What is a process alarm?
In industrial operations, especially in process control systems, understanding the concept of
Types of alarms in SCADA
is crucial. A process alarm is a notification system used to alert operators about abnormal conditions in a plant or factory. These alarms are designed to help detect potential issues before they escalate into major problems, ensuring safe and efficient operations. In this article, we’ll explore what process alarms are, their purposes, and how they contribute to the overall effectiveness of alarm management systems.
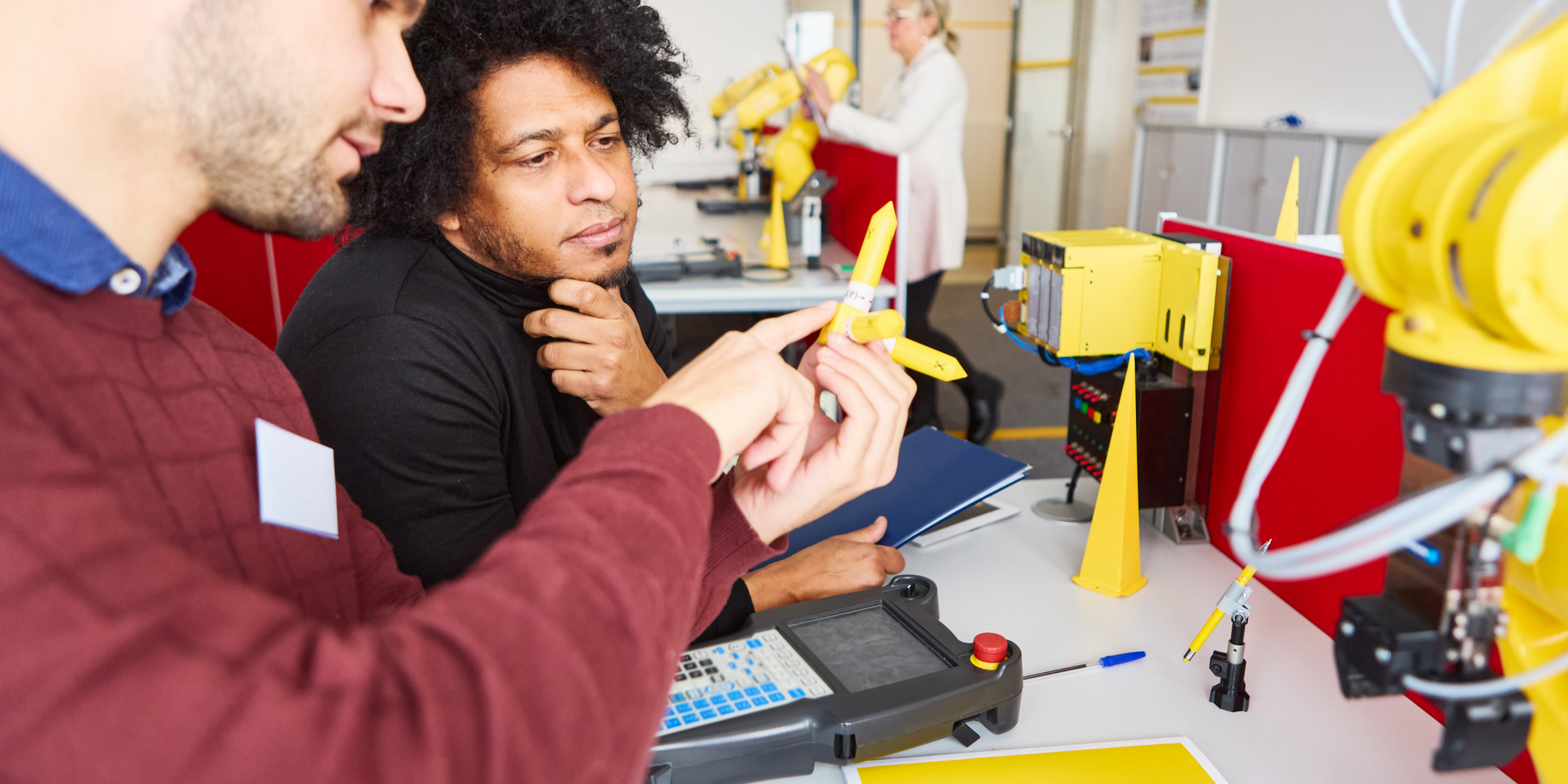
What is a Process Alarm?
A process alarm is a critical tool in alarm management, specifically designed to notify operators when a process deviates from normal conditions. Process alarms are typically integrated into industrial control systems such as SCADA (Supervisory Control and Data Acquisition), where they signal when equipment or systems require attention. The alarms can indicate issues like equipment malfunction, unsafe conditions, or process deviations. To manage these alarms effectively, standards such as IEC 62682 are used to ensure that the alarm system is appropriately configured for optimal response and safety.
What is an Alarm Management System?
An alarm management system is essential for ensuring that alarms are effectively prioritized, categorized, and managed throughout their lifecycle. It is designed to handle the full alarm process, from detection to resolution. Tools like EEMUA Alarm Management and ISA Alarm Management standards help maintain the integrity of these systems, ensuring that alarms are both informative and actionable. A good alarm management system helps prevent alarm overload, allowing operators to focus on critical issues, improving response times, and minimizing unnecessary distractions.
What is the Purpose of a Process Alarm?
The purpose of a process alarm is to provide immediate notification when a system or process requires attention. By highlighting potential hazards or operational inefficiencies, process alarms ensure that operators can intervene before issues become dangerous or costly. Alarm management for process control is essential for identifying not only faults but also the root causes of problems. With the integration of alarm management software, systems can categorize, escalate, and resolve alarms more efficiently, preventing disruptions and improving overall safety and productivity.
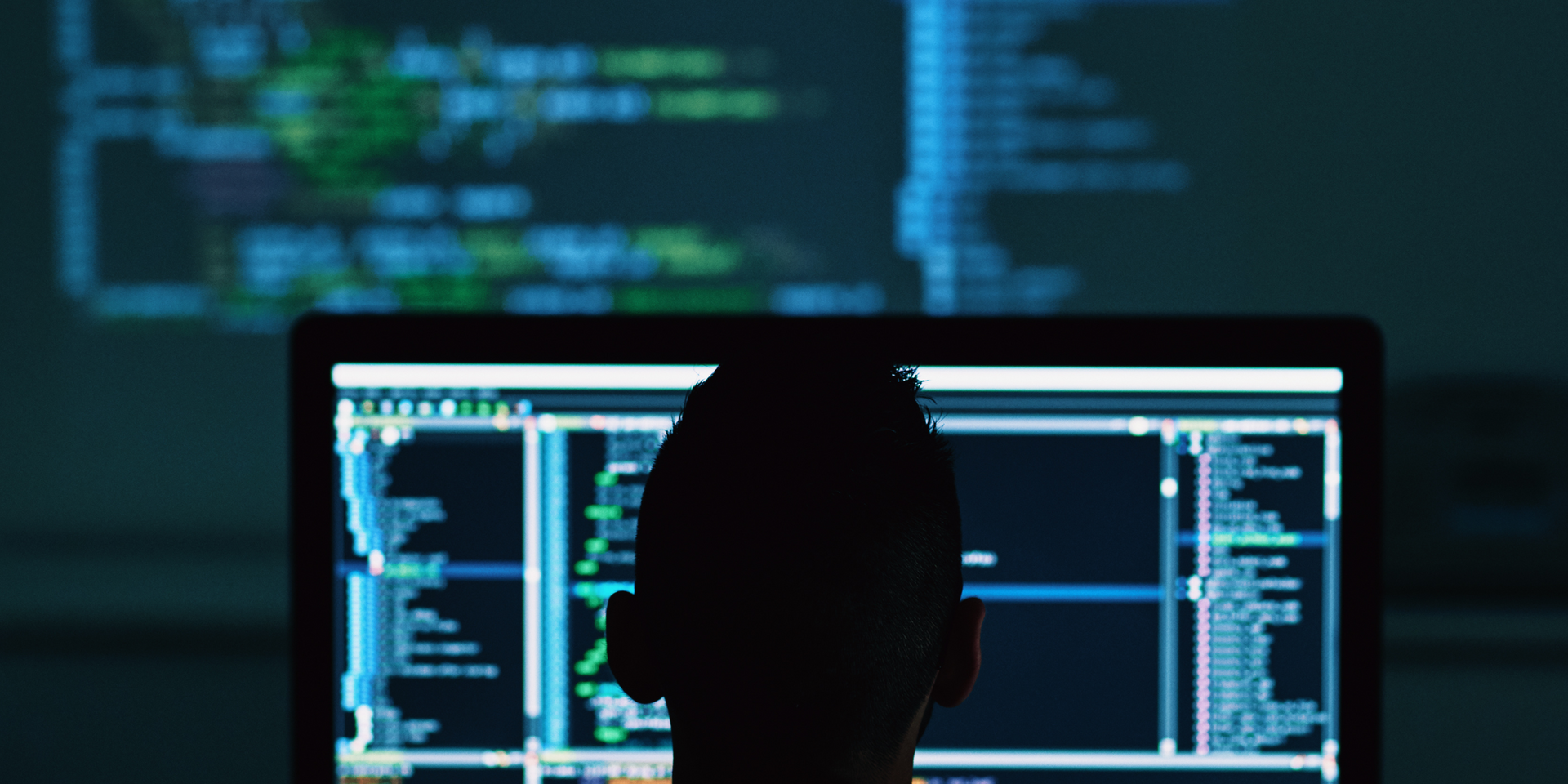
What is a SCADA Alarm?
A SCADA alarm is an automated system alert that notifies operators when a parameter within the SCADA system falls outside the acceptable range. SCADA alarm notification software is an integral part of process automation, as it enables real-time monitoring and quick response to process fluctuations. Through alarm logging & notification, operators can track all alerts in a centralized system, improving response times and minimizing the risk of system failures. This system also supports tracking, analysis, and reporting of alarm events to ensure compliance with regulatory standards.
What is a State of Alarm?
A state of alarm refers to the heightened state of alert triggered by specific abnormal conditions within a system. This alert often involves multiple alarms that may require immediate corrective actions. Within alarm management, understanding the seven types of alarm systems is crucial. These systems include SCADA alarm management software, which helps categorize and prioritize alarms based on severity, ensuring that operators can focus on the most critical issues first.
What Are Alarms in SCADA?
In SCADA systems, alarms are used to monitor and control process variables. Automating process control alarm response ensures that the system can respond to alarms automatically, potentially mitigating issues before human intervention is required. A well-implemented alarm in SCADA system helps improve system reliability, reduce the risk of human error, and enhance the overall efficiency of the operations.
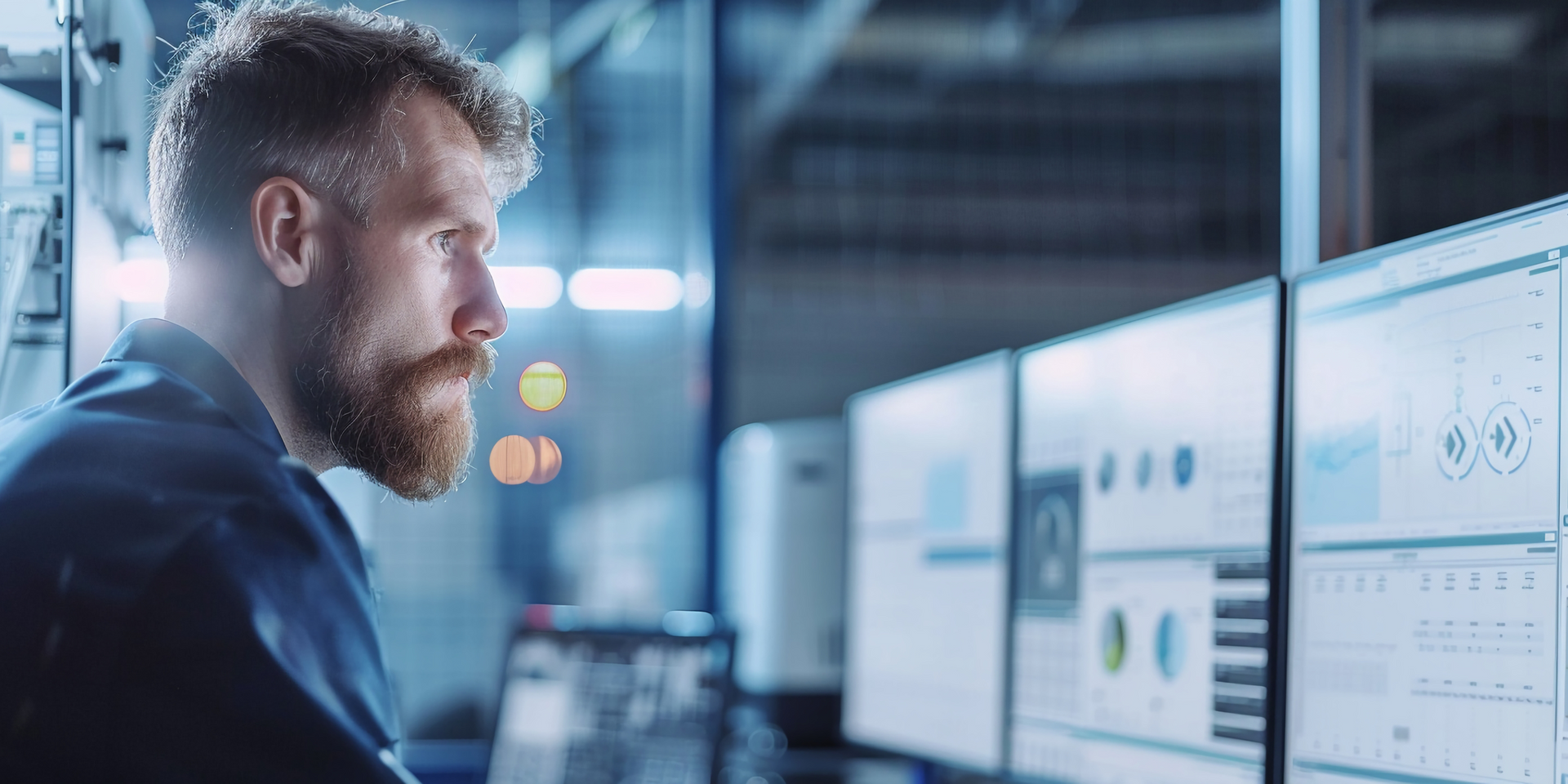
What Are Alarms Used For?
Alarms are used to signal abnormal conditions and prevent accidents. In industrial environments, process alarms help ensure that operations run smoothly by alerting operators to potential issues like temperature fluctuations, pressure changes, or equipment malfunctions. Alarm management standards help optimize the use of these alarms by ensuring they are configured to meet safety requirements. Proper alarm systems for process control are essential to maintaining operational safety, efficiency, and regulatory compliance.
What Are the 3 Main Types of Alarms?
Alarms typically fall into three main categories: warning, critical, and emergency alarms. These alarms serve distinct purposes in monitoring systems. For example, warning alarms are used for minor deviations that do not pose immediate threats, while critical alarms indicate more serious issues that require immediate attention. Emergency alarms are the most severe, alerting operators to potentially hazardous or life-threatening conditions. Understanding the different types of alarms is vital for effective alarm management and operator response. As defined by the ISA182 alarm management standard, these systems prioritize alarms based on their severity and potential impact.
Conclusion
Process alarms play an integral role in ensuring the safety and efficiency of industrial operations. Whether it’s managing SCADA alarms, implementing alarm management software, or understanding the different types of alarms, every aspect of alarm management works toward creating a safer working environment. What is a process alarm? is just the beginning of understanding how alarm systems can optimize operational performance.
If you're looking to enhance your alarm management systems or need more information about process alarms, consider implementing a dedicated alarm management solution today,
contact us!