Industry 4.0 In Manufacturing
Industry 4.0 In Manufacturing
Industry 4.0, often referred to as the Fourth Industrial Revolution, is an all-encompassing term that describes the ongoing transformation of the manufacturing industry through the integration of advanced technologies and automation into production processes. This revolutionary shift is expected to have a profound impact on various sectors, including manufacturing and supply chain management. The incorporation of cutting-edge technologies such as Artificial Intelligence (AI), Internet of Things (IoT), robotics, big data analytics, and cloud computing has enabled manufacturers to optimize their operations and achieve unprecedented levels of efficiency. By leveraging these advanced tools, companies can enhance productivity, reduce costs, minimize errors, and improve overall product quality. One of the key driving forces behind Industry 4.0 is the concept of smart factories. These factories utilize interconnected systems that enable real-time communication between machines and humans. Through this seamless integration, manufacturers can monitor production processes in real-time and respond swiftly to any issues or bottlenecks that may arise. Automation plays a pivotal role in Industry 4.0 by streamlining repetitive tasks traditionally performed by human workers. This not only frees up valuable time for employees to focus on more complex and creative endeavors but also reduces the risk of human error. Furthermore, Industry 4.0 enables manufacturers to embrace a more customer-centric approach by leveraging data-driven insights throughout the entire value chain. By analyzing vast amounts of data collected from various sources such as sensors embedded in machines or customer feedback systems, companies can gain valuable insights into consumer preferences and behaviors. This allows for personalized product offerings and tailored customer experiences. In conclusion, Industry 4.0 represents a paradigm shift in manufacturing by harnessing advanced technologies like AI and automation to drive efficiency, productivity gains, cost reduction while fostering innovation across all aspects of production processes.
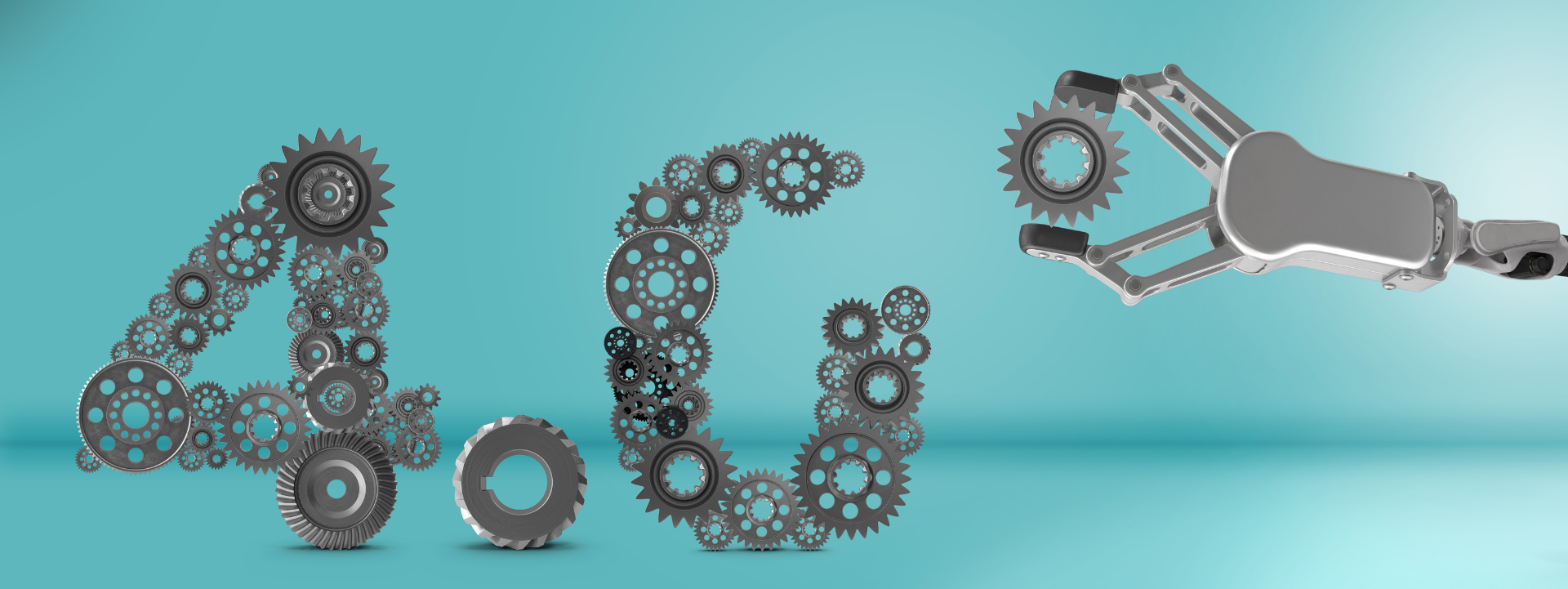
What Is Industry 4.0 Meaning
Industry 4.0 represents the integration of cyber-physical systems, the Internet of Things (IoT), and cloud computing into manufacturing. It's the current trend of automation and data exchange in manufacturing technologies, shaping the future of production. This revolution not only enhances operational efficiency but also drives innovation by connecting physical machinery with digital networks for improved analysis and forecasting. These interconnected systems allow for more responsive and flexible production processes, making manufacturing smarter and more adaptable to changing market demands. As a result, Industry 4.0 is fundamentally altering the landscape of industrial production, paving the way for more efficient and sustainable manufacturing practices.
Industry 4.0 Meaning PDF
Detailed guides and PDFs provide comprehensive insights into Industry 4.0, explaining how it revolutionizes manufacturing by integrating digital and physical systems to enhance connectivity and automation. These resources help stakeholders understand the key concepts and benefits, equipping them with the knowledge to implement these technologies effectively. They serve as essential tools for educators, industry professionals, and policymakers looking to navigate the complexities of this technological shift.
Industry 3.0 Meaning
Industry 3.0 was characterized by the introduction of computers and automation into manufacturing, setting the foundation for the smart automation processes that define Industry 4.0. This era marked a significant transformation from mechanical and analog systems to digital technology, radically changing how products were made and services delivered. The shift paved the way for increased efficiency and customization, preparing the industry for the next wave of digital integration.
Industry 5.0 Meaning
Industry 5.0 builds on the technological advances of Industry 4.0, focusing on the collaboration between humans and robots. It emphasizes personalized production, sustainability, and enhancing human capabilities with AI support. This next evolutionary phase aims to combine the creativity and problem-solving abilities of humans with the precision and efficiency of machines, fostering a more human-centric approach to industrial production.
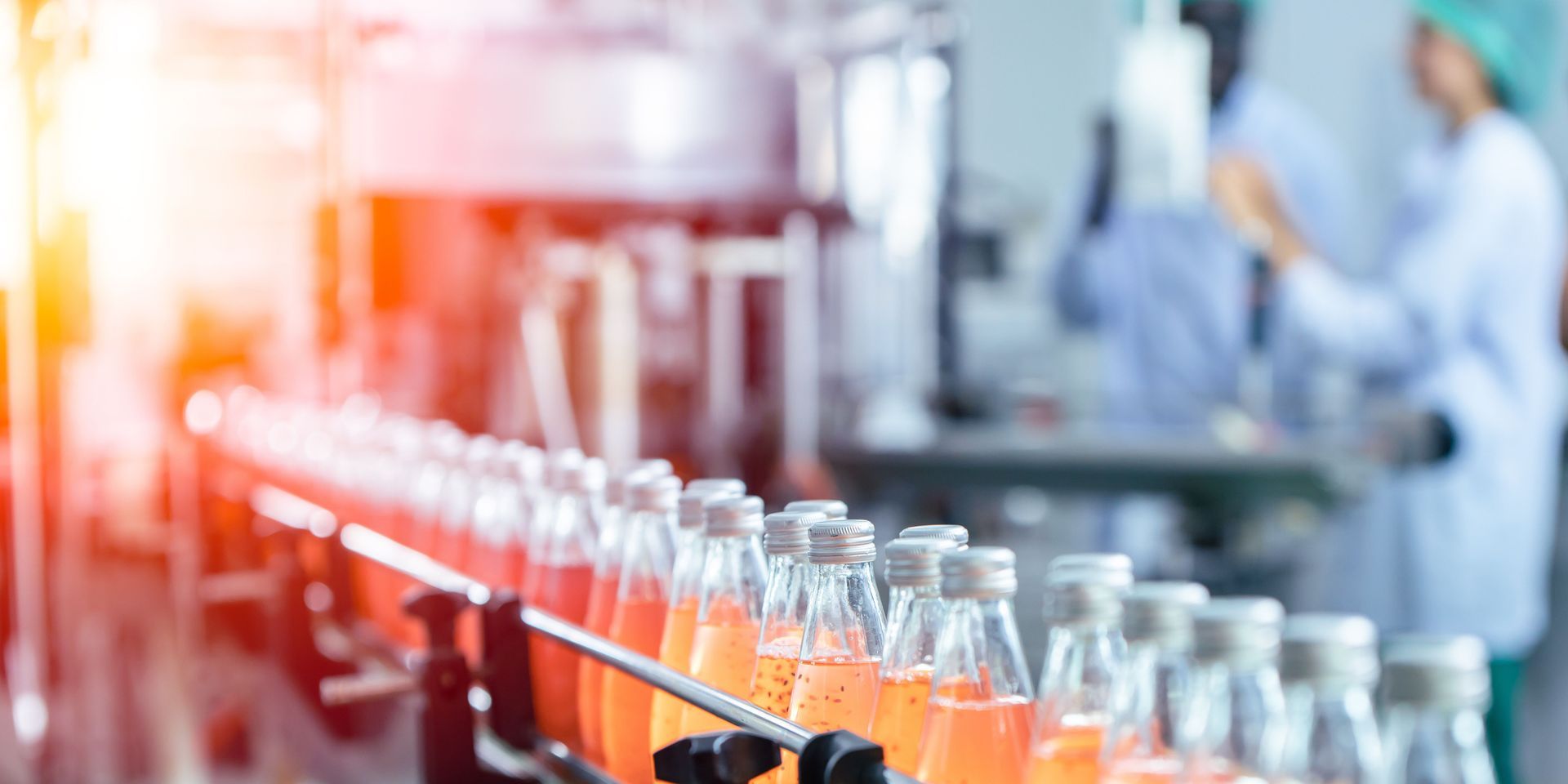
How Does Industry 4.0 Affect Manufacturing
Industry 4.0 introduces smart technologies that transform traditional manufacturing processes, making them more efficient and adaptable. By embedding systems with sensors and connectivity, manufacturers can now monitor and adjust processes in real-time, greatly increasing productivity. This adaptability also allows for more personalized manufacturing, meeting customer demands with greater precision. Additionally, the data-driven nature of Industry 4.0 enables predictive maintenance, reducing downtime and associated costs. Overall, these advancements foster a more responsive and sustainable manufacturing environment.
Industry 4.0 Technologies in Manufacturing
Technologies such as IoT, AI, and robotics are central to Industry 4.0, enhancing manufacturing by optimizing production lines and improving real-time decision-making. These technologies facilitate seamless communication between machines, which is vital for automating complex manufacturing processes. The integration of these smart technologies leads to improved efficiency and greater innovation capabilities within factories.
Importance of Industry 4.0 in Manufacturing
The strategic adoption of Industry 4.0 technologies is crucial for maintaining competitiveness in today's global market. It enables manufacturers to achieve higher efficiency and lower costs, while also providing the agility to quickly respond to market changes and customer needs. Embracing these technologies helps businesses stay ahead in a rapidly evolving industrial landscape.
Industry 4.0 in Manufacturing PDF
Industry-specific PDFs outline practical implementations of Industry 4.0, providing blueprints for integrating new technologies into existing manufacturing systems. These documents serve as a vital resource for companies looking to undertake digital transformations, offering detailed guidance and case studies. They are instrumental in helping manufacturers visualize potential impacts and plan strategic implementations effectively.
What Is an Example of Industry 4.0 in Manufacturing
Examples of Industry 4.0 are evident in smart factories where advanced sensors and Internet of Things (IoT) devices ensure efficient production processes. These technologies enable factories to operate with minimal human intervention, using data from sensors to optimize operations and increase output. The use of IoT not only boosts efficiency but also enhances the quality of products by providing continuous feedback loops for quality control. Additionally, the integration of AI with machine learning algorithms predicts maintenance needs, thereby minimizing downtime and extending the life of machinery. Such implementations illustrate how Industry 4.0 technologies are reshaping the manufacturing landscape.
Industry 4.0 Manufacturing Examples
From real-time monitoring of equipment to automated adjustments, examples like predictive maintenance and smart logistics illustrate the practical benefits of Industry 4.0. These advancements allow for greater operational flexibility and more efficient use of resources, reducing waste and improving overall factory performance. The continuous data flow from connected devices provides a comprehensive view of production activities, enabling timely decisions and adjustments.
Industry 4.0 in Manufacturing
Industry 4.0 has revolutionized manufacturing by integrating advanced technologies like IoT, AI, and robotics, which enhance operational efficiency and flexibility. This integration allows for more precise control over manufacturing processes, leading to higher productivity and reduced operational costs. As a result, manufacturers can better adapt to market changes and customer demands, making the sector more dynamic and competitive.
Industry 4.0 Company Example
Companies like Siemens and General Electric demonstrate advanced Industry 4.0 applications, showcasing highly automated and interconnected manufacturing environments. These companies leverage digital twins to simulate and optimize processes before actual physical production begins, enhancing efficiency and reducing the risk of error. Their adoption of Industry 4.0 technologies sets a benchmark for others in the industry, proving the value of digital transformation.
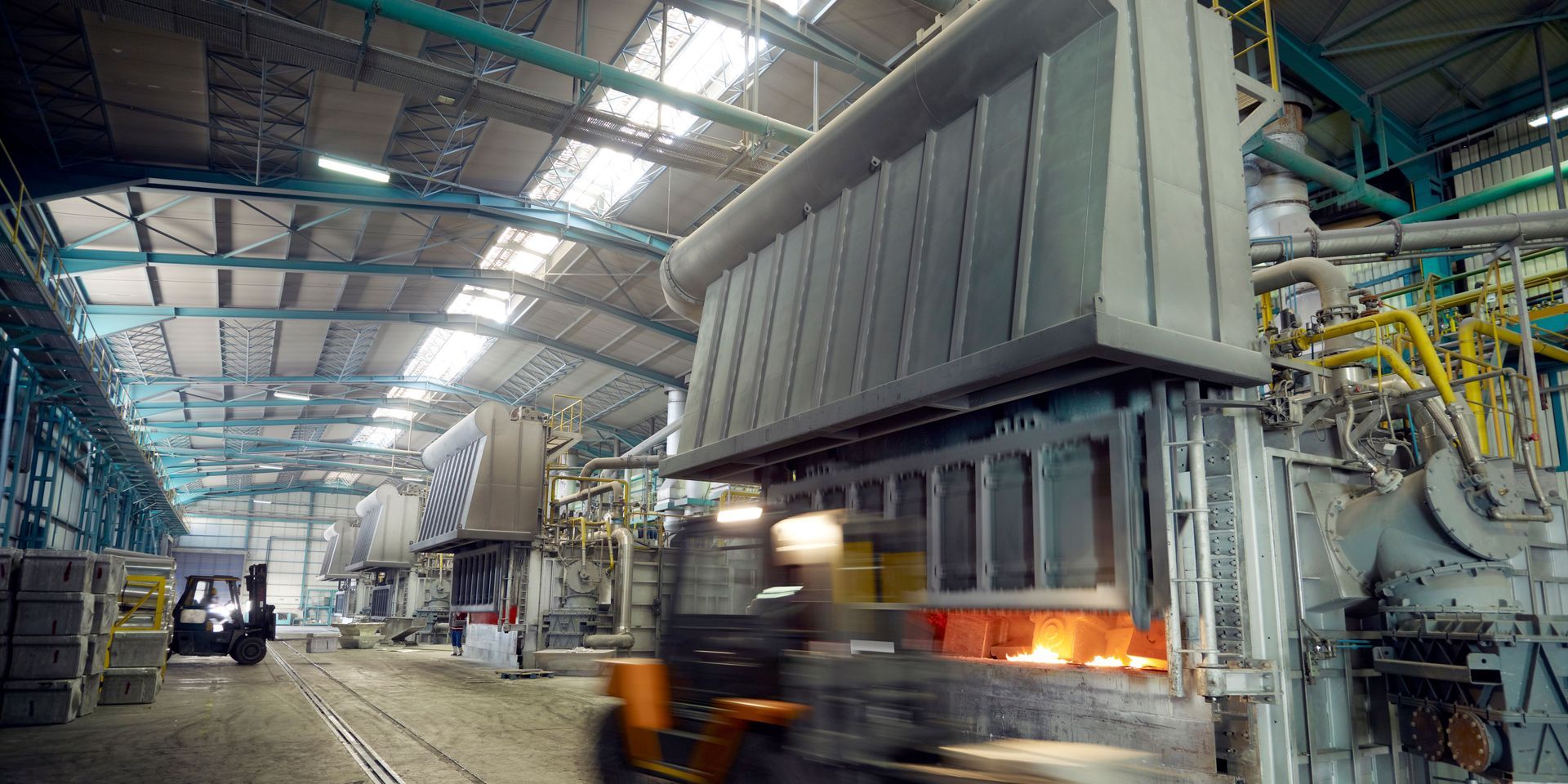
How to Implement Industry 4.0 in Manufacturing Industry
Implementing Industry 4.0 in the manufacturing industry involves a strategic overhaul of existing systems and processes to incorporate advanced digital technologies. First, manufacturers need to assess their current infrastructure and identify areas where IoT, AI, and automation can be integrated to optimize efficiency. Training programs should be initiated to upskill employees, ensuring they are capable of operating new technologies effectively. Collaboration with technology providers is essential to customize solutions that fit specific manufacturing needs. Finally, continuous monitoring and adaptation are key, as feedback from these systems will guide further improvements and innovations.
Industry 4.0 PPT
Presentations on Industry 4.0, particularly PowerPoint slides, are valuable tools for explaining the complexities and steps necessary for implementation in manufacturing. These presentations can outline key technologies, implementation strategies, and case studies, providing a visual and informative guide for stakeholders. They serve as an educational resource to facilitate understanding and drive strategic planning.
Industry 4.0 Benefits
The benefits of adopting Industry 4.0 technologies in manufacturing are substantial, including increased operational efficiency, reduced costs, and enhanced product quality. These technologies enable real-time data analysis and machine learning capabilities that improve decision-making and process optimization. Additionally, Industry 4.0 fosters greater flexibility and agility in manufacturing, allowing companies to respond quickly to market changes and customer demands.
Industry 5.0 Technologies
Industry 5.0 technologies focus on the integration of human ingenuity with advanced technological capabilities. This next evolution emphasizes personalized production, sustainability, and the enhancement of worker skills through collaboration with smart machines. Industry 5.0 aims to create more humane technology interactions, promoting a balance between automated efficiency and skilled human creativity.
What Does Industries 4.0 Mean
Industries 4.0 refers to a significant transformation in the manufacturing sector through the integration of digital technologies like IoT (Internet of Things), Artificial Intelligence, and robotics. This evolution is characterized by smart factories that leverage interconnected systems to automate and optimize production processes. The essence of Industries 4.0 lies in its ability to enhance operational efficiency, product quality, and innovation, significantly impacting how industries operate and deliver value. By enabling real-time data analysis and machine-to-machine communication, Industries 4.0 allows manufacturers to detect and address issues instantly, improving productivity and reducing waste. Furthermore, this technological shift is driving a more sustainable manufacturing approach, enabling industries to meet environmental and regulatory standards more effectively.
Industry 4.0 Technologies Meaning
The term "Industry 4.0 technologies" refers to the array of digital tools that facilitate the transformation of manufacturing operations. These include IoT (Internet of Things), Artificial Intelligence, machine learning, and robotics, which collectively work to automate tasks and provide deep analytical insights. Understanding these technologies is essential for industries aiming to leverage them for improved productivity and competitiveness.
Digital Transformation in Manufacturing McKinsey
McKinsey's insights on digital transformation in manufacturing emphasize the strategic integration of digital technology into all facets of a business. This transformation is not just about adopting new technologies but also about fundamentally changing how companies operate and deliver value, driven by the need to increase efficiency and adapt to new consumer demands. McKinsey provides a roadmap for industries to navigate this complex landscape, ensuring successful digital adoption and transformation.
Industry 4.0 Technologies PDF
PDF documents detailing Industry 4.0 technologies offer comprehensive guides on how these digital innovations can be applied effectively in the manufacturing sector. These documents serve as invaluable resources for industry leaders and professionals, providing detailed explanations, step-by-step implementation strategies, and case studies. They are crucial for any organization looking to understand and harness the potential of Industry 4.0 technologies for their operations.
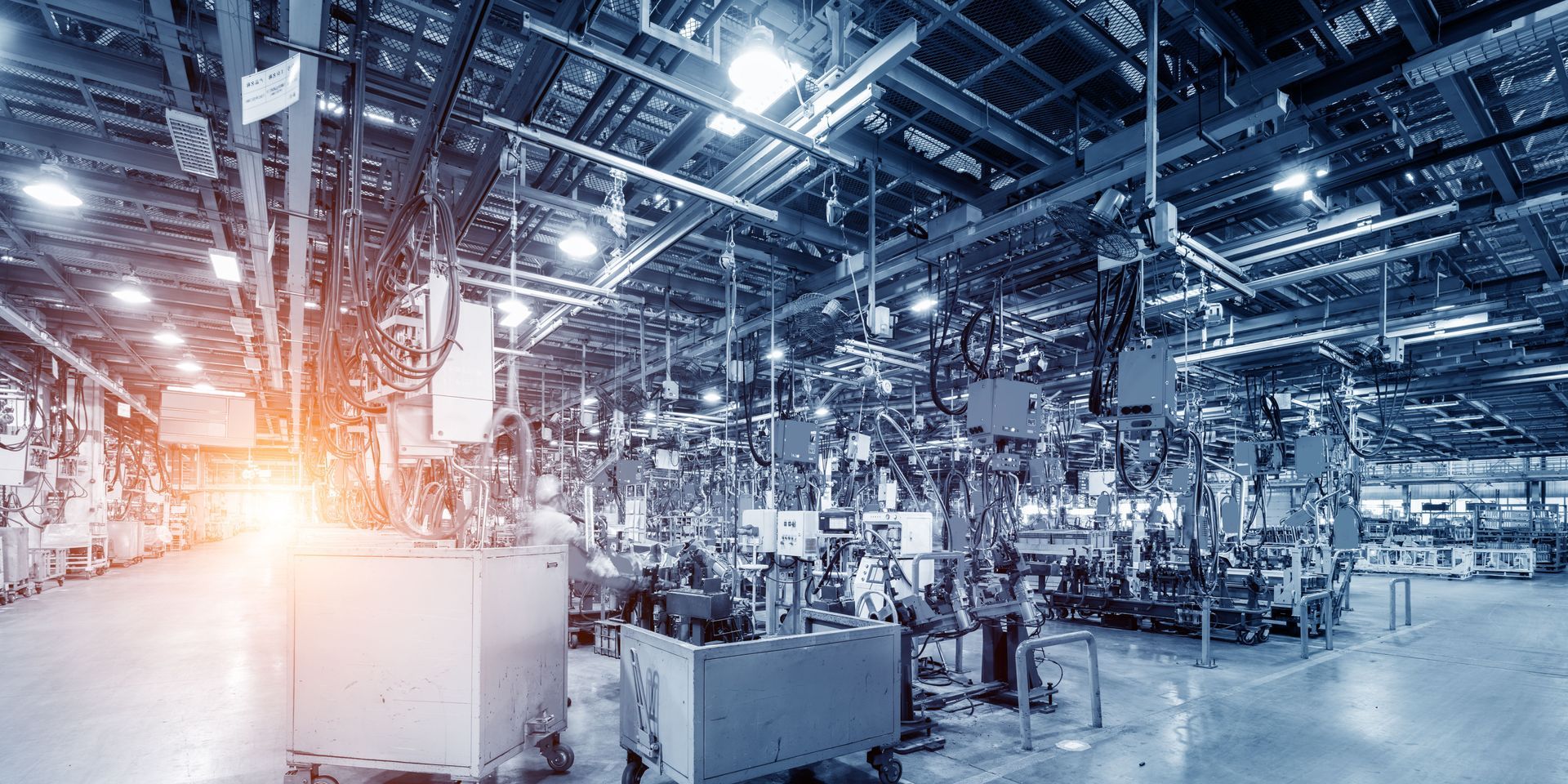
What Is Industry 4.0 Examples
Industry 4.0 examples showcase the practical implementation of advanced digital technologies in manufacturing settings to enhance efficiency and productivity. One prominent example is the use of smart sensors in factories that continuously collect and analyze data to optimize operations. Another example is the deployment of AI-driven predictive maintenance systems that forecast equipment failures before they occur, minimizing downtime. In logistics, Industry 4.0 is exemplified by automated warehouses where robots and automated guided vehicles streamline the movement of goods. These examples demonstrate how Industry 4.0 technologies integrate seamlessly to transform traditional manufacturing into highly efficient, data-driven operations.
Digital Transformation in Manufacturing Industry Examples
Digital transformation in the manufacturing industry is vividly illustrated by factories that integrate IoT (Internet of Things) systems for real-time monitoring and control of production lines. For instance, manufacturers are using digital twins to create virtual models of physical systems, which helps in optimizing machine performance and product quality. These transformations are not just about technology but also involve rethinking operational processes to fully capitalize on digital data.
Industry 4.0 Examples in Automotive Manufacturing
In automotive manufacturing, Industry 4.0 has led to significant innovations such as the integration of IoT (Internet of Things) devices to track and analyze every step of the assembly line. This allows for real-time quality control and immediate correction of manufacturing issues. The use of collaborative robots (cobots) working alongside human workers to enhance efficiency and safety is another key example of Industry 4.0 in action in this sector.
Industry 4.0 Technologies Examples
Examples of Industry 4.0 technologies in action include the use of IoT (Internet of Things) for equipment monitoring, AI for quality inspection, and blockchain for enhancing supply chain transparency. These technologies are employed across various industries to not only improve operational efficiency but also to provide greater traceability and security. Advanced analytics and machine learning are further utilized to interpret the vast amounts of data generated, leading to more informed decision-making and strategic planning.
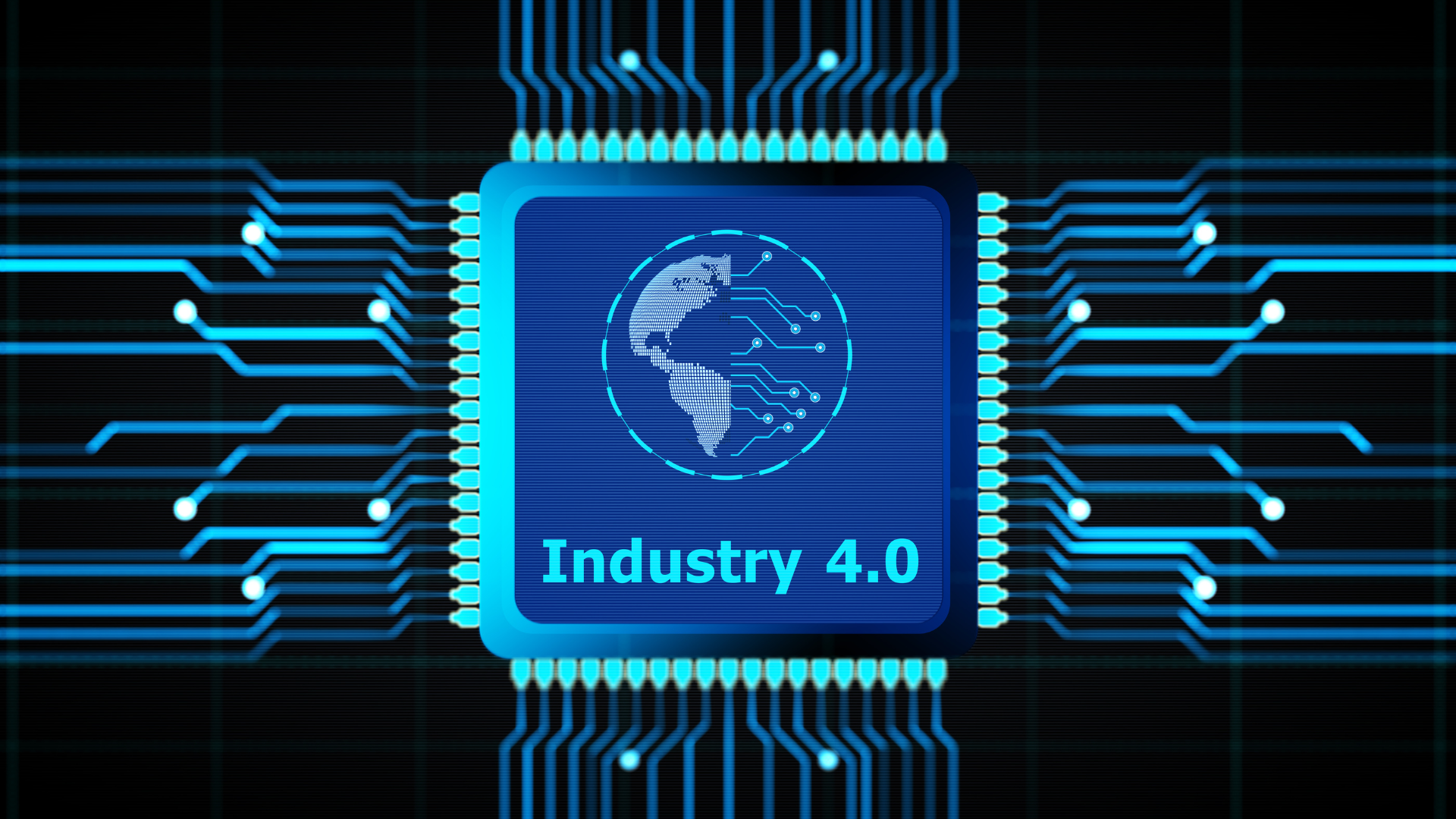
Is Industry 4.0 Still Relevant
Industry 4.0 remains highly relevant and continues to influence modern manufacturing practices significantly. As technology evolves, Industry 4.0 adapts, introducing new innovations that enhance connectivity, automation, and data-driven decision-making. The ongoing need for industries to improve efficiency, reduce costs, and offer customized products keeps Industry 4.0 at the forefront of economic and technological development. This relevance is cemented by its ability to integrate emerging technologies such as AI and IoT (Internet of Things), which are becoming critical in achieving advanced manufacturing capabilities. Moreover, as businesses face increasing pressure to become more sustainable and adaptable, Industry 4.0 offers the tools and methodologies necessary to thrive in a rapidly changing environment.
Industry 4.0 Applications
Industry 4.0 applications span a wide range of uses that facilitate more efficient and responsive manufacturing processes. These include IoT (Internet of Things) devices for real-time monitoring and AI algorithms for predictive maintenance, both of which significantly improve operational efficiencies. The adoption of these applications helps manufacturers reduce downtime, enhance product quality, and streamline supply chains.
Examples of Industry 4.0 in Manufacturing
Industry 4.0 has revolutionized manufacturing with examples such as automated production lines that adjust operations in real-time based on AI-driven insights. IoT (Internet of Things) sensors play a crucial role in tracking and managing energy usage, contributing to more sustainable operational practices. These technologies exemplify how Industry 4.0 is not just enhancing efficiency but also promoting environmental sustainability within manufacturing sectors.
What Is an Example of IR 4.0 Technology
An example of IR 4.0 (Industry 4.0) technology is the implementation of smart factory systems that utilize IoT (Internet of Things) devices to create fully integrated, automated production environments. These systems enable real-time monitoring and control of the manufacturing process, allowing for instantaneous adjustments to improve efficiency and reduce waste. Advanced robotics, used in conjunction with IoT and AI, further exemplify how Industry 4.0 technologies streamline operations and foster adaptive manufacturing capabilities. For instance, digital twin technology allows manufacturers to create virtual replicas of physical systems to simulate and optimize operations before actual implementation. This integration of cyber-physical systems exemplifies the core of Industry 4.0, transforming traditional manufacturing into highly efficient, data-driven operations.
Industry 4.0 PDF
Industry 4.0 PDF documents provide a wealth of information on how digital transformations are reshaping manufacturing. These resources often include detailed analysis of technology implementation, case studies from leading companies, and strategic advice for successfully integrating new technologies. They serve as essential guides for businesses looking to understand and apply Industry 4.0 principles effectively.
Industry 4.0 McKinsey
McKinsey's insights into Industry 4.0 highlight the strategic importance of these technologies in driving business growth and operational efficiency. Their reports detail how companies can harness the power of digital tools like AI, IoT, and robotics to transform their manufacturing processes. McKinsey also offers frameworks that help businesses implement these changes in a way that maximizes return on investment and competitive advantage.
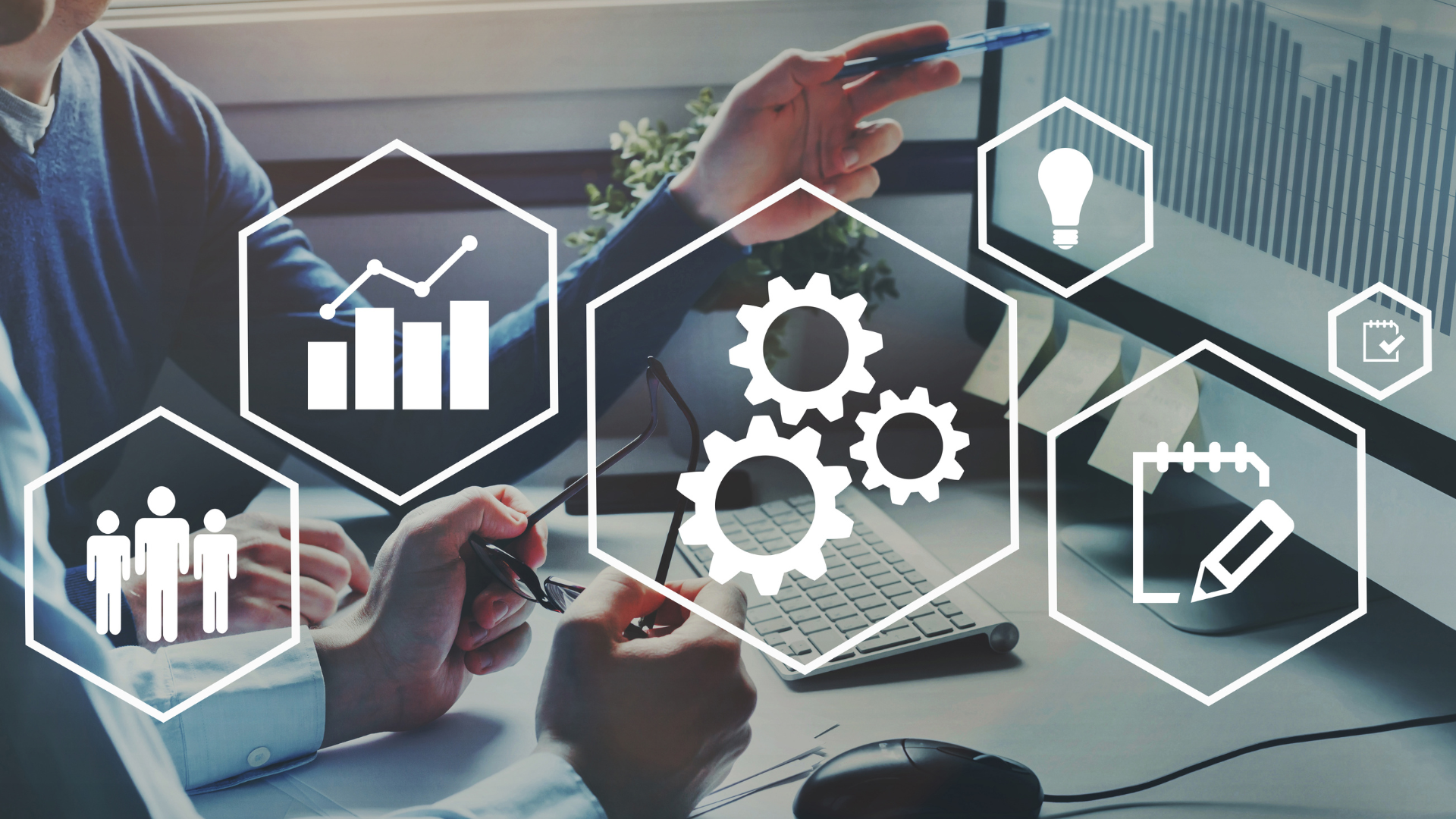