, OPC plays a pivotal role in enhancing productivity, optimizing processes, and promoting harmonious collaboration across the industrial landscape. OPC, which stands for OLE (Object Linking and Embedding) for Process Control, is not just any protocol - it is the industry-standard protocol that confidently ensures seamless data exchange and unmatched interoperability between a wide range of hardware and software components. With OPC, you can effortlessly facilitate communication between different systems, devices, and applications with utmost reliability and efficiency. This powerful protocol empowers industries to streamline their operations, enhance productivity, and achieve unprecedented levels of connectivity across their entire infrastructure.
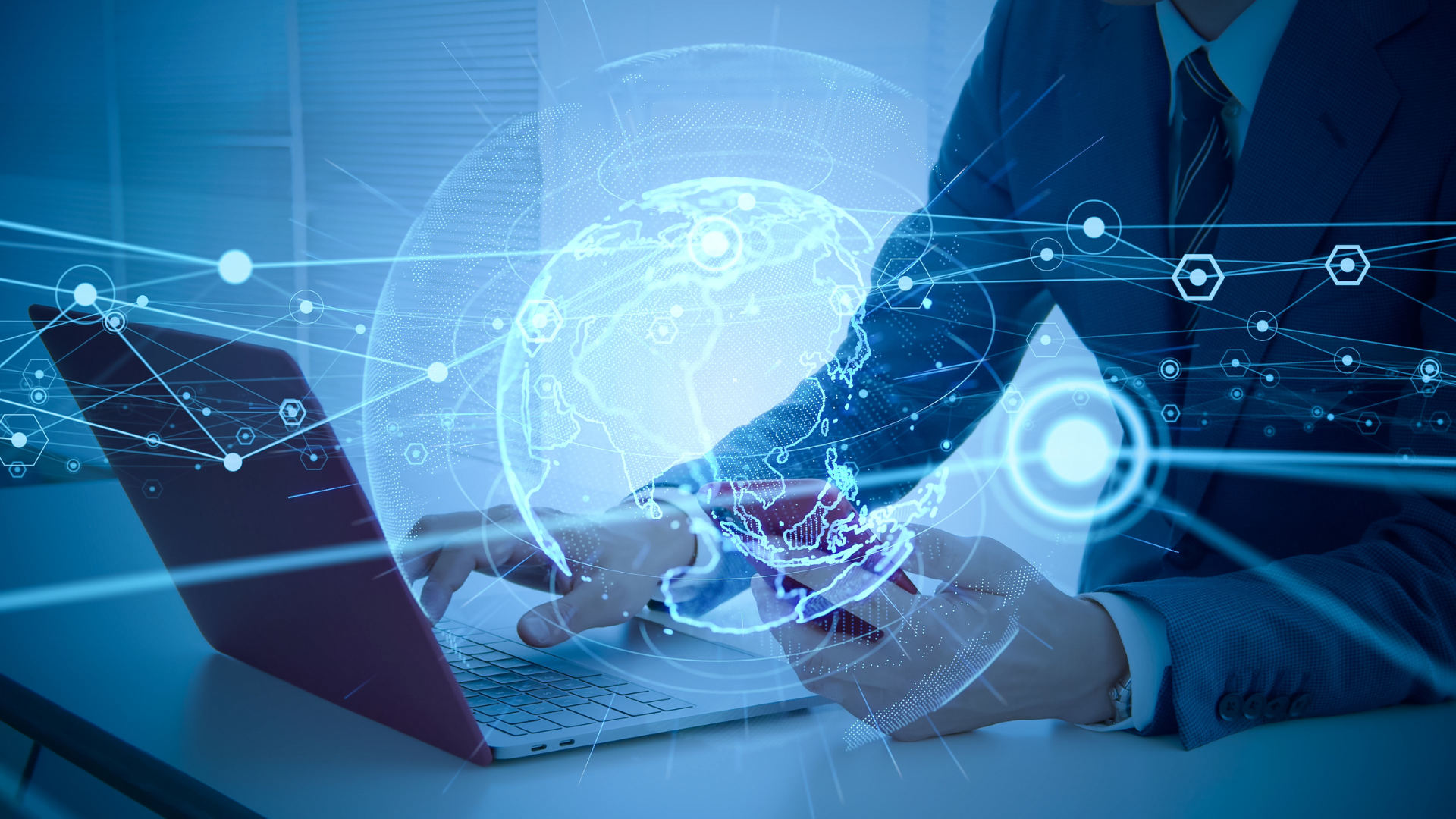
OPC Stands For
OPC, which stands for OLE for Process Control, is a powerful acronym that should not be overlooked. The abbreviation OLE itself refers to Object Linking and Embedding, which is a technology that facilitates seamless data transfer between various applications. What makes OPC truly remarkable is its ability to bridge the gap between different programming languages and platforms. This means that regardless of the software environment you find yourself in, OPC ensures smooth and efficient communication between applications, enabling the exchange of vital data with ease and precision.
OPC Servers
OPC servers undeniably play an absolutely crucial role in the overarching OPC architecture. They serve as the backbone and foundation, enabling seamless communication and data exchange between various devices, systems, and applications. Without these indispensable components, the entire OPC infrastructure would simply cease to function effectively. Thus, it is imperative to recognize and appreciate the pivotal significance of OPC servers in driving the flawless operation of the OPC architecture. These OPC Servers play a crucial role as efficient intermediaries, seamlessly collecting vast amounts of data from diverse sources including sensors, machines, and databases. They excel at their job by effortlessly making this valuable data readily available to client applications through well-designed and standardized interfaces.
OPC UA
Open Source OPC
Open source OPC servers, without a doubt, offer unparalleled flexibility and cost-effectiveness. Unlike their commercial counterparts, they grant users the freedom to modify the source code to match their unique and specific requirements. This level of customization empowers businesses to tailor their OPC servers precisely as needed, resulting in optimized performance and seamless integration within industrial automation systems. By choosing open-source solutions, organizations can not only avoid the hefty price tags associated with commercial alternatives but also ensure reliable communication at all times. With open source OPC servers at their disposal, businesses can confidently embrace efficient and affordable solutions for their industrial automation needs.
Free OPC Server Simulators
Free OPC server simulators are incredibly valuable tools for engineers involved in testing and development activities. These simulators, which can be obtained at no cost, play a crucial role in emulating the behavior of actual OPC servers. With their ability to replicate the functionalities of real OPC servers without the need for physical devices, these simulators empower engineers to thoroughly validate their applications before deploying them in real-world scenarios. This not only saves time but also ensures that the applications are robust and error-free, leading to enhanced performance and streamlined operations.
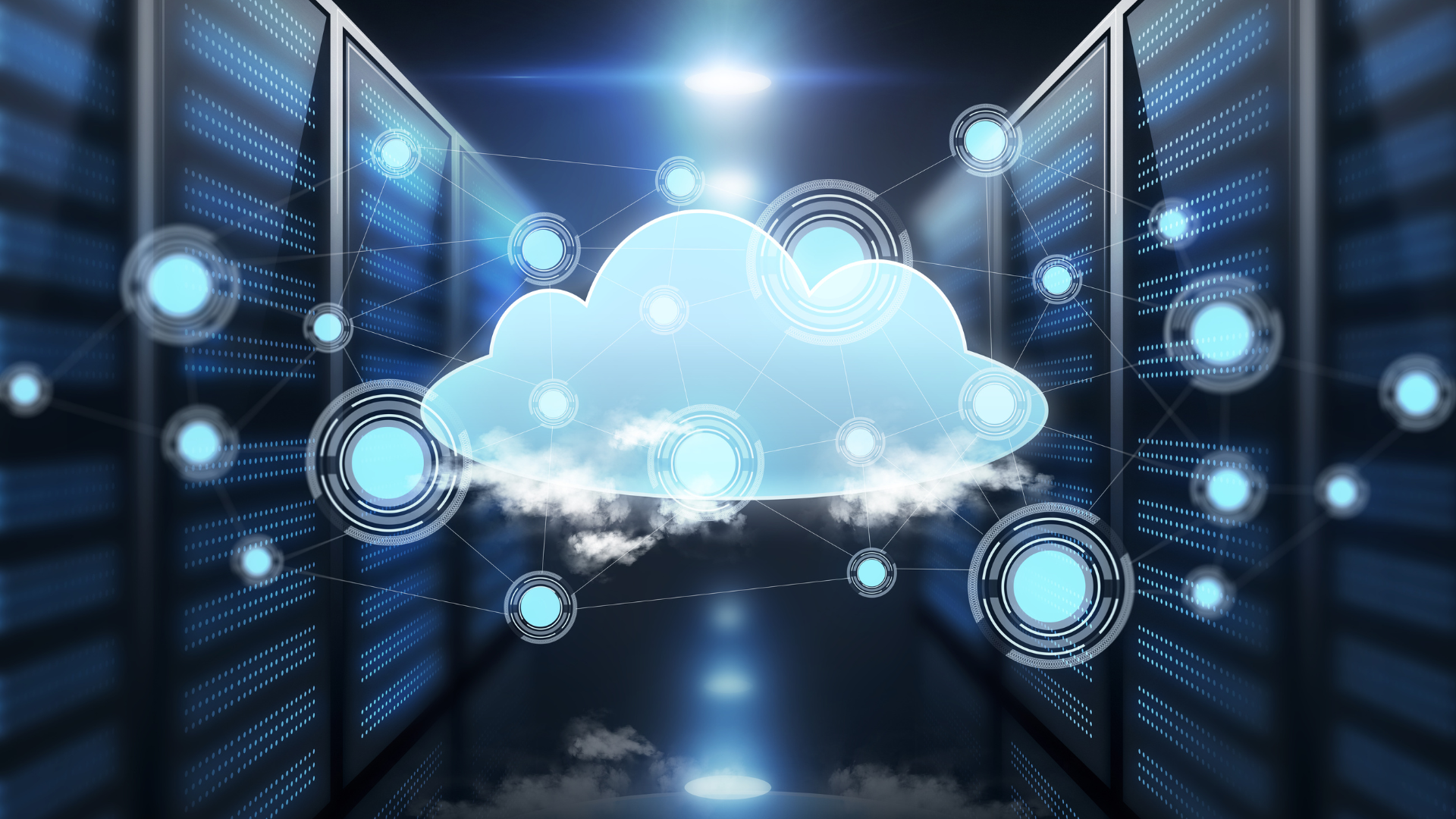
TIA Portal OPC
The TIA Portal OPC UA server, an exceptional feature included in Siemens' highly acclaimed TIA (Totally Integrated Automation) Portal software suite, empowers users with seamless integration capabilities. This remarkable server enables effortless connectivity and collaboration with various systems by leveraging the powerful OPC UA protocol, making it a game-changer for businesses across industries.
NI (National Instruments) OPC
The highly efficient and reliable NI (National Instruments) OPC server plays a crucial role in facilitating seamless connectivity between NI hardware devices and third-party software applications. By leveraging the power of the OPC standard, it empowers users to effortlessly access and utilize measurement data from NI instruments. This remarkable solution not only ensures compatibility but also enables easy integration with common industrial protocols, making it a game-changer for industries reliant on accurate and timely data acquisition.
OPC Protocol
In summary, the OPC protocol is an indispensable and essential standardized framework that plays a crucial role in facilitating efficient and reliable communication within industrial automation systems. It serves as the backbone for seamlessly integrating a wide range of devices and applications, ensuring a harmonious and synchronized operation throughout the entire system. This protocol is indispensable for achieving optimal performance, precision, and productivity in industrial settings.