Furthermore, it is worth noting that Industry 4.0, also known as the Fourth Industrial Revolution, plays a crucial role in enabling enhanced quality control and product customization. With the advent of advanced technologies such as Internet of Things (IoT), cloud computing, and big data analytics, manufacturers can now leverage real-time data to monitor and optimize production processes. This allows for immediate identification and rectification of any potential quality issues, ensuring that only products meeting the highest standards reach the market. Moreover, Industry 4.0 empowers businesses to offer highly personalized products to their customers. Through the integration of smart manufacturing systems and digital technologies, companies can efficiently gather customer preferences and utilize this information to tailor their products accordingly. This level of customization not only enhances customer satisfaction but also provides businesses with a competitive advantage in today's dynamic market. In summary, Industry 4.0 not only revolutionizes manufacturing processes but also paves the way for improved quality control measures and product customization capabilities. By embracing these advancements, companies can stay ahead in an ever-evolving business landscape while delivering superior products to their customers. With real-time data collection and analysis, manufacturers can monitor production processes closely, identify potential issues early on, and make necessary adjustments to ensure consistent product quality. Additionally, the ability to customize products according to individual customer preferences becomes more feasible with flexible manufacturing systems enabled by Industry 4.0 technologies.
What Is Industry 4.0 And Its Benefits?
What Is Industry 4.0 And Its Benefits?
Industry 4.0 in Manufacturing, also referred to as the fourth industrial revolution, is a revolutionary concept that involves the seamless integration of advanced Industry 4.0 technologies into various manufacturing processes. It marks a significant shift in the traditional manufacturing landscape by embracing cutting-edge technologies such as artificial intelligence, machine learning, internet of things (IoT), robotics, and big data analytics. This integration allows for enhanced automation, improved efficiency, increased productivity, and better decision-making capabilities throughout the entire manufacturing value chain. Industry 4.0 empowers manufacturers to achieve higher levels of customization, flexibility, and responsiveness to meet evolving customer demands while reducing costs and minimizing waste. The implementation of Industry 4.0 principles has the potential to transform traditional factories into smart factories that are connected and intelligent systems capable of self-optimization and real-time monitoring. This transformative revolution is poised to shape the future of manufacturing by enabling companies to stay competitive in an increasingly digitalized world. It involves the use of automation, data exchange, and artificial intelligence to create a smart and connected manufacturing environment.
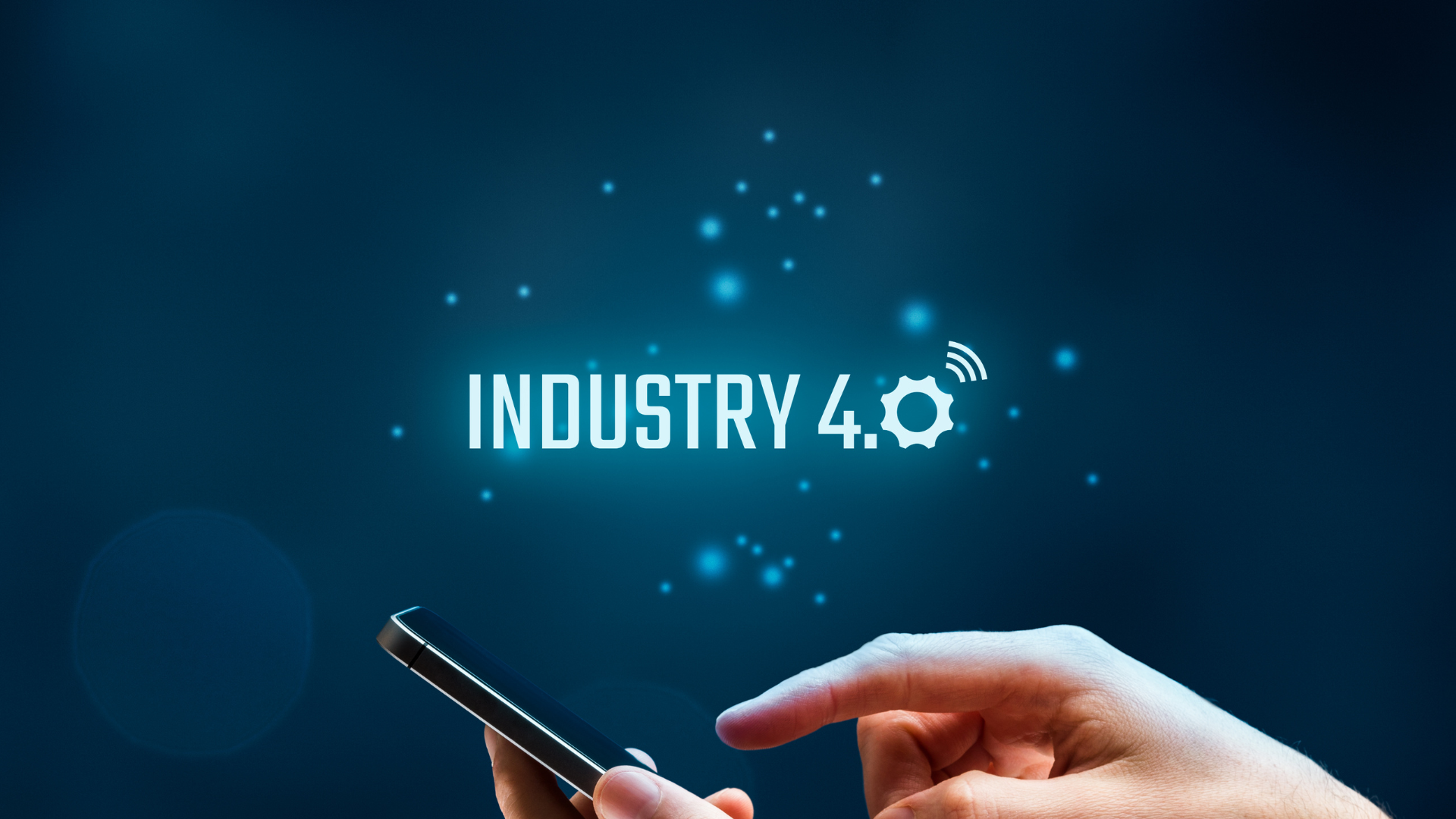
Industry 4.0 Benefits
Industry 4.0 has revolutionized the way businesses operate, bringing numerous benefits to various sectors. This fourth industrial revolution combines digital technologies with physical systems, leading to increased efficiency, productivity, and profitability. The benefits of Industry 4.0 extend beyond just manufacturing; they can be seen across industries such as healthcare, logistics, and agriculture. One of the key advantages of Industry 4.0 is the enhanced connectivity it offers. Through the Internet of Things (IoT), machines are able to communicate and exchange data in real-time, enabling seamless coordination and optimization of processes. This connectivity leads to improved operational efficiency as well as better decision-making through access to accurate and timely information. Another benefit is the increased automation that Industry 4.0 brings. With the integration of smart machines and robotics, repetitive tasks can be automated, freeing up human resources for more complex and creative work. This not only improves productivity but also reduces errors, resulting in higher quality output. Furthermore, Industry 4.0 enables predictive maintenance by leveraging advanced analytics and machine learning algorithms. By analyzing data from sensors embedded in equipment or machinery, potential issues or failures can be detected early on, allowing for proactive maintenance actions that prevent costly breakdowns or downtime.
The adoption of Industry 4.0 also promotes sustainability by optimizing resource utilization through smart energy management systems and waste reduction strategies. By monitoring energy consumption patterns in real-time and implementing energy-efficient solutions, businesses can reduce their carbon footprint while cutting costs. Lastly, Industry 4.0 offers new opportunities for innovation and competitiveness in global markets by enabling customization at scale known as mass customization. Through advanced technologies like additive manufacturing (3D printing), companies are able to produce personalized products quickly without compromising on quality or cost-efficiency. In conclusion, the benefits of Industry 4.0 are vast - from increased connectivity for seamless coordination to automation for improved productivity; from predictive maintenance for reduced downtime to sustainability initiatives for a greener future; and from innovation opportunities to customization capabilities. Embracing Industry 4.0 is not just a choice but a necessity for businesses looking to thrive in the ever-evolving digital landscape. Firstly, it enables increased productivity and efficiency in manufacturing operations. By leveraging technologies such as robotics and Internet of Things (IoT), companies can automate repetitive tasks, optimize production schedules, and reduce downtime.
Industry 4.0 Technologies
Industry 4.0 Examples
Furthermore, in the era of Industry 4.0, businesses are increasingly leveraging advanced technologies to drive cost savings and efficiency. One notable area where Industry 4.0 initiatives have made significant strides is in predictive maintenance strategies. By utilizing real-time data and machine learning algorithms, organizations can proactively identify potential equipment failures or maintenance needs before they occur, thereby minimizing downtime and expensive repairs. In addition to predictive maintenance, Industry 4.0 also emphasizes supply chain optimization. With the help of AI-powered analytics tools, companies can analyze vast amounts of data related to their supply chain operations, such as inventory levels, demand patterns, and transportation logistics. This enables them to make more informed decisions that optimize inventory holding costs, reduce lead times, enhance delivery performance, and ultimately contribute to overall cost savings. By embracing Industry 4.0 principles like predictive maintenance and supply chain optimization through advanced technologies such as AI and analytics tools, businesses can gain a competitive edge by operating more efficiently while reducing costs in an increasingly dynamic market environment. By utilizing sensors and analytics tools for predictive maintenance purposes, manufacturers can detect equipment failures before they occur and schedule maintenance activities accordingly. This proactive approach helps prevent costly breakdowns and minimize unplanned downtime.
Lastly, the advent of Industry 4.0 has significantly revolutionized the business landscape, offering a plethora of exciting and unprecedented opportunities for businesses across various sectors. By embracing the principles of Industry 4.0, companies can experience a substantial boost in innovation, leading to the development of cutting-edge products and services that cater to ever-evolving consumer demands. The integration of advanced technologies such as artificial intelligence, robotics, and Internet of Things (IoT) enables businesses to streamline their operations, optimize efficiency, and create new value propositions that were previously unimaginable. This transformative era empowers organizations to stay ahead of the competition by leveraging emerging technologies and harnessing their potential for growth and success in an increasingly digital world. Companies that embrace these advanced technologies can develop innovative solutions that meet evolving customer demands while staying ahead of competitors in a rapidly changing market landscape.
To learn more about Industry 4.0 and its applications in manufacturing, you may refer to industry-specific publications or books that delve deeper into this topic or explore PDF resources available online that provide insights into the benefits of implementing Industry 4.0 strategies in various industries.