Where is OPC Server Used?
Where is OPC Server Used?
OPC servers unquestionably play a paramount role in the vast realm of SCADA systems and industrial automation. They are essential components that facilitate seamless communication between different devices, sensors, and software applications within these complex systems. Without OPC SCADA servers, the efficiency and effectiveness of industrial processes would be severely compromised. Their significance cannot be overstated as they enable real-time data exchange, ensure robust connectivity, and empower operators to monitor and control operations with utmost precision. In short, OPC servers are the backbone of SCADA systems and industrial automation, indispensably contributing to their smooth functioning and optimal performance. They play a crucial role as a powerful bridge connecting and integrating various devices, software applications, and data sources within the industrial environment. With their advanced capabilities, they seamlessly facilitate smooth communication and interoperability between different components, ensuring efficient data exchange and streamlined workflows. Their presence not only enhances productivity but also strengthens the overall connectivity infrastructure of the industrial ecosystem.
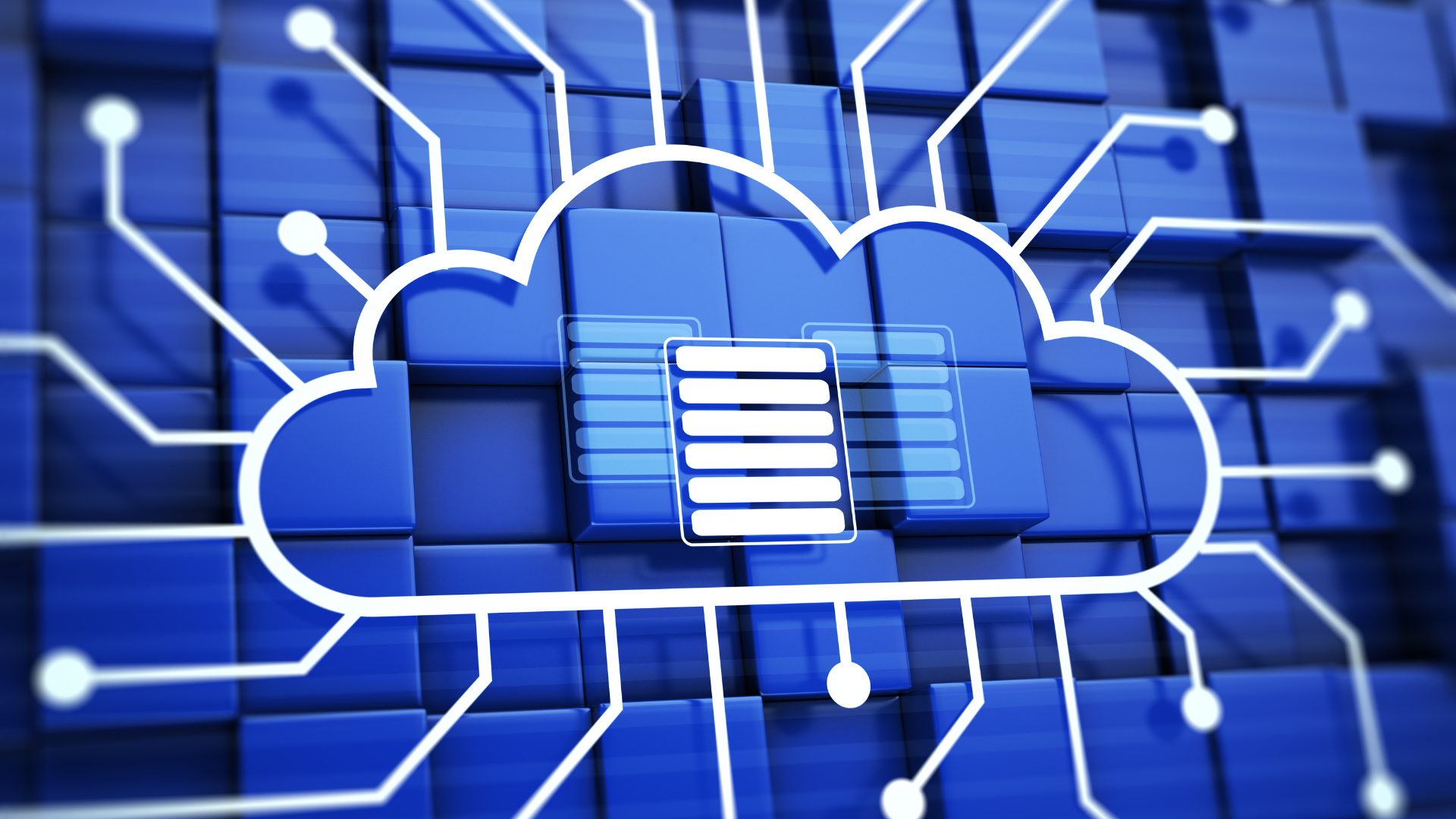
An OPC server, without a doubt, serves as the absolute central hub that effectively collects and delivers real-time data from an extensive range of hardware devices. These include, but are certainly not limited to, highly crucial components such as sensors, PLCs (Programmable Logic Controllers), and various other industrial equipment. Its pivotal role in seamlessly integrating and synchronizing these devices cannot be overstated as it ensures smooth operations and enables efficient decision-making processes. The valuable data obtained is seamlessly made accessible to OPC clients or software applications, empowering them to efficiently utilize it for a wide range of critical purposes such as real-time monitoring, precise control, in-depth analysis, and visually stunning visualization. This ensures that every bit of information is harnessed to its fullest potential, enabling businesses to make informed decisions and drive remarkable outcomes.
OPC client software plays a crucial role in establishing a seamless connection between users and OPC servers. By harnessing the power of this software, users gain the ability to effortlessly retrieve the precise data they need from OPC servers. This efficient tool empowers users to interact with OPC servers by effortlessly requesting specific information or even performing actions based on the data available, thereby enhancing their overall productivity and efficiency.
The architecture of an OPC server-client system is expertly designed to facilitate seamless communication between various components within an industrial network. This well-thought-out structure ensures that information flows effortlessly, enabling efficient data exchange and synchronization among the different elements of the network. With this robust system in place, the connectivity between servers and clients is both reliable and consistent, guaranteeing uninterrupted communication within the industrial network at all times. The client-server model is an essential framework that guarantees efficient and streamlined data exchange while simultaneously upholding the utmost security and reliability standards. It is a tried-and-true approach that facilitates seamless communication between clients and servers, ensuring that information is transmitted swiftly and without any compromise to its integrity. By adhering to this model, organizations can rest assured knowing that their data remains protected and accessible at all times, while also enjoying the peace of mind that comes with a robust and dependable system in place.
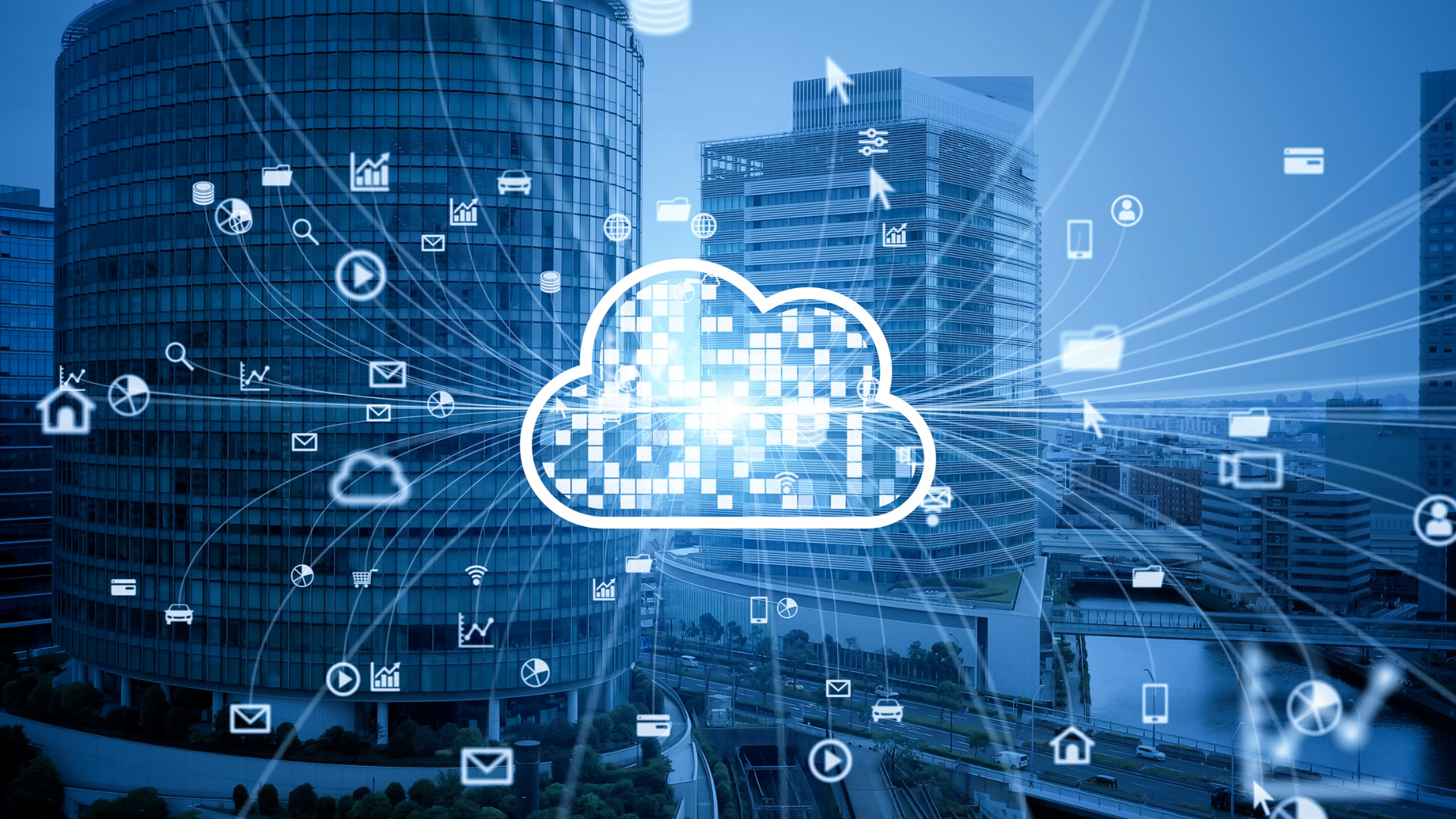
When it comes to specific use cases of OPC servers, it is an undisputed fact that they are extensively employed in various industries such as manufacturing, oil and gas, energy management, pharmaceuticals, water treatment plants, and numerous others. Their utilization in these sectors is not only widespread but also crucial for ensuring optimal operations and seamless data exchange. These OPC Servers empower users with the remarkable ability to monitor processes in real-time, granting them unprecedented control over various tasks. Additionally, they offer invaluable functionalities such as remote-control capabilities that allow users to effortlessly manage operations from anywhere, at any time. Moreover, these intelligent systems facilitate the collection of historical data, which can be leveraged for comprehensive analysis and informed decision-making. Furthermore, their seamless integration with other systems amplifies their utility and ensures a streamlined workflow throughout the organization.
The market is flooded with a myriad of OPC servers, each designed to cater to specific industrial protocols and adhere to manufacturers' standards. These diverse offerings ensure that businesses can find the perfect OPC server that seamlessly integrates with their existing infrastructure, allowing for efficient data exchange and streamlined operations. With such a wide selection available, companies can confidently choose an OPC server that aligns perfectly with their unique requirements, eliminating any compatibility issues and maximizing productivity. Siemens, a renowned industry leader, not only offers automation systems but also provides its own highly specialized OPC server software. This software has been meticulously designed to perfectly align with their automation systems, ensuring seamless integration and optimal performance. By utilizing Siemens' dedicated OPC server software, businesses can enhance operational efficiency and streamline their automation processes to achieve maximum productivity and accuracy.
Matrikon, a highly reputable and well-established player in the industry, stands out as a leading provider of OPC server solutions. Their offerings not only support multiple protocols but also boast an impressive array of configuration options that cater to the diverse needs and requirements of businesses. With Matrikon as your chosen solution provider, you can confidently rely on their robust technology to seamlessly integrate different systems and enhance overall operational efficiency.
In conclusion, it is imperative to recognize that the utilization of an OPC server is absolutely crucial when it comes to collecting real-time data from a multitude of devices or integrating your SCADA system with other software applications. With its seamless connectivity and efficient operation capabilities, an OPC server serves as a vital component within your industrial environment, enabling you to achieve optimal performance and productivity.