Exploring the Future of Automatic Manufacturing Today
Exploring the Future of Automatic Manufacturing Today
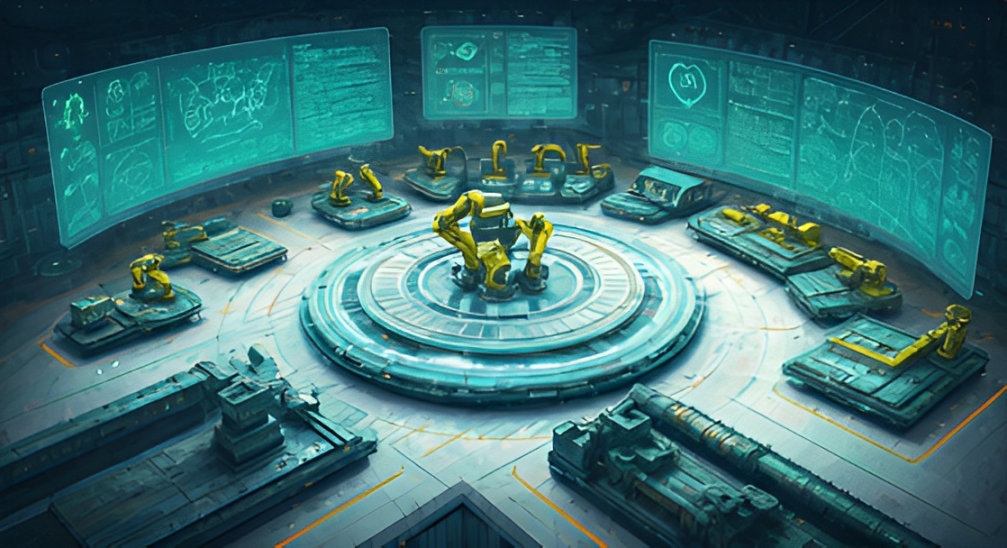
Key Highlights
- Automatic manufacturing systems leverage industrial automation tools, such as control systems, robotics, and smart sensors, to optimize the manufacturing process and improve production efficiency.
- Reduced reliance on human intervention minimizes errors and speeds up operations, enhancing output consistency.
- Advanced technologies like artificial intelligence, programmable automation, and flexible automation enable customization and adaptation to market demands.
- Automation supports digital transformation in industries, streamlining operations and increasing overall productivity.
- Businesses gain better quality control, lower labor costs, and the flexibility to handle various manufacturing processes efficiently.
Introduction
The world of automatic manufacturing is changing how industries work all over the globe. When companies add advanced technology to the manufacturing process, they get more done in less time, make fewer mistakes, and do the job with more care. This kind of digital transformation makes daily work easier and helps businesses keep up when customers want things their own way.
With these new systems, there is less need to rely on manual processes. The focus stays on continuous improvement and boosting production efficiency. Whether you want to use it at your own place or just learn what could happen with it in the future, automatic manufacturing is important. It helps you stay competitive and get your business ready for what’s next.
The Evolution of Automatic Manufacturing
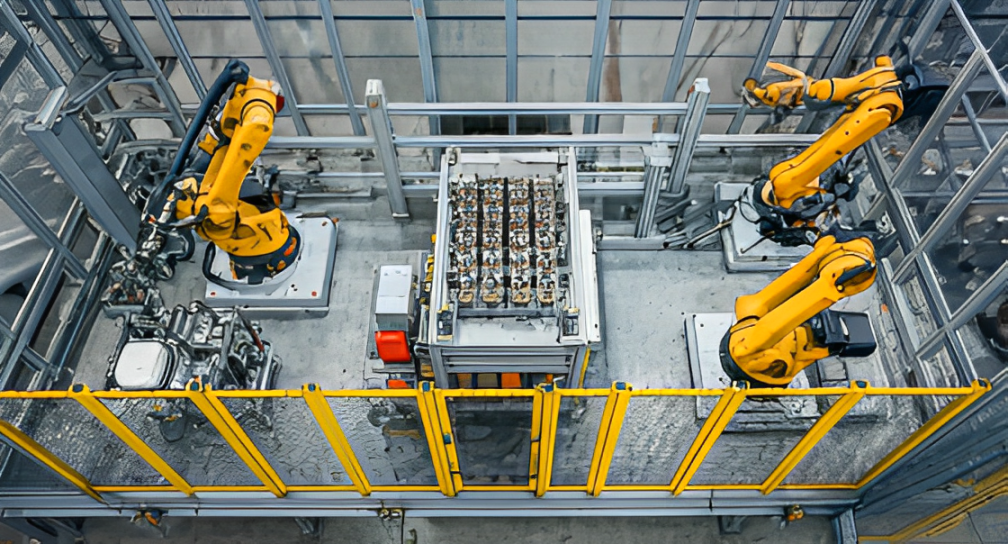
Technological changes have had a big effect on automatic manufacturing. Now, artificial intelligence and industrial robots are used in many production lines. This makes things faster and better while cutting down on the need for people to step in. There are also new, smarter systems for flexible automation, helping businesses change the way they run things when needed.
Some big names in the industry, like General Motors, use these tools every day. They use data and the internet of things to improve supply chain management. These tools help lower labor costs, boost product quality, and make modern manufacturing work better for everyone involved.
From Manual Labor to Automation: Key Milestones
The road to modern manufacturing started with manual work and simple tools. People did most of the work by hand. This way was useful, but it took a lot of time and there were often mistakes.
Things changed with the automated manufacturing system that came during the Fourth Industrial Revolution. Batch production started to be common. General Motors, for example, used conveyor belts. These new systems made the work more steady and much faster.
Soon, companies used programmable automation and flexible automation. These cut down on the need for stiff setups. In recent years, industries all over the world have used these changes. They have brought in advanced robots and connected systems. This new way of working makes up the main part of modern manufacturing systems now.
Influential Technologies That Shaped the Industry
Industrial automation has grown a lot because of new and creative technologies. Industrial robots have changed the way people work on assembly lines. They help finish jobs quickly and with more accuracy than ever before. There are many companies, like those in the automotive industry, that now use automated assembly lines and depend on these robots every day.
Another big help in this area is programmable logic controllers (PLCs). These systems control machines and let people easily change them to work for both small and large batches. These controllers, when used with numerical control systems and machine tools, help take out human error. This makes every product look and work the same.
The automotive industry has seen a big rise in production efficiency since these technologies came together. This has let the industry work much faster and get more done. The way industrial automation works now is always getting better because people want answers that fit their needs in each industry.
Core Technologies Powering Modern Automatic Manufacturing
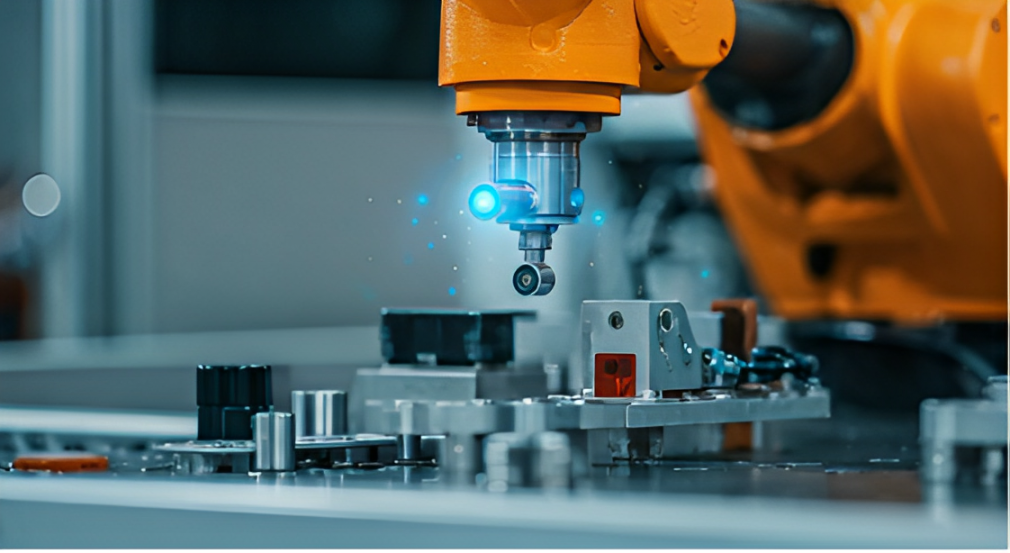
Cutting-edge robotics, artificial intelligence, and control systems are now a big part of how automatic manufacturing works. These tools help companies make more products in less time. They lower mistakes and increase production efficiency. By using control systems and bringing together various manufacturing processes, they let everything work together without any problems.
When you mix AI-driven control systems with robots, something special happens. These systems can learn, change, and get better in real time. In this way, businesses can grow and still keep their work exact. Next, we will look at how artificial intelligence and robotics, as well as IIoT, are changing smart factories.
Robotics and Artificial Intelligence Integration
The coming together of robotic arms and artificial intelligence has turned factories into places where things get made with great accuracy and speed. When robots and AI work together, they help remove human error from tasks that get repeated a lot, like putting things together and welding. This makes sure every product comes out the same, every time.
AI helps spot problems in the main types of automation. This means things can fix themselves and keep getting better over time, leading to continuous improvement. For example, some smart, flexible AI systems can quickly change from making one product to another. They match the production speed to what’s needed in the moment. You can see this in factories like Tesla, where robots and AI help things move fast.
Working together, people and smart machines raise the way we do things in the factory. They show what’s possible when using fewer things to make more. In the end, you get more work done, and there are fewer chances for things to go wrong or get wasted.
Industrial Internet of Things (IIoT) & Smart Sensors
The use of the Industrial Internet of Things (IIoT) and smart sensors is changing the way the manufacturing process works. These devices are linked together. This helps factories be more efficient and improve product quality. They collect data in real time, so companies can spot problems early and fix them before machines break. This way, there is less risk of human error. Smart sensors also keep track of how machines are running and watch the conditions in the work area. This allows people to make their production lines work better.
When factories use IIoT, they also manage the supply chain in a smarter way. It helps with digital transformation, which is needed to stay up to date. Adopting these changes puts factories at the top as the fourth industrial revolution continues.
Advancements in Manufacturing Software
Software solutions are at the center of digital transformation in manufacturing. Smart manufacturing software helps automate production planning, tracking, and how work gets done. This makes everything more efficient in the plant.
With automation technology, these tools connect easily to IoT devices and sensors. In the next part, we will look at software updates like CAD/CAM and cloud-based production tools. We will show how these new ideas are changing the way things work in manufacturing plants.
Computer-Aided Design (CAD) and Manufacturing (CAM)
The use of computer-aided design (CAD) and computer-aided manufacturing (CAM) is a big step forward in industrial automation. These tools help you make products with more care and accuracy. They also make it easier to turn hard designs into real items with automated systems. With advanced software, companies can work on their control systems, bring down labor costs, and boost product quality. The help from CAD and CAM supports continuous improvement in the supply chain. This drive for better ways of working makes modern manufacturing more productive and efficient for all of us.
Cloud-Based Production Management
Cloud-based systems bring all the work together in one place. They help connect machines, people, and the full supply chain in a way that is quick and simple. With these tools, you can track everything from afar. This means you can make changes to your production lines in manufacturing plants right when needed.
Benefits
Enhanced Transparency
Cost-Effective Scaling
Remote Management
Examples
Monitor production at all stages.
Add new machines with minimal downtime.
Oversee operations from anywhere.
These systems also let you use your control systems together. This helps companies in manufacturing plants stay up to date and still have good, easy access for everyone.
Impact on Workforce and Skills Development
Automation is changing the workforce. Companies do not need as much manual work now. This helps them spend less on labor costs and lets them use that money to help workers learn new skills. People get training for better roles in modern manufacturing.
Job roles are always changing. Because of this, people have to learn how to use advanced systems at work. This helps them keep their jobs and move up in their careers. Up next, you will see how gaining new skills and working with machines together are important in this new way of work.
Upskilling for Advanced Manufacturing Roles
The rise of modern manufacturing means workers need to learn new skills to keep up with automation technology. People in these jobs must take special training so they can watch over robots and use control systems for automation.
Policymakers and those in industries work together to lower labor costs and make more high-skill jobs. Team members join training programs to help them move into new roles more easily. This training also cuts down on human intervention in jobs that get done again and again, which is what the market needs now.
By making this investment, they make sure there is a skilled group of people for modern factories. It helps these workplaces to run well and do their jobs better.
Human-Machine Collaboration in Smart Factories
In smart factories, humans and machines work together to bring new ideas. The use of automation technology and people watching over it helps lower the risk of human error. This teamwork pushes the limits of what manufacturing systems can do.
Machines are great at doing the same tasks again and again. At the same time, people are good at seeing things in new ways and making changes. In these factories, human-machine collaboration keeps things precise, even with creative jobs like product design. This helps make sure that there is both creativity and the same good results every time. This way makes the manufacturing field better than ever.
Sustainability and Green Manufacturing Initiatives
Moving towards green and sustainable ways in manufacturing is a must. It is key to cut down the bad effects on the land and the air. Automation technology is important here, and it helps make the way things are made much better. There is less waste and less energy consumption. When you use new control systems along with smart sensors, you can get the production line to work better. These things also make product quality stand out. They let the automotive industry and other fields keep up with green ideas. The new steps do more than just help the earth. There is also a boost in economic growth. The supply chain is stronger and ready for new changes that come with sustainable efforts.
Reducing Waste Through Automation
Automation is very important in cutting down waste during a production process. By using control systems and programmable logic controllers, industries get to be more exact and lower human error. This helps use up less stuff and make the work smoother. It also helps people keep getting better at what they do, which brings scrap rates down.
In the assembly process, machine learning, which is part of artificial intelligence, lets industries look at real-time data. This helps find where things are not working well and fix them. By using this in supply chain management, companies can make their work process better and boost production efficiency. These new ways support green and smart choices in many manufacturing systems.
Energy-Efficient Manufacturing Processes
Energy-efficient manufacturing is very important today because of digital transformation. When companies use automation technology, they can make their production lines better. This helps to lower energy consumption and also makes production efficiency go up. Machine tools that have programmable logic controllers can make real-time changes. This way, there is less waste and the product quality gets better. Using artificial intelligence lets manufacturing plants keep getting better over time. This helps these plants manage their workings costs while keeping up high standards. With the growth of flexible automation, manufacturers can stay strong in today's busy economy.
Challenges Facing the Future of Automatic Manufacturing
Navigating the future of automatic manufacturing comes with some big challenges. Security and data privacy worries have grown because more industrial automation systems are connected to each other now. On top of that, the high initial investment needed for automation technology can stop many companies from using advanced systems. It is important to find the right mix of human intervention and automated processes. This helps lower the risk of human error and helps boost production efficiency. Getting past these problems is important if we want to use automated manufacturing systems to their full power in this time of digital transformation.
Addressing Security and Data Privacy Risks
The use of automation technology in making products helps boost how much work gets done. But, it also brings up worries about safety and data privacy. As more systems link together through the Internet of Things, there are more weak points that someone could attack. It is very important to set up strong control systems. Using good encryption tools and smart cybersecurity steps can help stop problems like data attacks. When makers put the safety of important information first, they can get the good things from automated systems. This also keeps their work safe and keeps the trust customers have in them.
Managing High Initial Investment and Integration
High initial investment in automatic manufacturing can be hard for many businesses, especially with the fourth industrial revolution. But the long-term benefits usually beat these upfront costs. By using automation technology like industrial robots and programmable logic controllers, companies can make production smoother and lower labor costs. Tying in these systems with what they already use also brings more efficiency and helps with supply chain management. The ongoing push for digital transformation and process automation can lower money worries over time. It helps to boost product quality and increase production speed.
Conclusion
The future of automatic manufacturing is set to change the way industries work. This is happening because of new automation technology and the use of artificial intelligence. These tools will help make the manufacturing process faster and better. There will be less need for human intervention, and people will see a boost in production efficiency and product quality. But, there are some things to think about. One is the high initial investment that companies must make. Another is how to keep data safe. If people work on these problems, the benefits can be great. This change will help the economy grow and will support the long-term health of the industry.
Frequently Asked Questions
What industries benefit most from automatic manufacturing?
Automatic manufacturing gives many benefits to industries like automotive, electronics, aerospace, and pharmaceuticals. These fields use automation to be more exact, reduce the time it takes to make things, and cut costs. This leads to better efficiency and makes the product quality better in their manufacturing work.
How does automatic manufacturing impact job availability?
Automatic manufacturing changes the way jobs are offered. It takes over many simple tasks, and this can mean there are fewer of these types of jobs. But, it also brings new chances for people who work with technology. There is a need for skilled workers who can run and make the most out of these new systems. So, while the jobs may change, it does not only take jobs away. Instead, it shifts them, and people can get new work in areas that are linked to technology and automation.
Are small manufacturers able to adopt automation cost-effectively?
Small businesses that make things can use automation without spending a lot of money. They can start with simple options that can grow over time, such as cloud-based tools and low-cost robots. There are also grants and special offers that help businesses be more productive. These can help with the first costs, so companies can bring in automation without hurting their budgets.
What are the main barriers to implementing smart manufacturing systems?
The main things that stop companies from using smart manufacturing systems are high costs at the start, trouble joining new tech with what is already there, worries about keeping data safe, and the need for workers who know how to do the job. These problems can make it hard for people to get all the good things that come with advanced automation and IoT technologies.
How will AI shape the future of manufacturing in the United States?
AI is going to change how factories work in the United States. It will help make things faster and better. With the help of machine learning, and smart tools, factories will run more smoothly and need less money to do their work. AI also helps make product quality better and lets people fix things before they break. It gives us real-time choices so we know what is happening at every step. This will help all companies give their customers good products and save money at the same time.