Top Benefits of Alarm Notification System in Manufacturing
Manufacturing places need to find and fix problems quickly. This helps reduce risks and keep things running smoothly. An alarm system together with a smart notification system works as a strong support for today’s management systems. They make sure important alerts get to the right people on time. These
Types of alarms in SCADA
setups are essential to deal with alarm fatigue, make operations better, and protect workers in facilities. Using alarm notification systems correctly not only boosts safety but also helps manufacturers monitor situations better and respond more quickly.
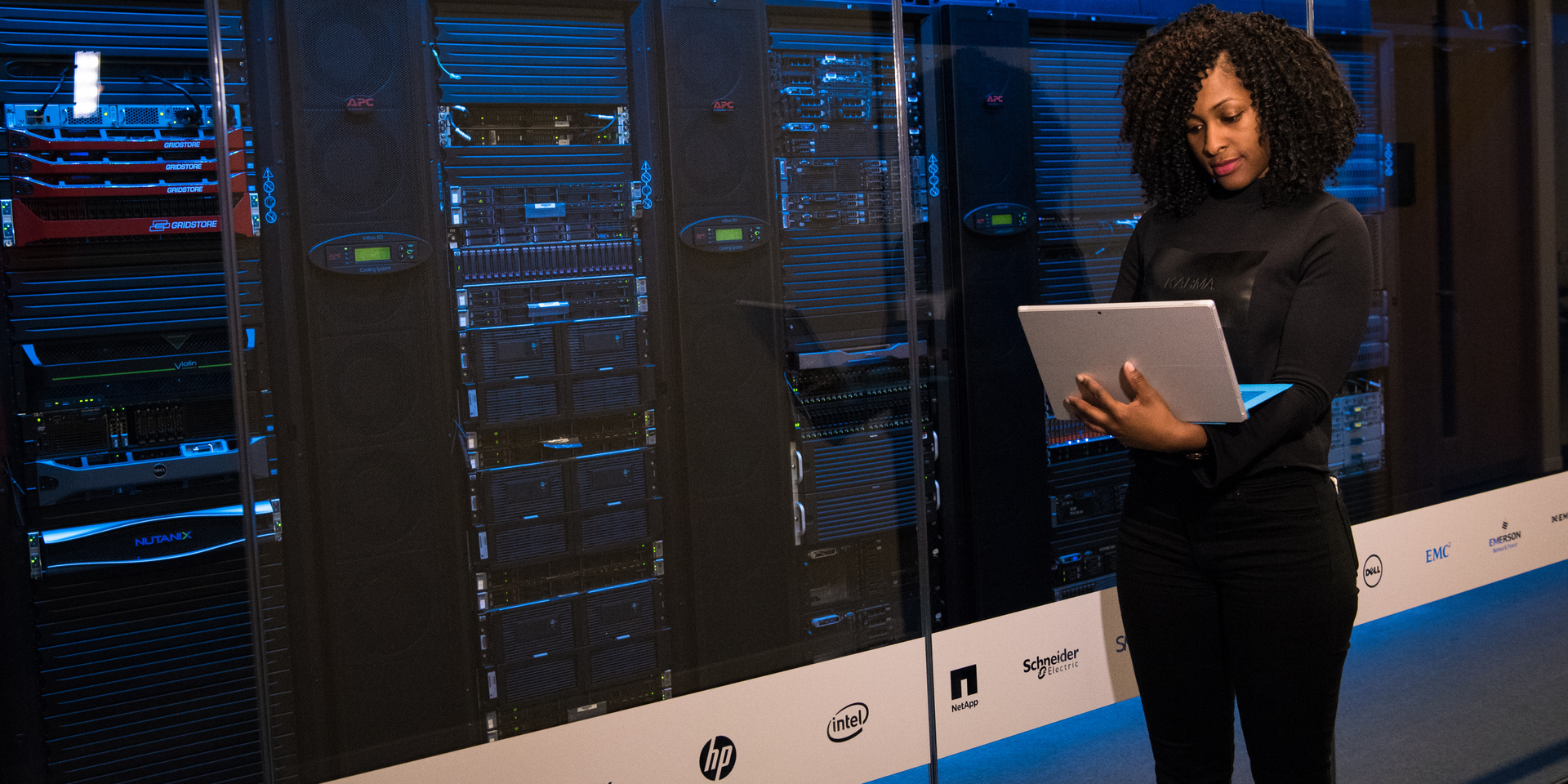
Understanding Alarm Notification Systems in Manufacturing
The role of alarm notification systems in manufacturing has grown a lot. These systems help connect the monitoring of important processes with fast responses in emergencies. They work well with different technologies and are key to good manufacturing setups.
Now, alarm systems aim to cut down on extra noise, which is called alarm fatigue, by highlighting important updates. They automate responses and prioritize what matters. This makes monitoring better and helps manage emergencies effectively. Let’s look into their details more.
What is an Alarm Notification System?
An alarm system in manufacturing helps alert users about problems or unsafe events. This ensures that everything runs well. These systems gather alarms from various devices. This includes HVAC systems, generators, and assembly lines. They turn these alarms into useful notifications.
What makes alarm notification systems special is their real-time monitoring ability. They analyze data and connect with controllers like PLC and SCADA. This helps centralize operations. Notifications are sent wirelessly through SMS, email, or mass alerts. This improves response dependability.
These systems do more than send alarms. They allow two-way communication. This means updates can be managed right away. Automated workflows make everything easier, like informing technicians and alerting decision-makers about big issues. With various configurations, these systems greatly improve facility management and emergency actions. This usefulness shows why alarm notification systems are now key in modern manufacturing.
Importance of Effective Alarm Management
Alarm management is very important for making notification systems work well. When alarms are not set up properly, staff can get overwhelmed by too many unnecessary alerts. This can delay their responses and put safety at risk. Good management means that only the most important alarms go through priority channels.
Modern systems offer customizable settings. These let alerts be filtered based on how serious they are and the specific conditions. By using a clear emergency notification plan, facilities can set rules to group alerts together or change who gets the alerts depending on certain situations. These setups help lower alarm fatigue and improve readiness for emergencies.
Effective alarm management also helps facilities keep track of rules and follow SLAs. When the whole organization is in sync, communication gets better, decision-making is faster, and responses in critical times are quicker. Recognizing this importance shows the possible uses that we will discuss next.
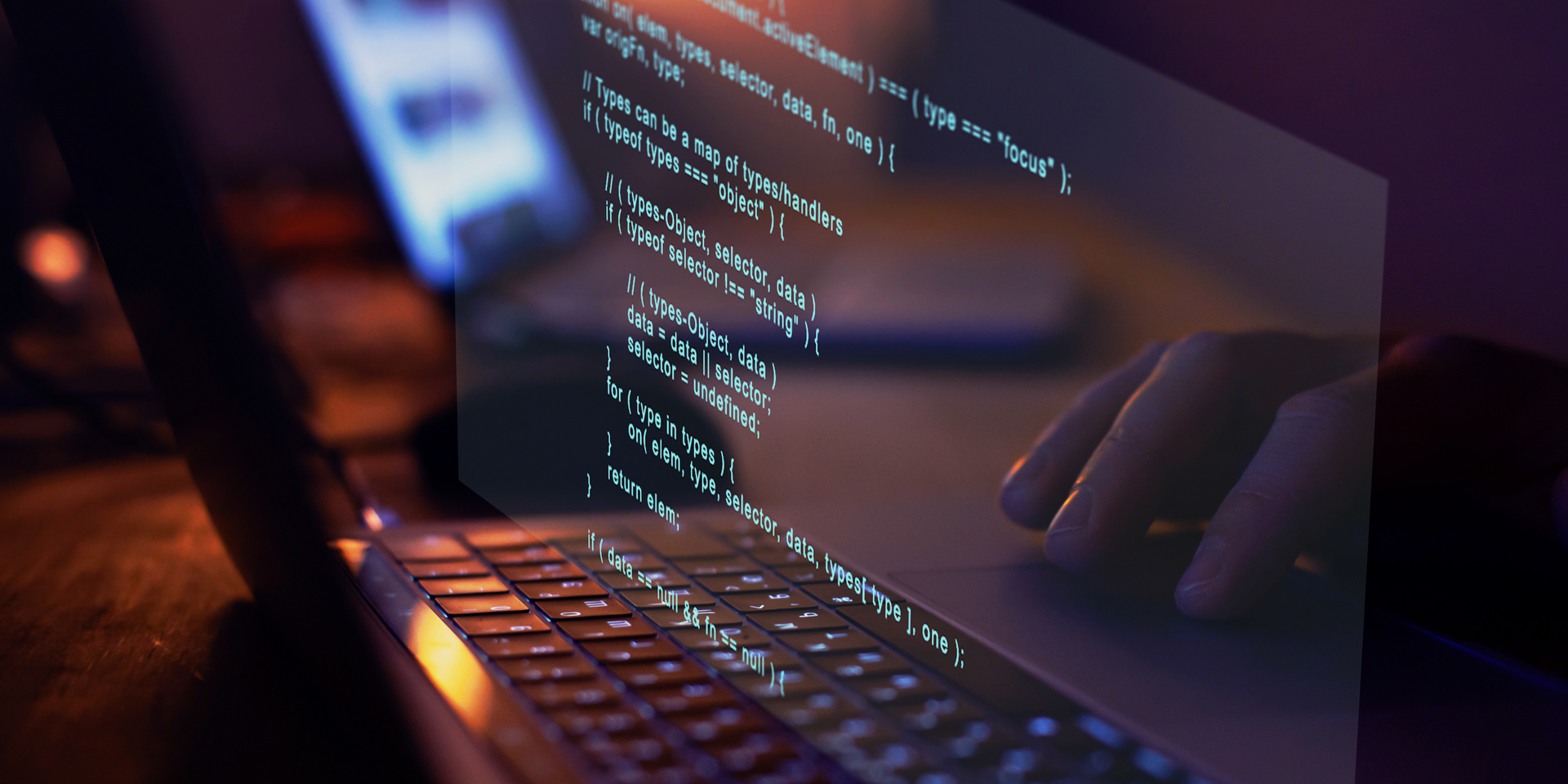
Manage SCADA Alarm Notifications Any Way You Choose
Managing alarm notifications for SCADA systems allows manufacturers to be very flexible. It doesn't matter if alerts come from cloud controllers, IoT devices, or industrial setups. Systems like HipLink help automate and improve how notifications are delivered.
Users can create specific rules and escalation levels, making SCADA alert notifications both customizable and effective. These systems work well with old devices, taking inputs like ASCII and turning them into valuable notifications. This management makes sure that every manufacturing process runs smoothly and that no important issues are missed.
More Control for Notifications
Taking control of alarm notifications means you can adjust how and when you get them. Modern systems like HipLink send alerts over wireless networks. This allows you to manage them easily and keep everything efficient. You can set up groups of people to receive messages and pick which ones are more important or even change routes for notifications.
Wireless methods for alerts give you more flexibility. They work on all types of devices like smartphones and paging systems. They can also confirm that important messages are received without a hitch. Custom filters help to block out alarms that are not important. This reduces distractions and keeps your focus on what really needs attention.
These systems also let you connect codes to user groups. You can even rotate alerts based on different types of incidents. This detailed control makes sure everything runs smoothly, whether you are monitoring assembly lines or checking the environment. Because of this, manufacturers can manage notifications better. This is a big benefit that helps improve how they operate.
Send & Acknowledge Alarms Via 2-Way Email
Two-way email features improve alarm handling. Sending alarms through email not only tells everyone but also encourages quick responses and acknowledgments.
Benefits include:
- Notifications sent through SMS, email, alerts, or wireless methods ensure no alarm is missed.
- Staff can acknowledge alarms from anywhere, leading to quicker problem solving without needing to be there in person.
- Tracking options provide better accountability during emergencies and for reviews later.
- This method also allows setups based on certain conditions. It filters messages according to the user’s chosen criteria. Email quickly connects teams in different places, which helps improve decisions during crises. As manufacturing processes become more complex, this reliable tool keeps operations running smoothly without losing monitoring reliability.
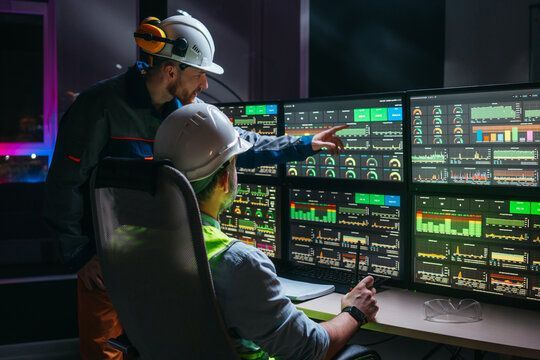
Key Benefits of Implementing an Alarm System
The use of advanced alarm systems has real benefits. First, they make things safer. You get instant emergency notifications that help lower risks and stop accidents.
Also, alarm notifications help improve how things run by cutting downtime with quick responses. They fit well with current systems, help meet rules, and lower costs. Manufacturing places can change workflows to be more productive and keep their service agreements. With all these benefits together, alarm systems are very important for better facility management.
Enhanced Safety and Quick Response Times
One of the best things about alarm systems is better safety for everyone. They quickly send emergency notifications to help reduce risks from equipment failure, fires, or environmental dangers.
Their ability to deliver alerts instantly means fast decision-making, which is crucial during serious situations. Features like alarm prioritization help sort out unimportant alerts, letting staff pay attention to real emergencies. This keeps work running smoothly, even when there is a lot of pressure.
Most importantly, features like quick response mechanisms stop expensive disruptions by helping managers respond before small issues turn into big problems. With two-way communication, they ensure that all feedback and updates are shared during emergencies. This kind of reliability improves safety in industries that need high precision, like manufacturing, while also boosting worker confidence when unexpected events occur.
Improved Operational Efficiency and Reduced Downtime
Keeping operations running smoothly is very important in manufacturing. Intelligent alarm notifications play a big role in making this happen. Systems like HipLink help workers automate their tasks. This means that processes don't stop for no reason.
By setting up different alert configurations, downtime is avoided. Alerts let the right teams know about internal machine problems or outside issues like bad weather. These fast notifications help facilities get back to work quickly.
Less downtime means less money lost. Manufacturers save time and resources that would be wasted during unexpected breaks. Alarm systems can watch many control systems, such as PLC, SCADA, and standalone controllers. This makes them crucial in keeping things running smoothly. More productivity leads to faster business results.
Conclusion
In conclusion, using an alarm notification system in manufacturing is crucial. It improves safety and makes operations smoother. By managing alarms well, you can cut down on response times and boost efficiency. These systems give teams better control over notifications. This helps address any issues quickly. When thinking about the main benefits of these systems, remember that choosing technology that works well with your current processes will create stronger and more productive manufacturing spaces. If you want to see how an alarm notification system can help your operations, we invite you to get a free consultation with our experts.